搅拌反应釜作为石油化工、生物化工及制药等工艺中的核心化工单元设备,其重要性不言而喻。通过深入解析智能高效磁力耦合式反应釜传动的结构原理、磁力矩的计算方法以及模糊控制系统的应用等关键内容,为磁力耦合传动的设计提供有益的指导。此举有望加速磁力耦合式反应釜的更新换代进程,并为其向更高参数领域的发展奠定坚实的技术基础。
搅拌反应釜在化工、石油化工、煤化工、生物化工及制药等多个工艺领域中,占据着至关重要的地位,作为不可或缺的化工单元设备。其核心优势在于,在工作转速下能够确保卓越的密封性能。特别地,磁力耦合式反应釜凭借其独特的优势脱颖而出,即彻底消除了动密封可能引发的泄漏问题,从而在高压、超高压、高真空、高转速及高温等极端操作条件下,实现了完全无泄漏的运行,极大地提升了工艺的安全性与效率。
1 系统工作原理
智能高效磁力耦合式反应釜的精妙设计涵盖了三大核心部分:一是磁力耦合式反应釜主体,融合了电动机、磁力耦合器、冷却水夹套、釜盖、釜体、传动轴、搅拌器及加热装置等关键组件;二是加热装置与釜体升降机构,为反应过程提供必要的热能调控与空间调整;三是集温度、压力与转速智能控制于一体的先进装置,确保操作精准无误。
(1)磁力耦合器的运作奥秘在于其独特的磁力相互作用机制。在静止状态下,耦合磁极的N极与S极相互吸引,呈直线排列,此时不产生磁力矩。然而,一旦主动机构在外力驱动下开始旋转,尽管从动机构因阻力暂处静止,但随着滑移角的逐渐增大并超越阻力矩的临界点,从动机构便紧随主动机构旋转。此过程中,从动机构(或主动机构)的单个磁极始终受到另一机构两个磁极的吸引与排斥力作用,形成类似齿轮联轴器的紧密啮合状态。通过隔套将从动部件及介质与外界隔绝,磁力线穿越隔套,实现无需物理接触的密封传动,彻底消除动密封的需求,确保无泄漏的安全运行。
(2)控制系统则是以高性能单片机为核心构建的模糊控制体系,它集成了多重先进功能。系统不仅实现了转速与电流的双闭环调节,确保转速稳定可靠;还采用了釜壁与釜内温度的串级调节策略,实现对温度变化的精细控制;同时,系统还集成了压力控制功能,全面监控反应釜的各项关键参数。此外,该系统还配备了上位机监控界面,使得操作人员能够直观、便捷地监控并调整反应釜的运行状态,极大地提升了操作的智能化与便捷性。
2 搅拌器冷模试验及应用
(1)关于工作原理的阐述,传统搅拌式反应釜面临两大挑战:一是釜内顶部气相区域常积聚未反应气体,影响反应效率;二是搅拌轴下方区域因搅拌力矩不足而形成搅拌死角。本研究创新性地提出并应用了空心搅拌器或与常规搅拌器结合的组合搅拌器设计,旨在解决这些问题。该设计通过空心结构促进气体与液体的更充分接触与反应,有效减少气相滞留,并强化搅拌轴下方区域的混合效果。
(2)在搅拌器冷模试验的装置与方法上,我们采用了公称容积为30升的透明有机玻璃釜作为实验容器,其内径设定为285毫米,以便清晰观察内部流动情况。试验中,空心搅拌轴通过联轴器与永磁内转子相连,而电动机则驱动永磁外转子旋转,实现动力的无接触传递。利用变频调速器,我们可以精确控制搅拌速度在0至1000转/分钟范围内变化。同时,通过吸气系统吸入空气并经空心轴、搅拌器喷入液相,实现气液间的充分接触与反应。实验过程中,我们利用多种精密仪器监测转速、搅拌功率、吸气量及吸入高度等关键参数,并设置了多个取样点以评估固体颗粒在釜内的分布情况。
(3)实验结论指出,空心搅拌器的应用显著改善了反应釜内的混合效果,实现了釜内上下两个方向的内循环流动。这一设计不仅有效解决了气相空间滞留问题,还显著减少了搅拌轴下方搅拌力矩为零的死角区域,从而提高了整体反应效率与均匀性。因此,空心搅拌器及其组合形式被证明是克服传统搅拌釜缺陷、提升搅拌效率的有效手段。
3 智能高效釜的研制测试
(1)转速调节系统。设计了转速、电流双闭环控制系统满足恒转速调节控制的要求。转速为外环控制电流为内环控制。如图 1所示。
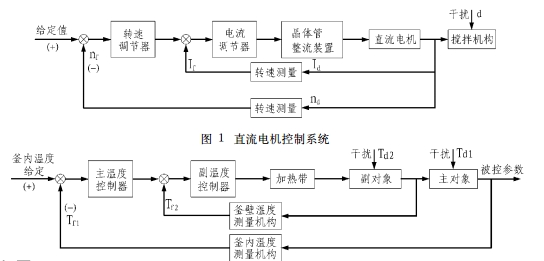
图1 温度串级控制系统
(2)温度调控系统方面,智能反应釜采用了先进的间接加热技术,即首先加热釜壁内的导热介质,再由这些介质将热量传递给釜内的物料。这种加热方式虽然有效,但也带来了系统控制上的滞后挑战。为此,我们引入了双偶采样与串级温度控制策略,该系统同时监测釜壁温度和釜内温度两个关键参数,形成了一套闭环调节机制,确保釜内温度能够精确控制在设定值附近,误差不超过±1℃。此外,系统还具备数字温度设定与超温自动报警功能,进一步提升了操作的安全性与便利性。
(3)在压力控制方面,智能反应釜采用了高精度的小型压力变送器作为测量元件,该变送器能够输出4~20mA的标准电流信号,供显示与控制单元使用。压力控制则通过固态继电器精确驱动电磁阀实现,确保了压力调节的快速响应与准确性。该压力控制系统不仅具备自动测量与定值控制功能,控制精度高达±0.1MPa,还设有数字压力设定与超压报警机制,有效保障了反应过程的安全稳定。
(4)至于通讯与信号传输,所有现场采集到的模拟信号首先经过专业的信号调理器转换成1~5V的标准电压信号,随后这些信号被统一送入I-7017模块,按照既定的通讯规约转换为RS-485格式的通讯信号,最终传输至上位机进行集中监控。上位机软件采用VB语言开发,界面友好,功能强大,每套系统可轻松实现对多达三台智能反应釜的实时监控与管理。
4 总结
综上所述,智能反应釜集成了先进的温度与压力控制系统,通过双偶采样与串级控制策略,实现了对釜内温度与压力的精准调控,确保了反应过程的高效与安全。同时,其通讯系统能够将现场信号实时传输至上位机,实现远程监控与管理,提升了操作的便捷性与智能化水平。这些创新技术的应用,不仅克服了传统反应釜的诸多不足,更为化工、制药等领域的生产提供了强有力的技术支持。
航烨能源在化工设备领域做出了显著贡献,专注于化工能源非标定制设备的技术服务,依托科研力量,提供反应釜、换热器等多种高质量非标承压设备,并支持定制服务,满足了科研与工业用户的多样化需求,推动了相关行业的技术进步与发展。