氢能,以其绿色无污染与高效储能密度的特性,正逐步成为推动我国达成“碳达峰”与“碳中和”目标的关键力量。随着政策红利的不断释放,氢能产业的快速发展已蓄势待发。然而,当前面临的挑战在于如何实现氢能的低能耗、大规模储存与运输,其中,混合冷剂氢液化技术被视为突破这一瓶颈的有效途径。
深入剖析当前的混合冷剂氢液化技术趋势,可见不同研究者依据制冷温区的特性,设计了多样化的技术路径,并持续优化混合冷剂的成分配比,以达到更优的液化效果。这一技术领域的进展,不仅彰显了其创新活力,也为氢能的高效、大规模储运提供了坚实的技术支撑。
氢能作为零碳排放的能源形式,其高储能密度、广泛来源及环境友好性,使其成为可再生能源高效利用与长周期储能的理想选择。在氢能储运方面,现有的方案主要包括气态、固态及液态储氢三种模式。
气态储氢,虽便捷但受限于低储氢密度与高压运输风险,主要适用于短途小量运输。固态储氢,虽前景广阔,但目前仍处于研发初期,技术成熟度有待提升。而液态储氢,尤其是液氢储氢,以其高储氢密度、低储运压力、高汽化纯度及经济的中长距离运输成本,成为解决氢能大规模、长期储运难题的首选方案。相较于有机液态储氢与氨储氢,液氢储氢无需复杂催化剂,且全程绿色无污染,优势显著。
因此,进一步推动混合冷剂氢液化技术的发展,不仅能够加速氢能储运技术的革新,还能为氢能的大规模商业化应用奠定坚实基础,助力我国能源结构的绿色转型与可持续发展。
1.氢液化循环
氢气的标准沸点设定在极低的-252.8℃,而其临界温度更是低至-239.96℃,这一特性使得氢气成为继氦气之后,液化难度最大的气体之一。工业界为了应对这一挑战,普遍采用先进的低温深冷技术,将氢气冷却至接近绝对零度的-253℃左右,从而实现在常压条件下的液态存储。
现行的工业氢液化设备,其核心原理深深植根于三种经典的循环过程:氢气Linde-Hampson循环、氦气逆Brayton循环以及氢气Claude循环。这些循环不仅优化了氢气的液化效率,还通过精心设计的流程,在循环过程中巧妙地融入了正仲氢转化步骤。这一步骤至关重要,它确保了液氢能够长期稳定储存,满足了各种应用场景对氢能长效保存的需求。
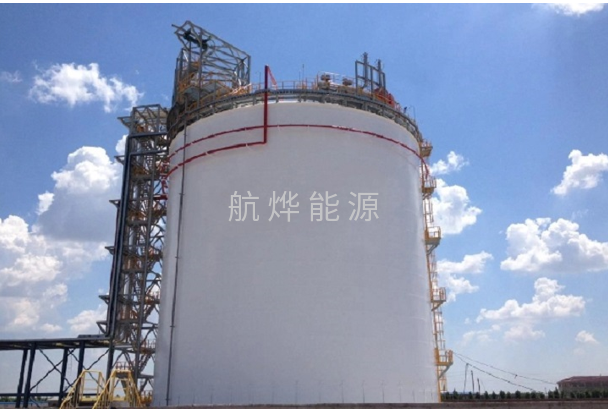
1.1预冷型Linde-Hampson循环
德国的Linde与英国的Hampson各自独立地提出了压缩与节流相结合的空气液化循环方法,这一创举为后续的氢气液化技术奠定了基石,该流程因而得名Linde-Hampson循环。鉴于氢气独特的低转化温度(204K),常温下仅凭节流效应难以直接实现其液化,故需对氢气进行前置冷却处理,其原理如图1所示。
