在追求实现碳中和目标的背景下,能源结构的转型成为了目前重大的挑战。化石能源作为当前能源体系的主体,对其进行清洁和高效利用尤为重要,尤其是发展和优化化石能源的使用方法。甲烷作为最清洁的化石能源之一,对其进行高值清洁利用被视为能源转型中具备良好发展前景的关键技术之一,受到了广泛关注。H2作为能源结构转型的重要基石之一,由于其燃烧不产生CO2,是理想的清洁能源。然而,目前工业规模上的H2生产仍主要依赖于化石能源,包括甲烷水蒸气重整(SMR)、煤气化和石油重整等。其中主要的制H2工艺是SMR工艺,该工艺中甲烷与水蒸气在650~1000℃、0~0.5MPa以及催化剂存在下反应得到CO和H2,然后通过水汽转换反应得到CO2和H2。
为消除SMR工艺中CO2的排放,需要结合碳捕集和封存(CCS)技术,但成本上涨了约60%。在碳中和背景下,SMR工艺的成本受到天然气和CO2排放成本的严重制约。根据2020年《British Petroleum世界能源展望》,未来30年内,天然气作为最清洁的化石能源,其消费量将持续增长,且增长量主要用于制H2。因此,有必要发展绿色低碳的甲烷制氢工艺
甲烷制氢可以从水汽重整制灰氢转变为甲烷裂解制蓝氢。甲烷裂解将甲烷分解为H2和固体碳,该反应不直接产生CO2,不需要CCS技术,可简化工艺流程。
相较于SMR工艺,甲烷裂解制氢工艺的主要优点为制氢过程可以减少75%以上的温室气体排放,即使天然气作为热源,甲烷裂解制氢工艺的碳排放仅为2~3kg/kg,远低于SMR工艺。甲烷裂解制氢工艺制备出的H2纯度较高,同时具有生产多种高价值碳材料的潜力,如从无定形碳黑到高度专业化的石墨烯、碳纳米管和纤维等,可广泛用于橡胶、电池和芯片等领域。

表1 甲烷裂解制氢工艺的对比
催化甲烷裂解制氢是一种利用催化剂来促进CH4分解成H2和碳材料的过程。目前,催化甲烷裂解工艺的研究主要集中在两个关键领域:一个是开发可行的催化剂以降低反应活化能从而降低反应温度,提高CH4转化率和H2选择性,另一个是对碳材料进行调控和分离。在催化甲烷裂解制氢中,反应器通常采用流化床结构。甲烷首先通过进料口进入流化床反应器(图1),并由气体分散器分散,随后气体流经固体颗粒,使固体颗粒保持悬浮状态,形成流化床。反应过程中,热量和质量在流化床内迅速传递,有助于维持反应的稳定性和效率。反应后的气体与固体颗粒在流化床顶部分离器中分离,而分离后的催化剂通常被回收到反应器底部,再次参与反应过程,反应后碳材料通过碳材料分离调理装置分离。流化床反应器因可以通过粒子的持续运动减轻积碳,成为催化甲烷裂解制氢工艺的常见反应器。由于催化剂能够降低CH4分解所需的能量,从而使得反应更加高效。在流化床中催化甲烷裂解制氢工艺相较于传统的非催化甲烷裂解制氢,工艺具有反应速率快、选择性高和碳材料质量较好等优点,但由于该工艺只能减轻积碳,催化剂仍然容易失活,需要频繁更换和再生,操作成本较高,使得该技术在商业化应用中面临挑战。

图1 流化床反应装置示意图
等离子体甲烷裂解制氢工艺
