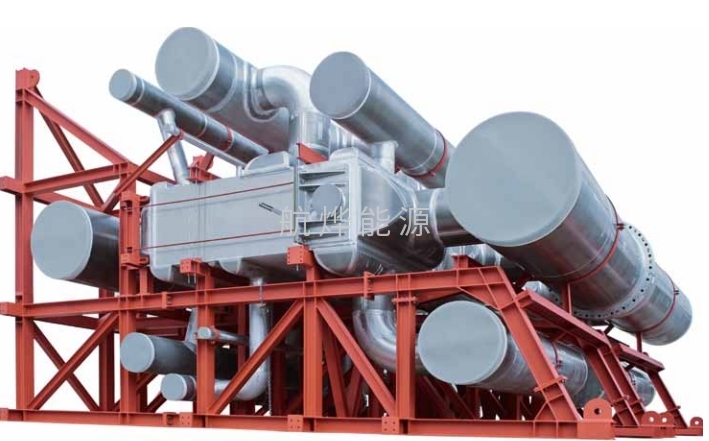
针对氨低温过冷系统的探索与实践,其核心架构围绕一台高效能的2.5kW/4.5K氨制冷机及其配套的过冷测试分配系统精心构建。该系统突破性地融合了冷压机技术,成功在极端低温和低压条件下,对液氨储罐实施真空与减压处理,实现了液氨温度低至3K的过冷壮举。 详述这台专为大型应用量身打造的2.5kW/4.5K氨制冷机,其核心技术源自先进的Claude制冷循环,该循环机制巧妙地串联了两台透平膨胀机,并辅以液氮预冷系统,以最大化制冷效率。
在流量与压力控制方面,该制冷机创新性地结合了透平膨胀机与节流阀的双重优势,实现了精细调控。
在纯制冷模式下,其卓越表现可达2.5kW/4.5K的制冷能力;若转换为纯液化模式,则能以每小时550升的速率高效生产液氨。
压缩机作为制冷循环中的压力核心,其排气压力设置借鉴了EAST氨低温系统的成熟经验,确保在制冷模式下高压侧压力稳定在20bar。随后,这股高压氨气历经水冷、除油、干燥等多重净化步骤,压力微调至19.5bar后,正式进入冷箱,开启其制冷循环的精密旅程。 进入冷箱系统的氦气,在维持310K温度的同时,面对高于80℃的高温区域,巧妙利用液氮与低压冷氨气,通过板翅式换热器HX1与液氮槽HX2的协同冷却作用,有效降温。随后,高压氦气在HX3内与低压冷氨气进行热交换,温度骤降,并分流至透平路与节流路。
透平上,高压氦气经透平膨胀机T1绝热膨胀,温度再降;随后与高压路氦气汇聚于HX5,再次接受低压冷氦气的冷却及T2的二次绝热膨胀,实现深度降温后回归低压路,既补充冷量又平衡流量与温度。主流路氨气穿越HX7后继续降温,进入T3节流降温;最终,在HX8完成终极温度调整后,通过节流降压至1.25bar,平稳进入液氨槽储存。
上述流程概览详尽描绘了2.5kW/4.5K氨制冷机冷箱内部的复杂而精密的工作机制,具体细节请参见附图1以获得更直观的理解。
图1 2.5kW/4.5K氦制冷机冷箱流程简介
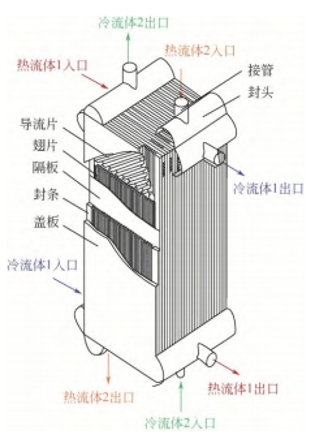
图2 铝制板翅式换热器结构示意图
铝制板翅式换热器,凭借其非凡的换热效能与紧凑的构造设计,在众多换热设备中脱颖而出。其小巧的体积与轻盈的质量,加之单位体积内卓越的换热面积,使之成为氦低温过冷技术中高效传热的理想选择。
在构建氦低温过冷系统时,我们始终致力于追求传热效率与压降控制的完美和谐。通过精心设计的优化方案,我们力求实现换热器体积的最小化,从而不仅减小了冷箱的整体尺寸,还降低了生产成本,减少了空间占用,同时确保系统既能在低温下高效传热,又能有效控制压降,满足双重性能标准。
鉴于氦低温过冷系统对真空绝热技术的依赖,冷箱内铝制板翅式换热器的密封性能显得尤为重要。为此,我们倾注大量精力优化钎焊工艺,持续提升换热器的钎焊品质,力求将任何潜在的内外泄露风险降至最低,确保换热器在极端运行环境下依然能够稳定可靠地工作,为整个系统的持续高效运行提供坚实保障。
相对同行,我们不仅能加工制造,技术团队还能针对定制需求研发板翅式换热器,助力客户降本增效!