在传统生产环境中,柱塞泵常用于输送诸如水等常见液体,且在标准温度条件下运行稳定,鲜少遇到汽蚀困扰。然而,随着L-CNG(液化天然气汽车)加气站网络的快速扩张,低温柱塞泵的重要性日益凸显。在L-CNG系统中,LNG被安全储存在真空绝热的储罐内,维持饱和液态。但一旦受到热量吸收或压力下降的影响,LNG便会发生气化,形成气泡,这一过程即为气蚀现象,对泵体及系统构成潜在威胁。因此,低温柱塞泵在L-CNG加气站中的应用,不仅是对其技术能力的挑战,也是确保其在特殊工况下稳定运行的关键所在。
1 低温柱塞泵磨损、气蚀的原因
图1展示了低温柱塞泵的结构细节,其中泵缸内部的一个关键区域是活塞与进口阀门之间的空间,这一区域被称为泵腔或工作室。在LNG(液化天然气)的输送过程中,LNG首先通过进液管被引导至进液腔,随后经由进液头上均匀分布的多个进液孔(这些孔呈圆周排列)流入泵腔。进口阀门的启闭由弹簧机制精细控制,确保在适当时机开启进液孔,允许LNG顺畅地从进液腔流入泵腔。
值得注意的是,低温柱塞泵在设计上具备独特的润滑特性,其活塞环(即活塞边缘的密封装置)依赖于LNG自身进行润滑。然而,若LNG在进入泵腔前已含有气泡,这些气泡将阻碍正常的润滑过程,导致活塞环与泵腔壁之间发生干摩擦,进而可能损坏活塞环,甚至对缸套造成拉伤,即产生不必要的磨损。
为避免此类问题,LNG在正式进入泵腔之前,会先经过进液腔这一缓冲区。在进液腔内,LNG中的气泡得以有效分离,并通过回气管被安全地引导回LNG储罐的气相空间,从而确保进入泵腔的LNG纯净无气泡,保障低温柱塞泵的正常运行与长寿命。
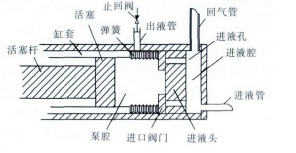
图1 低温柱塞泵结构
另一个关键挑战是气蚀现象,它发生在柱塞泵的吸液阶段。此时,泵腔体积扩张,形成局部低压环境,吸引LNG通过进液孔涌入泵腔。在此流动过程中,LNG的静压力需转化为动压以推动流动,并同时克服进液孔产生的摩擦阻力,这一过程伴随着压力的显著降低。若此压力降至低于当前温度下的LNG饱和压力阈值,LNG将发生气化,形成气泡。而当泵进入排液阶段,泵腔内压力骤增,这些气泡迅速受压破裂,其内气体迅速液化。此快速且剧烈的气泡破裂会触发周围高压LNG的急速汇聚,形成局部强烈的液击效应,即气蚀现象,这对设备寿命构成了严重威胁。
基于上述分析,我们可以归纳出导致柱塞泵泵腔内气泡产生的两大主要原因:
其一,热量传递效应。泵体及与其相连的进口管道(即连接储罐与柱塞泵的管段)可能将热量传递给LNG,导致泵内LNG温度上升并发生气化。
其二,压力损失机制。从储罐输出的LNG本身静压能可能不足以完全应对其在通过进口阀门及进液孔时所需克服的动能转换及摩擦阻力,从而导致压力显著下降。这种压力下降若达到足以使LNG气化的程度,便会引发气泡的生成。这两种情况均需在实际应用中予以高度重视,以确保柱塞泵的稳定运行与长寿命。
2 解决方案
确保柱塞泵在吸液阶段泵腔内维持完全液相状态,杜绝气相(气泡)的存在,是预防缸套磨损与泵腔气蚀的首要前提。为此,必须确保两大核心条件的实现:
首先,LNG在进入进液腔后,必须迅速且有效地完成气液分离过程,以防止任何气相(气泡)混入并随后进入泵腔。这一目标的达成,依赖于设计与安装阶段对工艺要求的严格遵循与精细控制,确保所有组件与流程均能有效促进气液分离,阻止气泡的形成与迁移。
其次,LNG在进入泵腔前,其液相必须具备足够的进口静压。这一静压水平需满足泵腔运行所需,以确保在LNG流经进液孔及克服相关阻力时,压力下降幅度不足以引发LNG的气化。因此,在柱塞泵的实际使用过程中,对工艺参数的精准控制至关重要,它直接关系到LNG静压的稳定维持与泵腔液相的纯净度。上述两个条件相辅相成,缺一不可,共同构成了保障柱塞泵稳定运行、延长设备寿命的关键防线。
2.1 气液分离
在图2所展示的LNG输送系统中,LNG自进液管流入进液腔,该腔室顶部特设回气管以应对LNG在管道传输过程中可能因吸热而发生的气化现象。这些气化产生的气体必须在进液腔内迅速分离,并借助回气管的有效引导,安全返回至储罐的气相空间。然而,若设计者在规划时过于追求管道的视觉美感,而未能充分考虑到回气管的坡度要求,便可能导致一个潜在问题:进液腔内分离出的气体(气泡)无法顺畅地沿回气管上升,进而随同LNG一同流入泵腔,最终引发柱塞泵的气蚀现象。
