公司日前合作的油船油气深低温冷凝回收项目低温氮膨胀制冷机部分,针对含氮气、甲烷、乙烷等混合气体,流量:20 Nm3/h(273 K,101325 Pa),设计适合于船舶空间的冷凝工艺流程,搭建试验验证平台,实现碳氢类总烃油气回收率≥95%、尾气排放符合相关标准的目标。
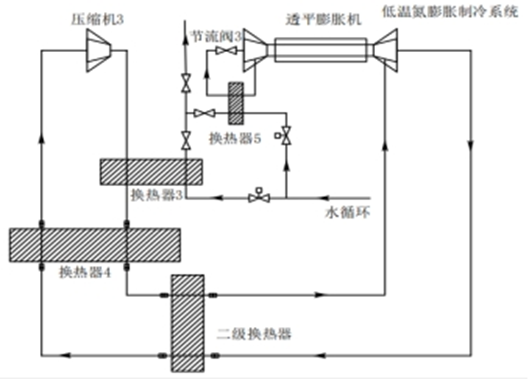
图. 低温氮膨胀制冷系统
针对20-40 m3/h CH4和N2混合气(CH4:60%, N2:40%,室温,进气压力5bar绝压),要求能实现绝压5 bar下的 CH4液化,并有1K以上的过冷度。就是把第一级预冷后的低温混合气体(-75℃氮气和甲烷的混合气)冷却到-150℃左右,再进入高效低阻翅片板翅式换热器进行降温与液化测试。为了保证VOC处理系统满足初始要求(如:烃类回收率、-75℃混合气冷却到-150℃左右等)。VOC处理系统二级机组高速离心压缩机必须提供足够的压头和流量的氮气。供膨胀机来膨胀制冷,使得制冷量(VOC冷却消耗冷量和系统漏热等)与制冷温区(在一定压力下,VOC气体需要达到一定温度,才能满足烃类液化去除需求)需满足特定要求。系统设备如下图所示。

图. 低温氮膨胀制冷系统 图. 高速电机
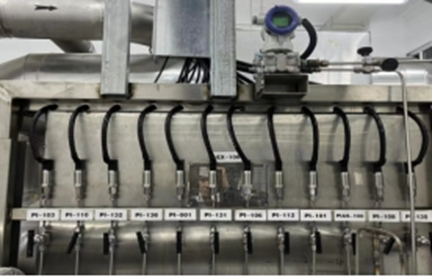
图. 膨胀机制动端 图. 压力变送器
原料气(储罐、钢瓶内),经过高精度自动减压阀门,经过冷却器 E-100-2-2(复叠制冷提供冷源),被冷却到-75℃,然后进入气液分离器 V-1,部分气体被冷却成液体(留在气液分离器 1 内),剩余未被液化的气体(CH4 和 N2)进入 HX-2 被冷却到-160℃(氮气制冷机提供冷量),进入气液分离器 V1-2,大部分 CH4(留在气液分离器 2 内),剩余气体 N2 和 CH4(小于 5%)尾气处理后排入大气。当气液分离器 1、气液分离器 2 内的液面达到一定高度时,分别打开排液阀门将液体输出。
