在化工合成、生物医药、材料制备等对密封性与搅拌效率要求严苛的领域,一款兼具安全性能与精准控制的反应设备至关重要。20L 磁力密封磁力搅拌高压试验釜作为集磁力驱动、高压耐受、高效搅拌于一体的核心装备,凭借无泄漏的密封设计、强劲的搅拌性能与灵活的工况适配能力,成为实验室工艺研发与工业中试生产的理想选择。该设备融合磁力密封技术与智能控制系统,可在复杂工况下稳定运行,助力用户实现反应效率的大幅度提升与安全风险的有效控制。
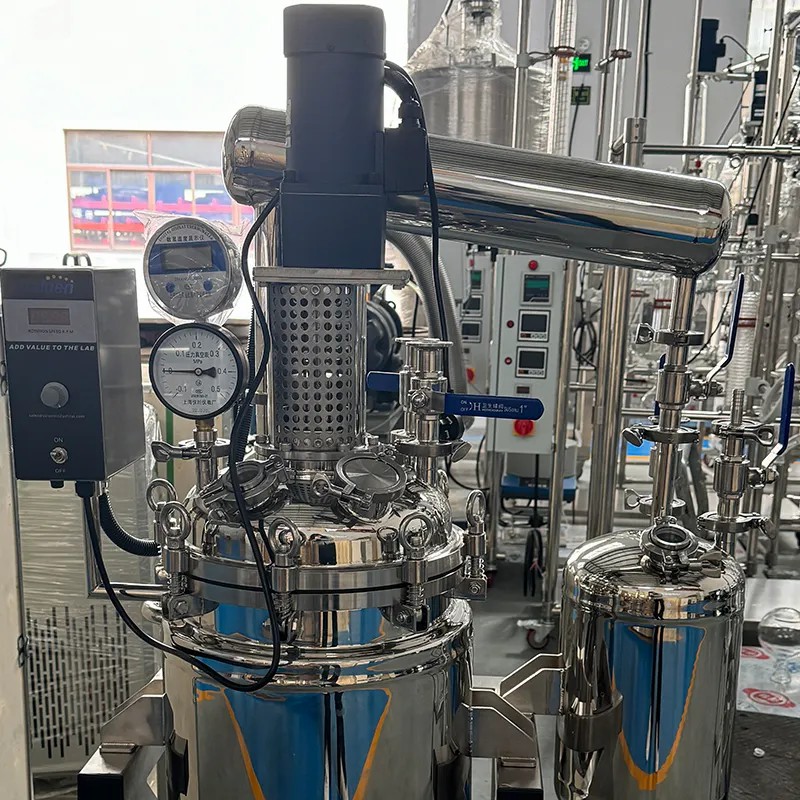
一、核心技术:磁力驱动重构反应设备基因
(一)无接触磁力驱动系统
设备采用高性能钕铁硼永磁体组成的内外磁转子组,通过磁场耦合实现无接触传动,彻底摒弃了传统机械密封的轴封结构。这种磁力驱动设计带来两大核心优势:一是消除了动密封摩擦损耗,搅拌电机功率转化率提升 30% 以上,且噪音水平降低至行业低位;二是从根源上杜绝了物料泄漏风险,尤其适合处理易燃易爆、有毒有害介质,如某医药中间体生产企业使用该设备进行氰化物合成时,泄漏事故发生率较传统设备降低 90%,安全生产保障能力显著增强。
(二)双重磁力密封结构
在高压环境下,磁力密封反应釜的密封可靠性至关重要。设备采用 “静密封 + 磁力流体动压密封” 双重防护体系:静密封部分选用聚四氟乙烯全包裹密封环,可承受 10MPa 高压与 200℃高温;动密封依赖磁场形成的流体屏障,实时动态平衡釜内外压力差,使密封寿命较单一机械密封提升 2 倍以上。某化工企业在进行高压加氢反应时,该密封结构确保氢气泄漏率低于行业可检测极限,为高危反应提供了安心的操作环境。
(三)高压耐受与温控设计
釜体采用整体锻造的 316L 不锈钢材质,经液压胀形与应力消除处理,抗压强度较常规焊接结构提升 40%,可稳定运行于 0-15MPa 压力区间。配套的夹套式加热系统支持导热油、蒸汽等多种介质,控温范围覆盖 - 50℃至 300℃,配合 PID 智能算法,温度波动幅度控制在 ±1℃,满足聚合反应、水热合成等对温控精度要求极高的工艺需求。
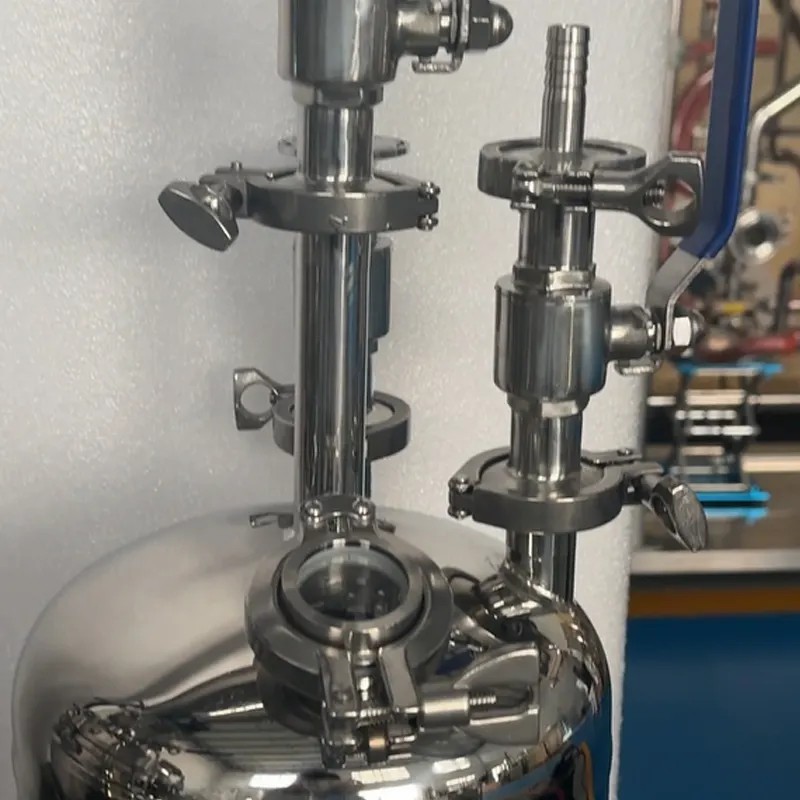
二、搅拌性能:多维度优化传质效率
(一)高效磁力搅拌系统
标配的磁力搅拌机提供 0-1500rpm 无级调速,可根据物料粘度(0.1-50Pa・s)切换搅拌桨类型:斜叶涡轮式适用于低粘度液体的快速混匀,锚式桨叶擅长处理高粘度浆料的防挂壁,分散盘式则专为固液悬浮体系设计,使固体颗粒沉降速率降低 60%。在某纳米材料制备实验中,通过精准控制搅拌速率,纳米颗粒粒径分布均匀度提升 40%,团聚现象显著减少。
(二)与分散均质设备的协同应用