1898年,英国科学家James Dewar率先采用液态二氧化碳与液态空气作为冷却介质,对压力高达20MPa的氢气进行预冷,随后再通过节流过程成功制取了液氢。这种预冷型的Linde-Hampson循环装置,以其数量稀少、结构紧凑、运行稳定的特点,成为了工业界早期氢液化技术的首选。
然而,随着技术的发展,Linde-Hampson循环因其显著的能耗问题而逐渐式微。该循环的能量利用效率,即理想最小理论液化功与实际消耗功之比,仅维持在3%至3.4%的较低水平,这极大地限制了其在工业上的广泛应用。因此,当前工业界已普遍转向更为高效节能的氢液化技术,而传统的高能耗Linde-Hampson循环则逐渐被淘汰。
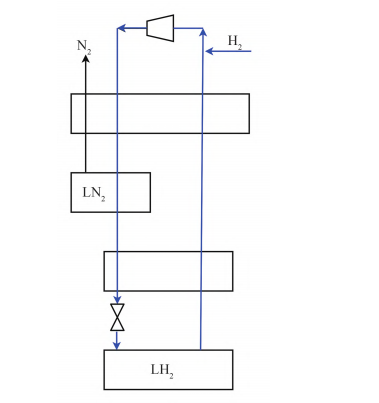
图1 预冷型Linde-Hampson循环示意图
1.2 预冷型Claude循环
1902年,Georges Claude在Linde-Hampson循环的基础上进行了革命性的创新,引入了透平膨胀机,从而诞生了简单版的Claude循环。理论上,这一循环无需预先冷却即可直接将氢气液化,但在实际工业应用中,为了提升能源利用效率,普遍采用了预冷型的Claude循环。该循环的核心机制如图2所示,其独特之处在于整个过程中仅使用氢气作为单一介质。
在预冷型Claude循环中,首先,经过预冷的氢气通过高效换热器,回收了来自已液化或低温状态的返流氢的冷量,实现了能量的初步利用。随后,部分氢气被送入透平膨胀机进行绝热等熵膨胀,这一过程中,氢气温度进一步降低,并释放出大量冷量,这些冷量被有效地传递给待液化的原料氢。最终,原料氢在充分吸收冷量后,通过节流过程转变为液态氢。而那些未能完全液化的氢气以及膨胀后的氢气则被重新导向压缩机,进行下一轮循环,同时,在这一过程中,它们所携带的剩余冷量也被回收利用。
预冷型Claude循环凭借其高效、稳定的性能,成为了当前大规模氢液化装置的基础架构。事实上,所有正在运行的大规模氢液化设施,都可以视为预冷型Claude循环的改良或衍生版本,这一技术的广泛应用,极大地推动了氢能产业的发展与普及。
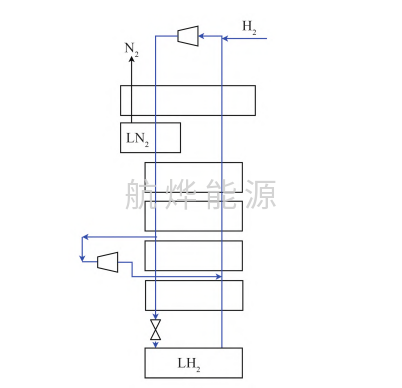
图2 预冷型Claude循环示意图
1.3 氦气逆Brayton循环
氦气逆Brayton循环是在Claude循环技术框架内的一次创新尝试,它巧妙地采用了氦气作为制冷媒介。鉴于氦气的液化点远低于氢气,经过预冷处理的氦气在透平膨胀机的作用下,能够降至比液氢温度更低的水平。这一特性使得原料氢在经历预冷及一系列换热器冷却后,无需再通过传统的节流过程,即可直接实现液化,其运作机制如图3清晰展示。