试验装置主要设备包括:3+1 台换热器(第四台为定制换热器)、1 台复叠式制冷机组、1 台氮气制冷机组、2 个气液分离器、1 套 PLC控制系统(数据采集与存储系统)等。此外,由于重烃类组分(C4, C5+)由于其液化点较高,普通冷处理方式(如水冷、制冷剂冷却)极易液化分离处理,故不属于VOC冷凝低温系统技术难点,因此实验过程中不考虑此类重烃成分,仅对较难液化处理的甲烷、乙烷、丙烷等轻烃组分的液化分离工艺展开试验。经配气稳压方案确认、测量仪表选型、PLC自控、尾气末端处理工艺、抽真空降温环节考虑等,确定了如下图所示的油气冷凝回收试验系统PID图。图为测控界面截图。
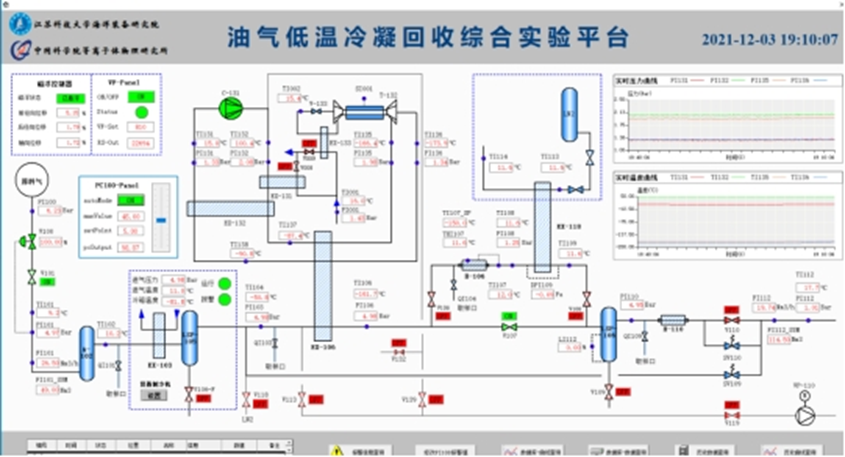
图. 测试界面
原油船油气冷凝回收系统为预冷单元、双级复叠制冷循环与低温氮膨胀制冷循环组成。建立了原油船油气冷凝回收工艺流程,油气冷凝、分离回收过程为:
第一阶段:油气进入冷凝回收系统后,首先经过预冷器冷凝放热,温度达到4℃左右,通过集液器1,冷凝干燥除去原料气中的水分和部分高沸点组分。
第二阶段:油气进入一级换热器,冷却降温至-75℃左右,通过气液分离器1后,丙烷、丁烷和大部分的乙烷组分被冷凝回收。
第三阶段:油气进入二级换热器,冷却降温至-160℃左右,通过气液分离器2后,完成包含甲烷在内的轻烃组分冷凝回收。
如图低温氮膨胀制冷系统流程仿真图所示,低温氮膨胀制冷系统中换热器3和换热器5通过水冷的方式带走热量,通过分液器与集液器完成介质水的分液与集液,分液器分液比例为1:1,氮气通过膨胀机所做的膨胀功Q-8传递给压缩机,氮气被压缩后,经过换热器5,通入节流阀后返回压缩机,完成循环。
图. 低温氮膨胀制冷系统流程仿真图
油气冷凝回收系统的油气进口成分如表6,环境温度为30℃,进口压力为5 bar,油气流量为20 Nm3/h。通过计算比较,本课题选用P-R方程作为油气系统的热力学计算方法,适用于这种拥有较宽温区的烃类混合物。按照油气回收目标设定冷凝温度为4℃、-75℃、-160℃,并利用换热器模型模拟油气冷凝回收系统流程。