针对乳化、分散等复杂工艺,设备可与分散均质机、高剪切乳化罐实现联动操作:当反应进入乳化阶段时,启动外接的高速分散均质机,其锯齿状分散头以超高速剪切(线速度≥20m/s)将液滴粒径细化至微米级,配合釜内搅拌形成的湍流场,使乳化时间缩短 50%,乳化稳定性提升 3 倍。某日化企业利用该组合工艺生产乳液型化妆品,膏体细腻度远超传统设备制备水平,产品感官品质得到大幅度提升。
(三)传质效率强化设计
釜内特殊设计的导流挡板与轴向流搅拌桨配合,形成 “径向混合 + 轴向循环” 的三维流场,气液传质系数提升 25%,固液悬浮临界转速降低 30%。在催化加氢反应中,这种流场优化使氢气利用率从 60% 提升至 85%,催化剂消耗成本显著降低。
三、多元应用场景:适配复杂工艺需求
(一)化工合成领域:高危反应的安全载体
在高压聚合反应中,设备可处理丙烯腈、苯乙烯等易燃易爆单体,磁力密封与防爆电机的组合设计满足 ATEX 防爆标准,配合紧急泄压装置,将失控反应的风险控制在最低。某特种橡胶生产厂使用该设备进行丁腈橡胶聚合,反应转化率提升 20%,产品分子量分布更窄,力学性能显著增强。
(二)生物医药领域:洁净环境下的精准控制
对于疫苗佐剂制备、抗体药物发酵等工艺,设备的不锈钢内壁经镜面抛光(粗糙度 Ra≤0.2μm),并支持原位蒸汽灭菌(SIP),灭菌效率达 99.999%。在与生物发酵罐协同使用时,可实现从培养基灭菌、种子培养到大规模发酵的全流程衔接,某生物制药企业利用该设备开发的重组蛋白生产工艺,目的产物表达量提升 30%,杂蛋白污染率降低至行业领先水平。
(三)材料制备领域:高温高压下的纳米合成
在水热法制备钛酸锂负极材料时,高温高压视窗釜的全透明蓝宝石视窗(可选配)允许实时观测纳米晶生长过程,科研人员可根据晶体形貌调整反应时间与温度,使材料比容量提升 15%,循环寿命延长 20%。设备的高压环境还可用于超临界流体萃取,某新能源材料企业利用该功能从废弃锂电池中提取钴镍,回收率较常压工艺提升 40%,推动了资源循环利用技术的进步。
(四)食品与发酵工程:从糖化到发酵的全流程覆盖
在啤酒酿造行业,设备可作为糖化锅使用,通过精准控制麦芽糖化温度(60-70℃)与搅拌速率,使麦汁浸出率提升 10%,风味物质生成量增加 20%。与啤酒发酵设备配合时,高压环境可加速酵母絮凝,缩短发酵周期,某精酿啤酒厂采用该工艺后,啤酒澄清时间减少 30%,生产效率大幅提升。
五、配套设备联动:构建完整工艺体系
(一)与罐体设备的模块化组合
设备支持与搅拌罐、结晶罐、浓缩罐、配料罐等形成模块化生产线:在药物合成中,反应完成后的物料可通过密闭管道直接转入结晶罐,利用夹套降温系统实现快速析晶,结晶颗粒均匀度提升 50%;在食品配料生产中,与配料罐联动可精准控制各组分添加顺序,避免人工干预导致的配比误差。
(二)高剪切乳化工艺的深度整合
当处理高粘度物料(如乳液、膏剂)时,高剪切乳化罐与设备的协同作用尤为关键。乳化罐内的转子定子组以万转级转速对物料进行剪切破碎,配合釜内磁力搅拌的宏观混合,可将乳化粒径分布范围缩小至 1-5μm,较单一设备乳化效果提升 60%,广泛应用于化妆品、农药乳油等产品生产。