在能耗表现上,氦气逆Brayton循环位于预冷型Claude循环与预冷型Linde-Hampson循环之间,展现出了适中的能源效率。更为重要的是,采用氦气作为制冷介质有效规避了处理高压氢气时可能遇到的安全风险,同时,氦气透平膨胀机的技术挑战相较于氢透平膨胀机而言更为可控。因此,在实际应用中,氦气逆Brayton循环通常被选作日产量在5吨以下的中型氢液化装置的首选方案。
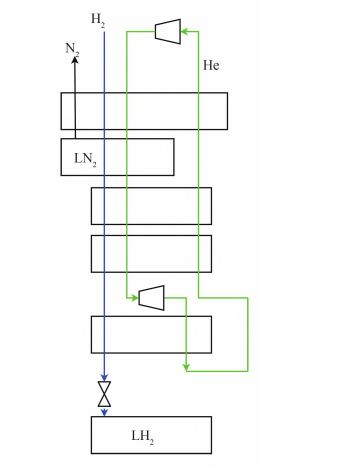
图3 预冷型Brayton循环示意图
2 混合冷剂预冷氢液化循环研究进展
当前,混合冷剂技术在氢液化循环领域仍处于探索与发展阶段,根据混合冷剂的制冷效能区间,该技术路径可细分为混合冷剂预冷循环与混合冷剂深冷循环两种策略。在混合冷剂预冷循环中,混合冷剂首先被用于将原料氢气预冷至接近液氮的温度范围,随后,当温度需进一步降至液氢水平时,则转而依赖成熟的Claude循环或逆Brayton循环来实现深度制冷。而在混合冷剂深冷循环中,从液氮温度到液氢温度的整个降温过程均通过混合冷剂来完成。
2.1 混合冷剂预冷氢液化循环
鉴于混合冷剂在液化天然气(LNG)领域的广泛应用与成熟技术,早期的研究自然而然地借鉴了这一经验,采用混合冷剂对原料氢进行初步预冷,预冷温度普遍设定在液氮温度附近。表1详细列举了采用混合冷剂预冷技术的氢液化工艺案例,展示了其液氢产量、预冷温度、能耗及㶲效率等关键指标。普遍而言,此类工艺的能耗维持在约7kW⋅h/kg的水平,而㶲效率则超过35%,这显著优于当前运行中的大型氢液化装置,彰显了其高效能特点。
值得注意的是,尽管各工艺案例的预冷温度均趋近于液氮温度区间,但具体数值却各有差异,这主要是由于研究中采用的混合冷剂组分不尽相同。常见的混合冷剂成分包括C1至C5烃类、氮气、氖气、氢气以及氦气,部分特例还引入了R14作为制冷剂。这些制冷剂的制冷温度范围从高到低依次为C5至C1烃类、氮气、氖气、氢气及甲烷。特别地,在混合冷剂预冷循环中,氖气的加入能够显著将制冷温度降低至80K以下。然而,对于制冷温度要求更低的氢气和氦气,它们通常不被纳入预冷循环中的混合冷剂组分考虑范围。
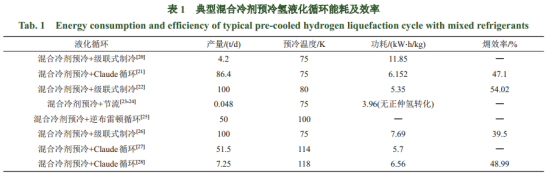
混合冷剂预冷的液化工艺中深冷循环一般采用Claude循环和级联式制冷循环,级联式制冷循环理论能耗更低,但是由于其设备复杂,需要更多的运动设备,因此投资大、维护费用高,目前工业上很少采用这种制冷方式。
2.2 混合冷剂深冷氢液化循环
表2列出了典型的混合冷剂深冷氢液化循环工艺的产量、能耗以及㶲效率。
随着科研探索的日益深化,众多学者正积极尝试在液氮至液氢的广泛温度区间内,运用混合冷剂来实现制冷效果,并已取得显著成效。相较于预冷氢液化工艺,混合冷剂深冷氢液化工艺在能耗方面展现出明显优势。这一优势主要得益于在液氮以下温度区间采用混合冷剂,使得深冷换热器中的冷热流体温度梯度更为接近,从而有效减少了深冷区域内的㶲损失。
