换热器的分类与核心工作原理
换热器的本质是实现两种或多种流体间热量传递的设备,其分类方式多样,按传热原理可分为间壁式、混合式与蓄热式三大类,每类设备因结构特性不同而适用于特定工业场景。
间壁式换热器是工业领域应用最广泛的类型,其核心特征是通过固体壁面将参与换热的两种流体分隔,热量通过壁面实现间接传递,有效避免流体混合污染。常见的间壁式换热器包括壳管式、板式、翅片管式等。以壳管式换热器为例,其由壳体、管束、管板、封头、折流板等部件构成,一种流体在管内流动(管程),另一种在壳体内管束外部流动(壳程),通过管壁完成热量交换。这种结构因其耐高压、适应宽温域的特性,被广泛应用于石油化工、电力等行业的大型装置中。而板式换热器则由一系列波纹金属板叠加而成,板片间形成狭窄流道,流体在板间逆向流动,利用波纹结构强化湍流,显著提升换热效率,在食品加工、制冷空调等对换热效率要求高且压力较低的场景中表现优异。
混合式换热器通过直接接触实现热量传递,适用于允许两种流体混合的工况,如冷却塔、喷射式换热器等。冷却塔中,高温冷却水与空气直接接触,通过蒸发与对流将热量散发至大气,广泛应用于电力、化工等行业的循环水系统。蓄热式换热器(又称回热器)则利用固体物质的蓄热与放热特性实现热量传递,两种流体交替流过蓄热体,当热流体流过时,蓄热体吸收热量;冷流体流过时,蓄热体释放热量。这类设备在冶金、陶瓷等行业的余热回收中发挥重要作用,如炼钢转炉的余热回收装置。
无论哪种类型,换热器的核心工作原理均基于热传递的三种基本方式:热传导、热对流与热辐射。在间壁式换热器中,热量传递过程可分解为三个环节:热流体通过对流将热量传递至壁面(对流换热)、热量通过固体壁面从高温侧传导至低温侧(热传导)、壁面通过对流将热量传递至冷流体(对流换热)。其换热效果取决于总传热系数 K,计算公式为 1/K = 1/h₁ + δ/λ + 1/h₂(其中 h₁、h₂分别为两侧流体的对流换热系数,δ 为壁面厚度,λ 为壁面材料导热系数)。因此,提升换热器性能的关键在于优化这三个环节,而模拟仿真技术正是实现这一目标的精准工具。
传统设计方法的瓶颈与挑战
在模拟仿真技术普及之前,换热器的设计与优化长期受制于经验主导与实验依赖的双重局限,难以满足现代工业对高效、节能、定制化的需求。这种传统模式的瓶颈主要体现在以下三个方面:
经验设计的局限性
早期换热器设计多依赖工程师的经验积累与简化的经验公式,如管壳式换热器的壳程传热系数计算常采用 Kern 方法或 Bell-Delaware 方法。这些方法基于特定工况下的实验数据拟合而成,虽能满足基本设计需求,但在复杂工况下误差较大。例如,当流体为高黏度介质或存在相变时,经验公式的适用性大幅下降,可能导致设计出的换热器换热效率偏低或结构冗余。某化工企业曾采用经验公式设计某反应釜的夹套换热器,因未考虑物料黏稠度随温度的非线性变化,实际运行中换热效率仅达到设计值的 75%,不仅增加了能耗,还因反应温度波动影响了产品质量稳定性。
经验设计的另一短板是难以应对创新结构需求。随着工业对换热器紧凑化、轻量化的追求,新型结构(如螺旋板式、板翅式)不断涌现,而这些结构的流动与传热特性复杂,缺乏成熟的经验公式支撑。工程师往往只能在传统结构基础上做局部修改,限制了创新设计的突破。
实验测试的高成本与低效率
实验测试是验证设计方案与优化参数的传统手段,但在换热器领域,其成本与周期问题尤为突出。搭建一套换热器实验装置需投入大量资金,包括设备加工、测量仪器(如热电偶、流量计、压力传感器)、控制系统等。对于大型工业换热器,仅制作缩尺模型的成本就可能高达数十万元。某电力企业为优化 300MW 机组的凝汽器结构,制作了 1:5 缩尺模型进行实验,仅模型加工与测试系统搭建就耗时 3 个月,花费近 80 万元。