等离子体甲烷裂解制氢工艺是通过向气体(通常是甲烷和可能的惰性气体混合物)施加高能量(如高电压电流、微波和射频能等),使气体电离成等离子体然后利用等离子体的高温特性对甲烷进行裂解制氢的工艺,该装置示意图见图5。同时可以通过调控反应条件,如温度、压力和等离子体特性,实现对产物组成和比例的精密控制,从而获得H2和高质量碳黑、碳管和石墨碳等多种碳材料。等离子体可分为热等离子体和非热等离子体两大类。根据等离子体类型的不同,甲烷裂解制氢效率和碳产物的类型也不同。不同等离子体裂解制氢工艺对比见表2。由表2可知,热等离子体工艺通常在700~4700℃的温度下运行,具有CH4转化率高、反应速率快等优点,适用于大规模生产碳黑,但其能耗较高,并且难以精确控制碳材料的结构和组成。非热等离子体工艺可以在低于900℃的温度下运行,可以生产碳纳米管,能耗较低,对设备的要求也较低,但相对于热等离子工艺,其产物的产率较低,技术复杂度也更高。耦合热等离子工艺可以在900~1100℃的条件下得到较高的H2产率和石墨碳。
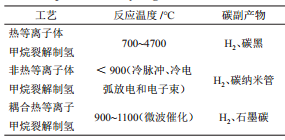
表2 不同等离子体甲烷裂解制氢工艺对比
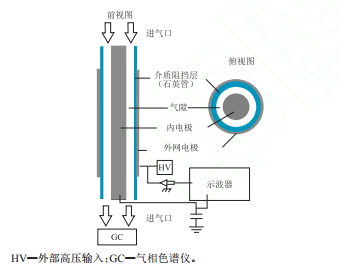
图5 等离子体甲烷裂解制氢装置示意图
热等离子体甲烷裂解制氢工艺
在热等离子体中,重粒子和高能电子都具有明显的反应能力,使热等离子体裂解制氢工艺具有较高的CH4转化率,被较多公司采用。在20世纪90年代,挪威克瓦纳集团公司致力于开发直流等离子体技术,联合生产碳黑和H2。在热等离子体甲烷裂解制氢工艺中的温度超过5000K,电离率高到足以引起焦耳加热,尤其适用于吸热过程,该工艺长期以来一直被应用于碳氢化合物的分解,该装置示意图见图6。实验在等离子体反应器PlasGas中进行,反应器顶部安装了水/氩复合电弧稳定等离子炬。在实验开始前将反应器缓慢预热(升温速率为约60K/h)至1200K后打开等离子体炬,然后注入甲烷和氦气与等离子体混合。甲烷气体的反应产物随后被导入淬火室水冷至600K。冷却后的气体流经能够在高达800K温度下运行的高温陶瓷过滤器分离出固体碳颗粒。随后,气体通过喷水泵排出,该泵同时充当洗涤器,去除残留杂质。PlasGas反应器旨在充分混合等离子体与处理物质,保证足够的停留时间,以促进能量有效转移,通过这种方式获得热力学平衡的气态反应产物。甲烷的流量和等离子体的类型会对碳的生长产生影响。甲烷和其他碳氢化合物裂解过程中碳颗粒的形成机制,并将该机制分为两个步骤:低温颗粒生长和高温退火。碳颗粒的形成机理表明,等离子体内部流体(反应气体和等离子体)的流动对碳颗粒结构具有重要意义。此外包括H2、碳黑形成的实验研究,基于热力学平衡计算、化学动力学模拟等相关理论基础预测并设计了等离子体甲烷裂解制氢的反应器,使用该反应器合成的碳黑具有比表面积大、导电性高、结晶性好和石墨化结构高等优良性能。
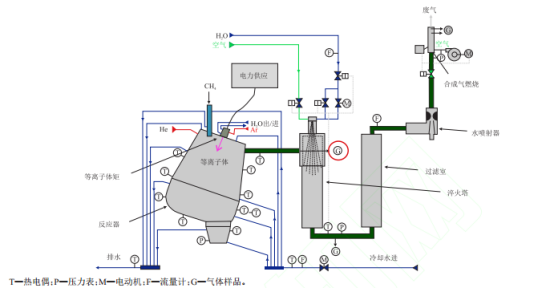
图6 热等离子体甲烷裂解制氢装置示意图
耦合热等离子体甲烷裂解制氢工艺
由于反应过程中存在热损失,与其他制氢工艺相比,等离子体甲烷裂解制氢过程的能源效率相对较低。因此,在过去的十几年中,通过重新设计裂解反应器和采用多样化热源,发展了多种裂解制氢工艺。一些新兴工艺采用多种热源的组合,例如微波与等离子体相结合、冷脉冲等离子体和冲击波相结合等,以最大限度地提高H2产量。同时,这些技术还利用传热介质,如熔融金属和熔盐,以提高从热源到反应物的传热速率。
非热等离子体甲烷裂解制氢工艺
