面对国内天然气供应的紧张局势,焦炉煤气制LNG(液化天然气)并联产氢气的项目应运而生,该项目不仅能够有效缓解能源短缺问题,还极大地推动了焦化产业与能源领域的科技进步与产业升级,实现了经济、环境与社会效益的和谐共生。本文探讨了焦炉气综合利用的最佳途径,并对深冷和提氢先后的不同工艺方案进行了技术经济比较.
面对国内天然气供应的紧张局势,焦炉煤气制LNG(液化天然气)并联产氢气的项目应运而生,该项目不仅能够有效缓解能源短缺问题,还极大地推动了焦化产业与能源领域的科技进步与产业升级,实现了经济、环境与社会效益的和谐共生。
焦炉煤气作为一种成分复杂的副产物,其富含的资源价值往往被低估。除了微量的焦油、苯、萘及硫化物等杂质外,其主要成分包括占总体积分数25%至30%的甲烷(CH4)和氢气(H2),后者更是高达55%至60%,此外还有约10%的一氧化碳(CO)、二氧化碳(CO2)以及少量的氮气(N2)和氧气(O2)。在当前甲醇、合成氨等产能相对过剩的背景下,从焦炉煤气中提取市场紧需的LNG和氢气,不仅符合国家节能减排的战略导向,还为企业开辟了新的盈利增长点,是实现资源高效利用的最佳实践。
表1 焦炉煤气成分表
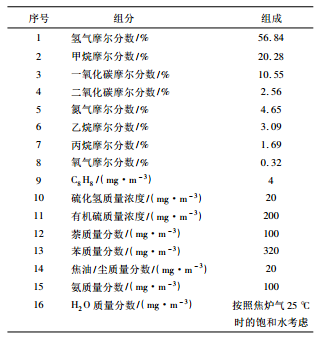
为了确保LNG生产的顺利进行,焦炉煤气需经过严格的净化处理,以去除其中的酸性气体、水分及其他杂质。这些杂质在低温下易形成结晶或结冰,不仅可能堵塞管道,还可能对设备造成腐蚀。因此,净化步骤至关重要。
随后,原料气需进行增压处理,以优化液化过程。提高原料气的压力能够在降低液化温度的同时减少制冷功率的消耗,从而节省能源。然而,过高的压力也会增加设备投资和维护成本,因此,通常将原料气压力控制在约5.5MPa(表压)左右,以达到经济效益与技术可行性的最佳平衡。
液化工艺的创新与选择
在液化工艺上,本项目采用了先进的混合制冷剂制冷循环技术,以N2和C1至C5烃类混合物作为循环制冷剂。该技术通过一台压缩机实现制冷循环,简化了流程并降低了造价。进一步地,结合丙烷预冷的MRC(混合冷剂循环)工艺(简称C3/MRC工艺),实现了冷量的高效利用。该工艺分为高温段和低温段两个阶段,高温段利用丙烷压缩制冷将原料气预冷至约-40℃;低温段则通过高压和低压混合冷剂与原料气进行换热,进一步降低其温度至液化点以下。这种分段供冷的方式充分利用了热力学原理,极大地提高了液化效率。
在将焦炉煤气转化为LNG(液化天然气)并同时生产氢气的过程中,存在两种主要的工艺路线选择,它们各自具有不同的特点和优势。
先提氢后深冷
此路线首先对净化后的焦炉煤气进行PSA(变压吸附)提氢处理,目的是从原料气中高效提取氢气。然而,PSA提氢过程中产生的解析气(主要为甲烷)处于常压状态,无法直接满足后续冷箱液化对压力的要求。因此,需要增设一台提氢解析气压缩机,将解析气的压力提升至冷箱所需的水平。随后,经过压缩的甲烷气进入冷箱进行液化分离,最终制成LNG。这种路线的优势在于能够先期分离出高纯度的氢气,但缺点是增加了压缩机的投资和运行成本。
先深冷后提氢
与第一种路线不同,此路线将净化后的焦炉煤气直接送入冷箱进行液化处理。在冷箱内,原料气经过降温和压力变化,实现各组分之间的初步分离,产生高压富氢气和低压富CO气体。随后,这些气体被分别送往PSA提氢装置进行进一步的提纯。值得注意的是,此路线省去了对解析气的二次增压过程,因为原料气在进入冷箱时即已具备足够的压力。然而,由于焦炉煤气中氢气含量较高,导致液化分离的难度增加,需要更低的温度才能实现有效分离,从而增加了能量的消耗。此外,为了应对更高的液化压力和更低的分离温度,冷箱的规模也需相应扩大。

图1 先提氢再深冷
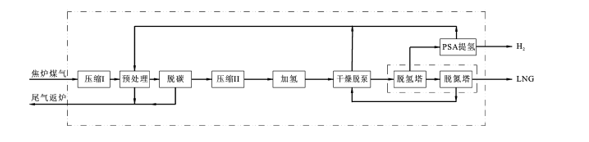
图2 先深冷再提氢
焦炉煤气制LNG并联产氢气的项目不仅是一项技术创新的成果,更是推动能源结构优化和环境保护的重要力量。航烨能源专注于LNG领域和制冷循环装置的深度研发、创新设计、高效生产及全方位安装服务。我们致力于为客户提供量身定制的LNG冷能系统解决方案,全方位满足您的需求,欢迎来电咨询。