实验测试的周期长且工况覆盖有限。由于换热器性能受流体种类、流量、温度、压力等多参数影响,全面测试所有工况几乎不可能。工程师通常只能选取关键工况进行测试,通过插值法推测其他工况的性能,这不可避免地带来误差。此外,实验过程中若发现设计缺陷,需重新加工模型并再次测试,进一步延长研发周期。某汽车空调企业开发新型微通道换热器时,因实验中发现制冷剂分配不均问题,反复修改结构并测试,导致研发周期从原计划的 6 个月延长至 10 个月,错失了市场窗口期。
多目标优化的矛盾与妥协
现代工业对换热器的要求日益多元化,需同时满足换热效率高、压降小、体积紧凑、成本低等目标,而这些目标之间往往存在矛盾。例如,增加换热面积可提升效率,但会导致体积增大与成本上升;提高流速能增强对流换热,但会增加压降与能耗。传统设计方法难以精准量化这些目标的权衡关系,工程师只能凭经验做出妥协,难以找到全局最优解。某板式换热器生产企业在设计某食品冷却设备时,为降低压降而减小了板片波纹高度,虽满足了压降要求,但换热效率下降了 12%,最终不得不通过增加板片数量来弥补,导致成本超出预算 15%。
模拟仿真技术的深度应用与技术突破
模拟仿真技术通过构建虚拟模型再现换热器的流动与传热过程,为突破传统设计瓶颈提供了全新路径。从基础的一维计算到三维流场仿真,不同层级的仿真工具满足了从快速评估到精细优化的全流程需求,成为现代换热器设计的核心支撑。
一维与二维仿真:快速评估与参数优化
一维仿真以集中参数模型为核心,忽略空间分布细节,重点关注进出口参数与整体性能的关系,适用于方案初步筛选与参数敏感性分析。MATLAB 作为数值计算的强大工具,在一维仿真中应用广泛,其核心是基于传热学基本方程与换热器效能 - 传热单元数(ε-NTU)方法。
ε-NTU 方法通过计算换热器效能 ε(实际传热量与最大可能传热量的比值)与传热单元数 NTU(表征换热能力的无量纲参数),快速评估性能。在 MATLAB 中,工程师可编写程序实现不同流型(如顺流、逆流、交叉流)的 ε-NTU 计算,并结合迭代算法优化关键参数。例如,对于管壳式换热器,通过编写脚本可模拟管程数、壳程挡板间距、管径等参数对 ε 与压降的影响,在几分钟内完成上百组参数组合的计算,筛选出最优范围。某换热器设计公司利用 MATLAB 对某化工用管壳式换热器进行参数优化,通过遍历管径(15mm-30mm)、管长(2m-6m)的组合,在 2 小时内找到了效能提升 8% 且压降降低 5% 的参数组合,而传统方法需数天才能完成相同工作量。
二维仿真在一维基础上考虑某一方向的空间分布,适用于平板式、螺旋板式等具有对称结构的换热器。COMSOL Multiphysics 是二维仿真的常用工具,其多物理场耦合能力可同时模拟流体流动与传热。在板式换热器二维仿真中,工程师可建立板片通道的二维模型,设置流体属性与边界条件,求解 Navier-Stokes 方程与能量方程,得到通道内的速度分布与温度梯度。通过分析不同波纹角度(30°、45°、60°)对流动阻力与换热系数的影响,可精准优化板片结构。某企业采用 COMSOL 对板片波纹角度进行仿真优化,发现 45° 角时在相同流量下换热系数比 30° 角提高 18%,而压降仅增加 7%,据此改进的产品获得了显著的市场竞争力。
三维 CFD 仿真:揭示流场与温度场的微观奥秘
三维 CFD(计算流体动力学)仿真通过求解三维空间的流动与传热方程,能精准再现换热器内部的复杂流场与温度场,是深入分析与优化结构的核心工具。Fluent、ANSYS CFX 等软件凭借强大的物理模型与求解器,成为换热器三维仿真的主流选择,其应用流程主要包括以下步骤:
几何建模与网格划分是三维仿真的基础。工程师需根据设计图纸,利用 CAD 软件(如 SolidWorks、AutoCAD)构建换热器的精确几何模型,包括流道、翅片、挡板等细节。对于复杂结构(如板翅式换热器的翅片阵列),需简化非关键细节以平衡计算精度与效率。网格划分将几何模型离散为大量微小单元,是影响仿真精度的关键环节。在管壳式换热器仿真中,壳程流体绕管束流动的区域需采用结构化网格以提高精度,而封头、挡板等复杂区域可采用非结构化网格。某研究团队对一台 160 根管的管壳式换热器进行仿真时,通过局部加密管束周围网格(最小网格尺寸 0.5mm),成功捕捉到了流体绕流产生的涡流,而采用均匀网格时这些细节完全被忽略。