此外,值得注意的是,进液腔内的气泡与部分LNG会以混合物的形态进入回气管。在回气管内,这两相需进一步完成分离,而分离的关键则在于气、液两相之间的密度差异。若回气管被设计为水平安装或倾斜角度过小,将极大地阻碍气液分离过程的顺利进行,因为这样的设计不利于气泡的聚集与上升,从而增加了气泡随LNG进入泵腔的风险。
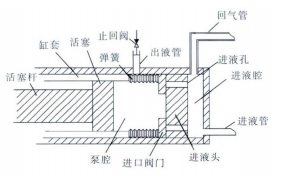
图 2 柱塞泵回气管水平设置
为了确保回气管能有效引导进液腔内产生的气体垂直向上流动,并顺利返回至储罐的气相空间,回气管的安装倾角成为了一个关键参数。基于实践经验,我们推荐在条件允许的情况下,回气管的倾角应大于5°,如图3所示。这一设计利用了气体在液体中产生的垂直向上浮力,其中浮力沿回气管方向的分力即为推动气体向储罐气相空间流动的主要力量。
同时,为了保持回气管内气体流动的顺畅性,储罐底部回气管阀门与柱塞泵进液端之间的水平距离被限制在不宜大于5米的范围内。这意味着回气管两端的最大落差将不超过0.44米(基于5°倾角的计算),这样的设计对储罐基础的高度要求相对较低,无需进行特殊加固或处理,从工艺角度来看是完全可行的。
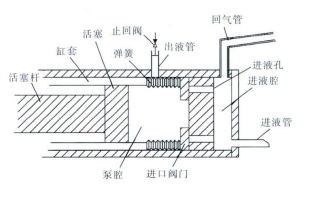
图 3 柱塞泵回气管有一定倾角设置
进液管设计时的倾角设置同样具有其重要性,这一措施旨在促进进液管内气体的自然上升与及时分离,使其能够沿着进液管顺畅地流回储罐中。这样做不仅能有效减轻进液腔内气液分离的负担,还能减少因气体滞留而可能导致的操作问题。
另外,无论是进液管还是回气管,其布局均应避免出现凹凸不平的结构。这种平滑无阻的管道设计是至关重要的,因为它能有效防止气堵或液堵现象的发生。气堵指的是气体在管道内积聚无法顺畅流动,而液堵则是液体在管道中堵塞,两者都会影响LNG的正常输送,甚至可能对系统造成损害。因此,在管道设计与安装过程中,务必确保管道的流畅性,以避免上述问题的出现。
2.2 足够的进口静压
为了有效防止LNG在输送过程中因压力降低而气化产生气泡,采取的策略是给LNG施加足够的进口静压。这一措施确保了LNG的温度始终低于其在当前压力下的饱和温度,从而使LNG处于过冷状态。在这种状态下,即便LNG流经进液孔时经历了一定的压力降低,其剩余压力仍然高于该温度下的饱和压力阈值。因此,LNG能够保持稳定的液态,不会因压力下降而气化形成气泡,从而保障了输送系统的安全与稳定。
静压余量的获取对于防止LNG在输送过程中气化产生气泡至关重要。以下是实现这一目标的主要途径:
利用储罐的液位高度:尽管LNG的密度相对较小(例如,密度为480 kg/m³时),1米液位高度仅能产生约0.0047 MPa的位压,这对于柱塞泵所需的0.034 MPa静压余量来说贡献有限。更重要的是,这部分位压还需用于克服LNG在管道中流动时产生的阻力。流速是影响阻力的关键因素,流速越大,阻力越显著。因此,通常建议将进液管和回气管的流速控制在0.3 m/s以下,以避免湍流状态导致的阻力急剧增加。为减少流动阻力,建议采用独立的进液管设计,避免与其他设备共用进液管,从而减少三通管件的使用,降低整体阻力。
对储罐进行增压:LNG在储罐中长时间储存后会达到饱和状态,此时储罐内的压力即为LNG的饱和压力。随着LNG温度的升高,储罐压力也会相应增加。为了确保柱塞泵进口处的LNG压力始终高于其饱和压力至少0.034 MPa,需要对储罐进行增压。这样做可以确保在克服管道阻力后,LNG在泵腔内仍能保持液态,避免气化现象的发生。然而,值得注意的是,对储罐增压后,储罐内的LNG会逐渐冷却并液化气相,导致压力逐渐下降。因此,建议增压值应大于0.20 MPa,以确保LNG在输送过程中始终拥有足够的静压余量。
3 总结
为确保LNG输送中避免气化气泡,需通过液位高度和利用储罐增压来提供静压余量。液位高度虽贡献有限,但有助于克服部分流动阻力。主要依赖对储罐的增压,确保LNG压力高于饱和压力,并预留足够静压余量。同时,优化管道流速和独立进液管设计,进一步减少流动阻力,保障输送安全。
航烨能源在LNG输送与储存领域展现出卓越贡献,通过技术创新提升静压管理效率,确保LNG在输送过程中稳定不气化。其独立进液管设计与储罐增压技术,有效降低了流动阻力,提升了系统安全性与稳定性。