然而,随着化工装置规模的扩大以及化工工艺向高温高压方向发展,传统的管壳式换热器在高温高压环境下更为常见,而铝制板翅式换热器则较为少见。原因在于,尽管铝材在常温或低温条件下表现出色,但随着温度攀升,其许用应力逐渐降低,特别是在超过100℃后,许用应力大幅下降,至200℃时接近材料的应力极限,此时多数铝材的许用应力仅为常温下的不足一半(具体数据参见表1)。这一特性限制了板翅式换热器在高温高压下的承压能力。
尽管在高温高压条件下,管壳式换热器展现出明显的优势,但大型化后的化工装置中,由于其单位体积换热面积有限,导致设计的换热器体积庞大、占地面积广、制造复杂且成本高昂。相比之下,板翅式换热器以其紧凑的结构和高效的换热性能,在相同负荷下体积更小、成本更低,具有诸多管壳式换热器无法比拟的优势。因此,通过合理的结构设计和材料选择,板翅式换热器同样适用于高温高压工况。以国内某乙烯项目的甲烷冷却器为例,我们可以深入探讨高温高压板翅式换热器的设计思路与实现方法。
表1 各主要铝材在不同温度下的许用应力
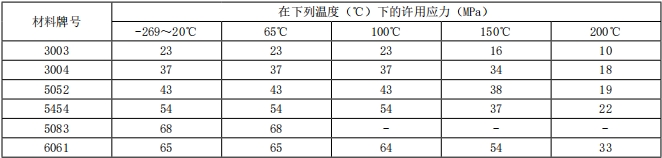
1 换热器设计参数
热流体方面,我们采用甲烷作为介质,其设计压力设定为4.95MPa。在正常工作条件下,甲烷的进口温度为40℃,经过换热后,出口温度降至16℃。然而,考虑到在实际运行过程中,甲烷的进口温度可能会瞬间飙升至一百多摄氏度,为了确保换热器的安全运行,我们将热流体的设计温度保守地设定为150℃。
冷流体方面,我们选用三元冷剂作为介质,其设计压力为2.6MPa。在换热过程中,冷剂的进口温度为10℃,经过与热流体的热交换后,出口温度升高至21.5℃。由于我们已经将热流体的设计温度提高到了150℃,因此在极端情况下,换热器热端的冷流体温度将保持在21.5℃,而热流体温度则可能达到150℃。这样的设计既考虑了正常工况下的换热需求,又兼顾了可能出现的极端情况,确保了换热器的可靠性和安全性。同时,热流体和冷流体的传热系数分别设定为2400 W/m²•K和1900 W/m²•K,且换热器采用逆流换热形式,以进一步提高换热效率。
2 材料选用
板翅式换热器主要由两部分构成:一是用于流体汇集的封头,二是负责热量传递的核心部件——芯体。芯体则进一步细分为翅片、隔板、封条以及侧板这四个关键组件。在设计高温高压型的板翅式换热器时,对各主要承受压力的元件材料进行科学选择至关重要。
在封头材料的选择上,我们遵循的是材料的经济性和加工的便捷性。对于高压铝制板翅式换热器,若其设计温度不超过65℃,通常会选用铝镁合金5083作为封头材料,因其具有较高的许用应力,有助于减少封头的厚度。然而,在甲烷冷却器的设计中,由于热侧的设计温度高达150℃,5083材料便不再适用,而需改用能承受高温的铝材,如5052、5454或6061等,这会导致封头厚度的相应增加。对于冷侧,考虑到最极端的工况即热侧进口温度为150℃,但冷侧流体是在进入芯体后才进行换热,其进口温度仅为10℃,因此冷侧进口封头仍可选用5083材料。至于冷侧出口,由于流体在芯体内经过热交换后,其温度是两股流体相互作用的结果,且经过热平衡计算,出口温度并未达到65℃,故出口封头同样可选用5083,以达到减薄封头厚度的目的。
在翅片材料的选择上,我们主要依据的是翅片的抗拉强度。当设计压力小于6.9MPaG时,翅片材料通常会选用3003,因为其强度足以满足这一压力范围。但当设计压力超过这一值时,为了增强换热器的承压能力,就需选用抗拉强度更高的3004材料。在甲烷冷却器的设计中,考虑到极端情况下芯体金属材料的最高温度约为93.22℃,根据相关数据表,大部分材料在此温度下的许用应力并未降低,因此翅片材料仍可选用3003。
3 结构设计
为了满足高温高压板翅式换热器的独特设计要求,合理的结构设计至关重要,而在这一过程中,材料的选择只是其中一环。
翅片作为板翅式换热器的核心部件,不仅承担着传热的功能,还需具备一定的承压能力。对于高温高压的工作环境,选用高压翅片成为了增强换热器承压能力的关键。评估翅片承压性能的一个重要指标便是其爆破试验压力。在翅片参数保持一致的情况下,平直型翅片展现出了最强的承压能力,多孔型翅片紧随其后,而波纹型和锯齿型翅片的承压能力则相对较弱。然而,从阻力降和传热效率的角度来看,这几种翅片的性能则呈现出相反的趋势。
在设计本换热器时,我们综合考虑了翅片的承压能力与加工限制。为了提升翅片的承压能力,我们倾向于增加翅片的厚度并减小节距。但这一做法也面临着加工上的挑战:翅片越厚,冲床模具的回弹量就越大,从而影响了翅片的成型质量;而节距越小,冲床模具就越容易受损,导致无法顺利冲制翅片。因此,在权衡了各方面因素后,我们最终选择了翅高为6.35毫米、翅厚为0.5毫米、节距为1.7毫米的高压翅片。
面对150℃时铝合金材料许用应力的显著下降,甲烷冷却器封头的计算厚度大幅增加,尤其是在考虑了开孔补强后,封头的名义厚度更是达到了35毫米,这无疑给封头的加工与焊接工艺带来了巨大挑战。铝合金的延伸率相对较低,室温下若形变量超过10%,便极有可能产生裂纹。因此,在加工前,必须对其进行加热以提高塑性,加工完成后还需进行退火处理,以有效消除残余应力。
在封头的实际加工与安装过程中,我们采取了多项措施以确保质量。首先,考虑到封头与换热器芯体之间的角焊缝为单面焊,为保证焊透,我们特别选用了40毫米宽度的封条来配合热侧较厚的封头。其次,我们采用了过渡短节的设计,先将其与芯体进行双面焊接,待封头加工完成后再与短节进行对接焊复合,这一方法大大提高了焊接的可靠性和效率。
此外,在换热器的通道排列上,我们也进行了精心的设计。由于板翅式换热器最外侧通道的承压能力相对较弱,因此,在排列时,我们将高压的热侧通道放置在中间位置,而低压的冷侧通道则排在最外侧。同时,为了进一步增强冷侧通道的承压能力,我们在其外侧特别布置了四层工艺层。这样的设计不仅提高了换热器的整体承压性能,还确保了其在高温高压环境下的稳定运行。
4 总结
高温高压板翅式换热器的设计独具特色,它证明了在铝材使用温度范围内,即便面对高温高压的严苛工况,通过巧妙的结构设计与恰当的材料选择,这种换热器完全能够替代传统的管壳式换热器。这一替代不仅显著减小了设备的体积,还完美契合了装置大型化对工艺流程的高要求。
航烨能源通过创新的结构设计和材料选用,提高了换热器的承压能力和传热效率,有效缩小了设备体积,满足了装置大型化的工艺流程要求,推动了该领域的技术进步和应用拓展。