值得注意的是,深冷温区所采用的混合冷剂组分与预冷阶段存在显著差异。具体而言,C2至C5等较重的烃类组分在此阶段不再适用,取而代之的是以甲烷、氮气、氖气、氢气及氦气为主要成分的混合制冷剂。此外,不同研究文献中对于深冷循环的具体设计也呈现出多样性,循环的数量并不统一,这反映了该领域在技术创新与方案优化上的活跃与多样性。
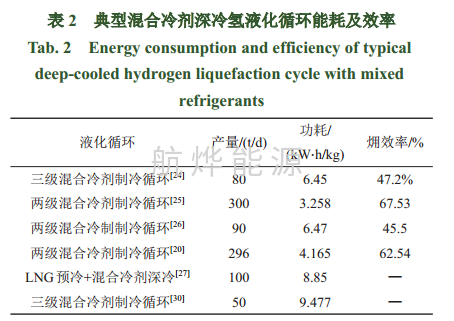
总结前述研究内容,我们可归纳出混合冷剂氢液化技术的几大鲜明特点:
1)相较于传统的氢液化工艺,混合冷剂氢液化循环通过大幅缩小换热器中的温度差异,实现了能耗的显著降低与㶲效率的显著提升,尤其在混合冷剂深冷氢液化工艺中,这一优势更为显著。
2)在混合冷剂预冷液化循环中,冷剂组分常包含C1至C3烃类、氮气、氖气等相对较重的成分;而进入深冷循环阶段,则转变为以氮气、氖气、氢气、氦气等低沸点轻组分为主的混合制冷剂。
3)混合冷剂各组分的配比优化对于降低氢液化过程中的能耗至关重要,然而,由于该问题的高度复杂性和非线性特征,目前尚未形成普遍适用的优化规律。多数研究者采用遗传算法等先进工具,以寻求冷剂组分的最佳配比。
4)当前,混合冷剂氢液化技术仍处于理论研究与概念验证阶段,全球范围内尚未有实际投产的混合冷剂氢液化装置,其技术可行性与经济性仍需进一步验证。
5)为追求更高的效率,一些研究者在设计氢液化流程时,引入了如两相透平膨胀机等尚未成熟的技术,这既体现了技术创新的勇气,也伴随着一定的风险与挑战。
6)混合冷剂组分对于制冷温度范围及效率具有决定性作用,但在氢液化领域,特别是液氮至液氢温区内的混合冷剂组分优化设计研究尚显不足。
结论:
1)鉴于我国氢能产业的蓬勃发展,液氢作为解决氢能储运难题的关键手段,其需求预计将迎来爆发式增长。因此,降低氢液化过程中的能耗已成为当前亟待解决的重要课题。
2)混合冷剂技术以其卓越的节能效果和能量利用效率,在氢液化领域展现出巨大的潜力。然而,目前该技术仍处于研发阶段,其实用性与经济性的验证尚需时日。
3)借鉴液化天然气技术的成功路径,我们可以合理推测,混合冷剂预冷氢液化工艺有望凭借其较低的技术门槛和突破地域限制的液氮预冷优势,率先在氢液化领域实现应用。而混合冷剂深冷氢液化工艺则可能需要更长时间的概念探索与技术研究。
在能源转型与绿色发展的浪潮中,航烨能源公司以其前瞻性的战略视野、创新的技术实力以及深厚的行业积淀,持续引领着能源行业的绿色变革。我们致力于成为清洁能源解决方案的卓越提供者,通过不断优化能源结构,提升能源利用效率,为全球可持续发展贡献航烨力量。展望未来,航烨能源将继续秉承“科技驱动绿色未来”的核心理念,携手各界伙伴,共同开创一个更加清洁、高效、可持续的能源新时代。