物理模型与边界条件设置决定了仿真的可靠性。根据换热器的工作特性,需选择合适的湍流模型(如 k-ε 模型适用于一般湍流,SST k-ω 模型适用于有分离流的场景)、传热模型(如强制对流、相变模型)。边界条件包括入口流量 / 压力、出口压力、壁面温度 / 热流密度等。在模拟冷凝器中的相变传热时,需启用 Fluent 的多相流模型(如 VOF 模型)与相变模型,设置制冷剂的饱和温度与相变潜热。某空调企业仿真微通道冷凝器时,通过精准设置制冷剂 R32 的相变参数,成功模拟了从过热蒸汽到饱和液体的相变过程,仿真得到的换热量与实验数据偏差仅为 3.2%。
结果分析与结构优化是三维仿真的核心价值所在。通过速度矢量图、温度云图、压力分布图,工程师可直观发现设计缺陷。例如,某板式换热器仿真中,发现流道入口处因突然收缩产生局部高速区,导致压降过大,通过增加导流圆角,该区域流速峰值降低了 25%,压降减少 18%。在翅片管式换热器中,仿真发现翅片间距过小会导致流体绕流不畅,形成死区,通过优化间距从 1.5mm 调整为 2.0mm,死区面积减少 60%,换热效率提升 9%。
系统级仿真:多设备协同与动态特性分析
在工业系统中,换热器并非孤立运行,其性能受上下游设备影响,同时也影响整个系统的稳定性。系统级仿真通过构建包含换热器的整体系统模型,分析动态工况下的响应特性,为系统优化与控制策略制定提供支撑。Simulink 凭借其模块化建模优势,成为系统级仿真的首选工具。
在化工连续生产系统中,换热器的动态响应直接影响反应稳定性。某化工企业利用 Simulink 搭建了包含反应器、换热器、泵、控制系统的整体模型,其中换热器模块细化为壳程与管程的动态传热方程,与反应器的物料平衡、能量平衡方程耦合。通过仿真发现,当原料流量突然增加 10% 时,换热器出口温度会在 5 秒内下降 3℃,进而导致反应器温度波动。基于此,工程师设计了前馈 - 反馈复合控制系统,提前根据流量变化调整换热器热源供给,使温度波动控制在 ±0.5℃以内。
在新能源汽车热管理系统中,换热器(如水箱、冷凝器、蒸发器)与电池、电机、压缩机等设备协同工作,系统级仿真尤为重要。某车企利用 Simulink 建立了整车热管理模型,仿真不同工况(如快充、爬坡、高速行驶)下各换热器的负荷变化。结果显示,快充时电池产热骤增,传统换热器布局会导致冷却不足,据此优化了冷却液管路设计,增加了一个并联换热器,使电池温度在快充时控制在 45℃以下(原设计最高达 52℃)。
跨行业应用案例与效能提升数据
换热器模拟仿真技术的价值已在多个行业得到验证,从传统工业到高端制造,仿真驱动的设计优化带来了显著的能效提升、成本降低与周期缩短。
石油化工行业:高压换热器的安全与高效
石油化工行业的换热器多在高温、高压、腐蚀性环境下运行,对安全性与可靠性要求极高。某石化企业的加氢裂化装置中,一台管壳式换热器因壳程介质为高压氢气(压力 18MPa,温度 350℃),设计时需同时满足换热效率与抗氢脆要求。传统设计采用保守的壁厚与管间距,导致设备重量达 52 吨,制造成本高且换热面积利用率低。
通过 Fluent 三维仿真,工程师发现壳程流体在管束间分布不均,近入口区域流速过高(达 8m/s),不仅增加压降,还存在冲蚀风险;而远入口区域流速过低(仅 1.2m/s),换热效率低。基于仿真结果,优化了挡板结构,将原单弓形挡板改为双弓形,同时调整管束排列方式,使壳程流速分布均匀性提升 40%。仿真显示,优化后换热效率提高 12%,而压降降低 8%。更重要的是,通过仿真评估不同壁厚下的应力分布,在满足强度要求的前提下,将筒体壁厚从 50mm 减至 42mm,设备重量降至 45 吨,制造成本减少 15%(约 60 万元),且通过疲劳寿命仿真验证,设备使用寿命可达 15 年(原设计为 10 年)。
电力行业:电站锅炉换热器的节能改造
