历史上,氦气首先被应用于为气球与飞艇提供关键的升力,展现了其作为轻质气体的独特价值。时至今日,氦气已成为航空航天、尖端医疗、国防安全以及超导技术等高科技领域的核心要素,其战略地位在国防军工与高科技产业的蓬勃发展中愈发凸显,成为不可或缺的关键资源。
地球上的氦资源主要由两种稳定同位素构成:3He与4He。前者被视为地球内部自诞生以来便存在的古老见证,而后者则是放射性衰变过程的宝贵产物。尽管核反应技术能够合成微量的氦,但从工业应用的角度出发,氦气无法通过化学方法直接合成或制取,而是依赖于物理纯化技术,从含氦源中分离出不同纯度的氦气产品。
值得注意的是,空气中虽含有微量的氦气,浓度约为每立方米5.2毫升,但直接通过空气液化分离提取氦气的工业化尝试虽已存在,其产量却难以满足庞大的市场需求。因此,当前主流的氦气生产方式聚焦于天然气提氦技术,这一方法已成为保障全球氦气供应稳定的重要基石。
1 天然气提氦产业链
氦从生产到使用的产业链主要包括氦资源的发现、 生产、储存、运输、销售和用户等重要环节,见图 1。
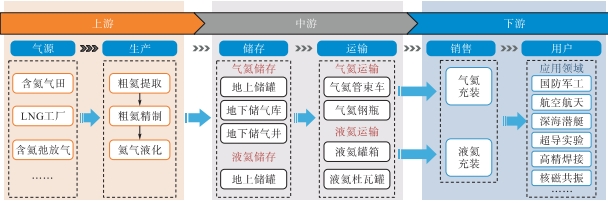
图 1 天然气提氦产业链示意图
氦气的来源多种多样,主要包括富含氦气的天然气田、以含氦天然气为原料的液化天然气(LNG)生产过程中产生的闪蒸气(BOG),以及以含氦天然气为制氢原料的化工厂所排放的弛放气等。表1详细列出了国内一些典型的含氦气源的组成成分。对于高氦含量的天然气,其氦气浓度可达到0.3%至8%之间,这样的高浓度使得从天然气中直接提取氦气在经济上变得尤为可行。而对于氦含量较低(不足0.1%)的天然气,尽管直接提取效益有限,但在大型天然气液化设施中,通过特定的工艺过程,氦气会被有效富集于闪蒸气(BOG)之中,进而从BOG中回收氦气成为了一种经济效益显著的方法。这种策略不仅优化了资源利用,还促进了氦气供应的多元化与可持续性。
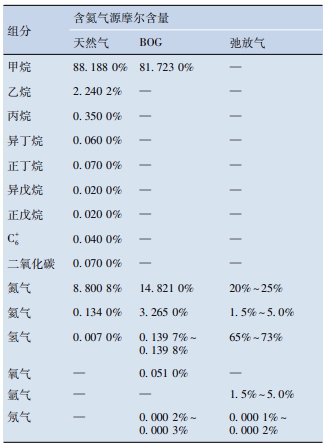
表 1 国内典型含氦气源组分表、
氦气的生产流程依其原料来源的不同,可细分为天然气提氦、BOG(闪蒸气)提氦及弛放气提氦等几种途径。而从生产步骤的角度来看,则涵盖了粗氦提取、粗氦精制、氦气液化以及氦的储存与运输四大环节。在粗氦提取阶段,主要任务是从含氦的原料气体中去除大部分如甲烷、氮气等非目标组分,从而初步获得粗氦气。随后,粗氦精制阶段则致力于将粗氦气进一步纯化,直至达到产品级别的氦气标准。氦气液化则是利用物理手段将气态氦冷凝为液态,便于高效储存与运输。
关于氦的储存,依据其物理状态的不同,可分为气态氦储存与液态氦储存两种方式,以适应不同的应用场景与需求。至于氦的运输,则是将生产好的氦产品安全、高效地送达最终用户手中的关键环节。根据运输距离的远近,氦产品可能会以气态或液态的形式被运送至各地的分销点,再由分销点进行二次分配,最终送达各个用户手中,确保氦气的稳定供应与广泛应用。
2 天然气提氦产业链技术发展现状
粗氦提取、粗氦精制、氦气液化、氦的储运等天然气提氦生 产技术路线见图 2。
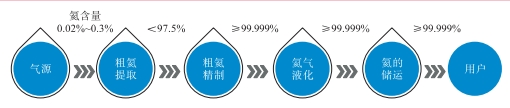
图 2 天然气提氦生产技术路线图
2. 1 粗氦提取
粗氦提取旨在将天然气中的氦气浓度提升至接近但不超过97.5%的水平。此过程常依托深冷处理或膜分离技术,或两者结合使用以达成目标。
深冷技术,基于天然气中各组分沸点温度的显著差异,特别是氦气具有远低于其他组分的液化温度,通过精确控制温度与压力条件,使天然气中的大部分非氦组分先行冷凝,而氦气则保持气态,从而有效实现氦气的分离与浓度提升。