氮透平膨胀机是系统-80℃以下低温冷量的唯一来源,其可靠性与性能直接影响整个系统的稳定运行。氮透平膨胀机具有转速高、温区低、无油等特点,一般采用静压气体轴承(需要消耗高压轴承气)或动压气体轴承(承载力与刚度低于静压气体轴承)。由于气体轴承的承载力、刚度等都较低(比油轴承低一个量级,比滚轴轴承低的更多),不合适未来船(船用具有:扰动大,颠簸,反复晃动等特点)用多扰动场合。因此研发了基于陶瓷球轴承(微脂或特殊润滑形式)的氮透平膨胀机,具有承载力高、刚度大、抗干扰能力强等特点,适合船用复杂运行工况。
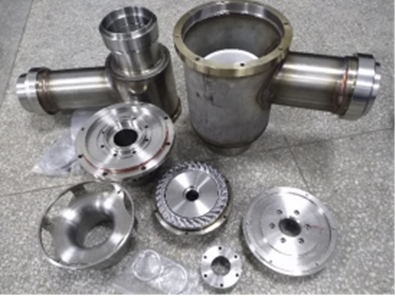
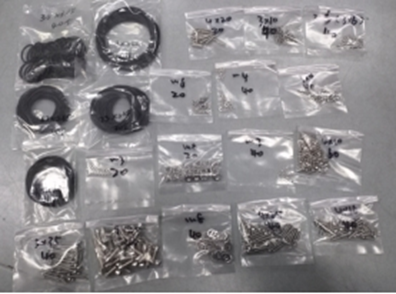
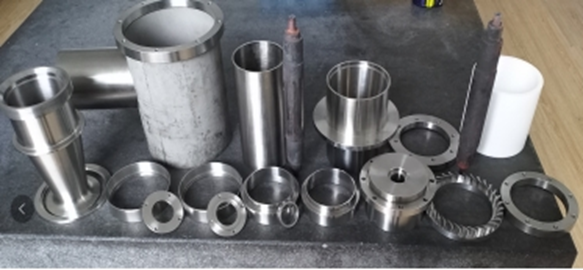
图. 氮透平膨胀机部件
透平膨胀机设计参数设计为:
表. 膨胀机计算参数初步选取
透平膨胀机 | 工质 | 流量 | Pin | Tin | Pout | Tout | 效率 | 制冷量 |
实际选取参数 | 氮气 | 310 g/s | 1.80 bar | 114.5 K | 1.1 bar | 103.2 K* | 72.9%* | 3.44 kW |
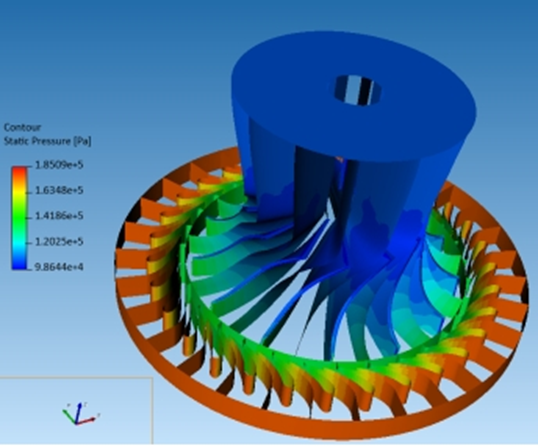
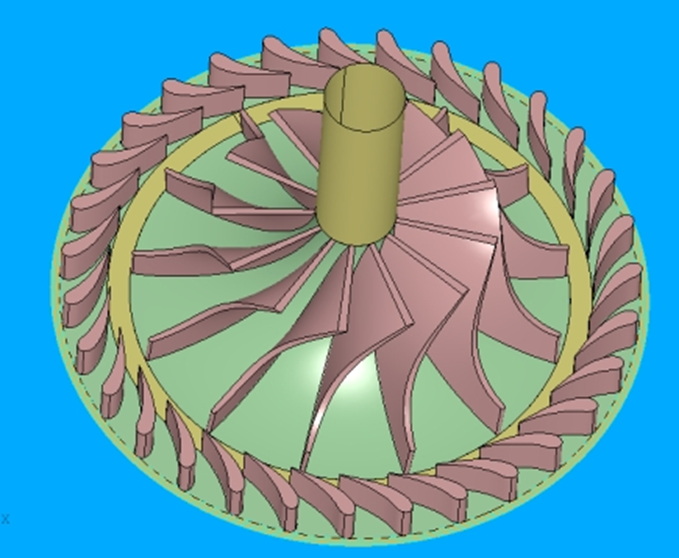
图. 膨胀轮流道模拟压力分布图 图. 膨胀轮流道3D造型图
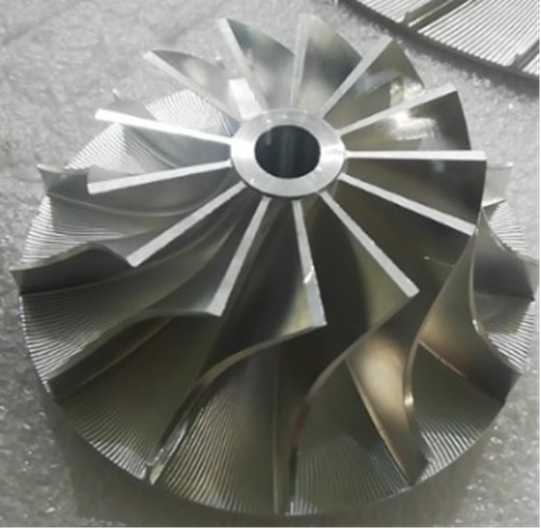
图. 膨胀轮实物图
制动叶轮主要目的是把膨胀端的膨胀功给消耗掉,使得膨胀机转子达到功率平衡,并抵消膨胀端部分轴向力。使得转子整体的轴向力降低,降低转子对轴承系统的负荷,增加轴承的寿命。由于制动叶轮不考虑运行效率等因素,为了方便加工与运行平稳(变工况范围宽等),采用直叶片结构形式。具体如下图所示。
图26. 制动轮设计结果实物图
本公司对膨胀机的流道部分进行了设计、分析与优化,最终得出较好的流道效率和工况。设计结果,膨胀机出口温度最低101.05 K(进口温度是116 K),满足低温冷凝温度103.2 K的温度;制冷量4.5 kW(80%的余量),满足VOC处理系统对冷量的需求。