除了热等离子体甲烷裂解制氢工艺外,非热等离子体甲烷裂解制氢工艺通常在低于900℃的温度下运行,因此被广泛应用于裂解天然气以生产H2和固体碳。相对于热等离子体,非热等离子体具有更高的能源转化效率和更低的冷却需求。目前,甲烷裂解制氢多采用冷脉冲非热等离子体技术、冷电弧放电非热等离子体技术及电子束非热等离子体技术。
熔融介质法甲烷裂解制氢工艺
熔融介质法甲烷裂解制氢是一种利用高温下的熔融态媒介(通常是熔融金属或熔盐)作为催化剂的反应过程,反应装置见图8。熔融状态下的金属或盐具有良好的流动性和导热性,甲烷在熔融介质中以气泡的形式参与反应,裂解为H2和固体碳,由于熔融介质与固体碳的密度差使碳材料能够漂浮在熔体表面,因此避免了固体催化剂积碳失活的问题同时也降低了碳的分离难度。
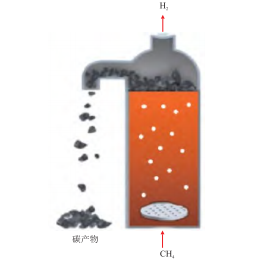
图8 熔融介质法甲烷裂解制氢装置示意图
气体分散工艺
在熔体中,甲烷以气泡形式存在,与熔盐接触的仅有气液界面和扩散到熔体中的少部分甲烷分子。对于催化性能并不出色的熔融盐,减小气泡直径、增大气液接触面积是最大程度发挥其催化性能、提升CH4转化率的关键。
碳分离工艺
由于熔融金属具有高催化活性,裂解产生的固态碳会不断积聚影响反应持续进行。尽管通过改进曝气头设计和优化反应器结构取得了一定的成功,实现了CH4的高转化率和碳材料的有效分离,但如何在保持高CH4转化率和碳分离率的同时,进一步降低能耗,提高系统的整体能量效率,仍然是重要挑战。未来发展方向应着重于以下几个方面:(1)继续探索更高效的气体分散技术和碳分离机制,以提高甲烷转化率和碳材料的收集效率。(2)设计能效更高的反应器和优化操作策略,减少能量损失,提升整个系统的热利用效率。(3)开发新型熔融介质,改善其催化性能和热稳定性,同时降低反应温度和环境影响。
随着能源结构转型的加速,清洁高值利用天然气势在必行。甲烷裂解制氢工艺可以同时制得高纯度H2和碳材料,具有良好的发展前景。流化床和微波辅助技术提高了CH4转化率并延长了催化剂寿命,但催化剂的快速失活和高能耗限制了其工业化进程。等离子体裂解甲烷制氢虽然具有高CH4转化率和反应速率,但受到高能耗和电极积碳问题的制约。熔融介质法裂解甲烷制氢因解决了催化剂失活和碳材料分离的问题,展现了在大规模甲烷资源处理和降低能源消耗方面的潜力。面对现有技术的局限性,未来的研究和发展趋势应聚焦于以下几个方面:(1)进一步优化催化剂和反应系统设计,以提升CH4转化率和延长催化剂寿命。(2)解决等离子体甲烷裂解制氢中的高能耗和电极积碳问题,通过技术创新降低能源输入。(3)对于熔融介质法裂解甲烷制氢,寻找更有效和稳定的熔融媒体及催化剂,同时优化工艺以提高效率和经济性。从目前的研究和发展趋势来看,熔融介质法裂解甲烷制氢因具有独特的操作模式和易于碳分离的特点,在处理大规模甲烷资源和优化能源消耗方面具有巨大的潜力。随着可再生能源如太阳能、风能的发展,将其与甲烷裂解制氢工艺相结合,不仅能显著提升能源效率,还将推动整个过程的无碳化,为实现环境的可持续发展提供强有力的支撑。可再生能源的引入,尤其是在熔融介质法裂解甲烷制氢中,有望实现从高温加热到高效甲烷转化的闭环,减少对化石燃料的依赖,并大幅减少整体碳足迹。总之,结合可再生能源的熔融介质法裂解甲烷制氢技术,不仅能够提升能源效率和经济性,还有助于实现工艺的无碳化和环境可持续发展,未来在能源结构转型中具有重要作用和广阔的发展空间。