另一方面,膜分离技术则利用了氦气分子在特定膜材料中具有高度渗透性的特性。该技术依据天然气中各组分在膜内溶解与扩散速度的差异,在膜两侧建立的压差驱动下,促使氦气以更快的速度通过膜层,实现与其他组分的有效分离与提纯。两种技术各有千秋,均能在粗氦提取过程中发挥重要作用。
2. 2 粗氦精制
粗氦精制是一个关键的工艺环节,旨在将粗氦气通过一系列纯化步骤提升至符合工业氦、纯氦、高纯氦乃至超纯氦标准的产品。由于起始的含氦气源成分各异,粗氦提取方法(如深冷或膜分离)的不同会导致粗氦中混杂的杂质种类及浓度存在显著差异。例如,采用深冷技术从特定含氦天然气中提取的粗氦常含氮气、甲烷、氢气等杂质,而膜分离技术则可能引入甲烷、乙烷、丙烷、氮气、氢气及二氧化碳等多种杂质。
面对氢气这一特殊杂质,因其液化温度与氦气相近且分子大小相当,传统的深冷、膜分离及变压吸附技术均难以直接实现氦氢分离。因此,粗氦精制过程中常采用催化脱氢技术,通过向粗氦中注入氧气,利用催化反应生成水蒸气来去除氢气。为确保氢气被彻底脱除,通常会设置多级催化氧化反应器并加入过量氧气,但这一过程中会伴随新杂质——水和氧气的引入。
随后,对于粗氦中剩余的水、二氧化碳、烷烃及氮气等杂质,变压吸附技术成为有效的脱除手段。该技术依据不同吸附材料对特定杂质的吸附选择性,如硅胶或氧化铝用于脱水,活性炭用于脱除二氧化碳,沸石则针对甲烷和氮气等,实现杂质的逐一去除。当吸附剂饱和后,通过降压反吹或抽真空等方式将杂质解吸,恢复吸附剂的吸附能力。在某些情况下,也会根据实际需要采用变温吸附技术。
特别地,若含氦天然气中混有氖气,前述技术均难以完全去除,氖气会随氦气纯化过程逐渐富集。在此情况下,工业上常采用低温吸附法,即将高压粗氦气冷却至液氮温度以下,利用低温吸附材料高效脱除氖气及其他如氩气、氮气等杂质,最终获得纯度高达99.999%以上的高纯氦产品。此外,根据解吸机制的不同,低温变压吸附技术也是一种可行的选择。
2. 3 氦气液化
氦气的液化过程,是一个在极端低温条件下将气态氦转变为液态的技术挑战,因为氦气以其极低的沸点著称,堪称自然界中最难以液化的气体之一。为了克服这一难题,工业界广泛采用了先进的液氮预冷结合多级膨胀制冷的氦循环液化技术。这种技术相较于传统的高压节流制冷循环,展现出了显著更高的制冷效率,同时极大地增强了氦气的液化能力,使得大规模、高效能的氦气液化成为可能。
2. 4 氦的储运
氦的储存与运输方式依据其物理状态(气态或液态)划分为气氦储运与液氦储运两大类。此外,还可依据储运设备所承受的压力等级区分为高压储运与低压储运系统;在储存形式上,则区分为地上储存与地下储存策略。对于气态氦而言,其主流储存方式是通过高压容器来实现,这些容器又可根据其移动性细分为固定式(如储罐)与可移动式(如高压储气瓶组管束、便携式气瓶等),它们专为安全高效地储存高压气氦而设计。而低压储存系统则常见于气囊设施中,这类设施主要用于回收低压环境下的残余氦气,以提高资源利用率。
3 总结
针对氦生产领域,我强烈建议加速推进氦分离膜技术的研发与实际应用,并同步提升大型氦液化器的设计制造能力,以优化生产流程,提高氦气提取与液化效率。在氦储运方面,应着力研发并广泛采用大型固定式及移动式液氦罐箱,以增强氦气储存与运输的灵活性与安全性。此外,还需强化氦产业相关标准与规范体系的建设工作,同时积极推动氦资源保护法的立法进程,确保氦资源的合理开发与利用,引领整个氦产业向更加健康、有序的方向迈进。
展望未来,我们的产品,作为航烨能源创新实力的集中体现,拥有显著的市场竞争优势。我们采用最先进的生产工艺与材料科学,确保产品的高效性、可靠性与环保性。我们的清洁能源解决方案不仅具备卓越的性能表现,还能有效降低能耗,减少碳排放,为客户带来显著的经济与环保双重效益。此外,我们注重产品的智能化与定制化服务,能够根据不同客户的需求与场景,提供个性化的能源管理方案,助力客户实现能源利用的最优化。