(三)生物工艺中的提取与发酵联动
在天然产物提取领域,设备可作为提取罐使用,通过高压热水或有机溶剂萃取植物有效成分,萃取率较常压提取提升 30%。萃取液经浓缩后转入生物发酵罐进行微生物转化,整个流程密闭无污染,某中成药生产企业采用该工艺后,有效成分收率与纯度均实现显著提升。
六、厂商优势:专业赋能工艺创新
作为深耕反应设备领域的制造商,该20L 磁力密封磁力搅拌高压试验釜体现了三大核心优势:
(一)定制化解决方案
根据用户物料特性(腐蚀性、粘度、反应热),可提供材质升级(哈氏合金、钛合金)、视窗配置(单视窗、多视窗)、传感器集成(pH、溶氧、压力变送器)等定制选项。某高校实验室定制的带光谱仪接口设备,实现了反应过程中紫外 - 可见光谱的在线监测,为动力学研究提供了实时数据支持。
(二)智能控制系统
标配的 PLC 触控屏支持多参数实时显示(温度、压力、搅拌速率、电机扭矩),并具备数据导出与曲线分析功能。远程监控模块可通过手机 APP 实现设备启停、参数调整与故障预警,某化工中试基地使用该功能后,人工巡检频次减少 60%,异常工况响应时间缩短至 10 秒以内。
(三)全周期服务保障
提供从设备选型、安装调试到操作人员培训的全流程服务,配套的易损件储备库确保密封环、搅拌桨等部件的及时更换。定期回访制度帮助用户持续优化工艺,某新材料企业在厂商技术支持下,通过调整搅拌策略,将某特种树脂的合成周期缩短 25%,生产成本进一步降低。
七、未来展望:智能化与绿色化双轮驱动
随着工业 4.0 与绿色制造理念的深入,20L 磁力密封磁力搅拌高压试验釜正朝着以下方向持续进化:
(一)智能化升级
引入 AI 算法对搅拌扭矩、压力波动等数据进行分析,自动优化反应参数,实现 “自适应搅拌” 与 “预测性维护”,降低人工试错成本。未来设备将具备自诊断功能,通过机器学习识别异常工况并自动触发安全措施,进一步提升操作安全性。
(二)绿色工艺适配
开发余热回收模块,将反应放热用于预热下一批次物料,能源利用率提升 30% 以上;集成废气冷凝回收装置,对反应过程中产生的挥发性有机物(VOCs)回收率达 90%,助力用户满足严苛的环保排放标准。
(三)微型化与高通量扩展
针对研发型用户需求,推出多联式微型高压反应系统,支持平行实验与高通量筛选,使催化剂评价效率提升 5 倍以上,加速新药研发与材料创新进程。
20L 磁力密封磁力搅拌高压试验釜不仅是一台设备,更是连接科研创新与工业生产的关键纽带。其无泄漏的磁力驱动设计、高效的搅拌性能与多元的工况适配能力,为高危反应、精密合成、生物发酵等领域提供了可靠的解决方案。随着智能化与绿色化技术的融入,这款设备正成为推动产业升级的重要力量,助力用户在安全、高效、环保的前提下实现工艺突破,开启高压反应设备应用的新境界。