电站锅炉的省煤器、过热器、再热器等换热器是影响机组效率的关键设备。某 600MW 超临界机组的省煤器存在排烟温度偏高(设计值 120℃,实际达 135℃)的问题,导致锅炉效率降低约 1.2%,年多耗标煤约 5000 吨。
采用 ANSYS CFX 对省煤器进行仿真,发现主要原因是烟气侧飞灰沉积导致换热面污染,传热热阻增加。通过模拟不同飞灰浓度下的沉积过程,发现省煤器管束错列布置的间距不合理,导致局部烟气流速过低(<6m/s),飞灰易沉积。基于仿真结果,将管束横向间距从 80mm 增至 100mm,纵向间距从 60mm 增至 75mm,同时优化了吹灰器布置。改造后,排烟温度降至 122℃,锅炉效率提升 0.9%,年节约标煤约 3750 吨,投资回收期仅 8 个月。此外,通过仿真预测不同负荷下的烟气流场,制定了动态吹灰策略,使飞灰沉积速率降低 30%,延长了省煤器的检修周期。
航空航天领域:轻量化换热器的突破
航空航天设备对换热器的重量与体积要求极为严苛,每减轻 1kg 重量都能带来显著的效益。某卫星姿控系统的液冷换热器需在体积小于 0.01m³、重量小于 2kg 的约束下,实现 200W 的换热量,传统管壳式结构难以满足要求。
研发团队采用仿真驱动的创新设计:首先利用 SolidWorks 建立板翅式换热器的初始模型,通过 Fluent 仿真发现,传统平直翅片的换热面积有限,且流动阻力大。据此提出仿生结构翅片(模仿蜂巢结构),并通过参数化仿真优化翅片厚度(0.15mm)、间距(1mm)、角度(60°)。仿真显示,仿生翅片的换热系数比平直翅片提高 25%,而压降降低 18%。在此基础上,结合拓扑优化算法(通过 ANSYS Tosca 实现),删除翅片中受力较小的区域,进一步减轻重量。最终产品重量仅 1.8kg,换热量达 210W,比原设计方案减重 20%,且通过热循环仿真验证,在 - 50℃至 80℃的温度波动下可承受 1000 次循环而不失效。
食品医药行业:卫生级换热器的精准温控
食品医药行业的换热器需满足卫生要求(如易清洗、无死角),同时保证物料在换热过程中温度均匀,避免局部过热导致品质劣变。某果汁加工厂的板式换热器在运行中出现局部温度过高(超过 80℃),导致果汁维生素 C 损失率达 15%。
通过 COMSOL Multiphysics 仿真发现,板片密封垫片的局部凸起导致流道变窄,流速增加,湍流增强,此处的对流传热系数比其他区域高 30%,造成局部过热。更换新型截面的密封垫片后,流道分布均匀,温度偏差控制在 ±2℃以内,维生素 C 损失率降至 5% 以下。此外,针对换热器的 CIP(在线清洗)过程,通过 Fluent 仿真优化清洗液(85℃热水)的流速与路径,确保所有流道的雷诺数大于 3000(湍流状态),清洗时间从原有的 30 分钟缩短至 20 分钟,每年节约清洗成本约 12 万元。
仿真技术的发展趋势与未来挑战
换热器模拟仿真技术正朝着更精准、更高效、更智能的方向发展,同时也面临着多物理场耦合、尺度效应、数据验证等方面的挑战。
多物理场耦合仿真的深化
未来换热器的工作环境将更加复杂,需同时考虑传热、流动、相变、化学反应、结构力学、电磁效应等多物理场的耦合作用。例如,在质子交换膜燃料电池的换热器中,需模拟流体流动、传热、电化学反应、水管理(相变与传质)的耦合过程;在电磁加热换热器中,需耦合电磁场与热传导、对流的相互作用。目前,多物理场耦合仿真面临的主要挑战是不同物理场的时间尺度与空间尺度差异大(如化学反应的毫秒级与结构变形的小时级),求解效率低下。自适应时间步长算法与多尺度耦合方法(如分子动力学与连续介质力学的耦合)将是解决这一问题的关键,预计未来 5-10 年,商用软件将能实现更高效的多物理场耦合仿真。
人工智能与仿真的融合
人工智能(AI)技术为换热器仿真注入了新活力。机器学习算法可基于大量仿真数据训练预测模型,快速估算换热器性能,大幅缩短优化周期。例如,某研究团队利用 1000 组 Fluent 仿真数据训练神经网络,使换热器效能的预测时间从原来的 2 小时缩短至 0.1 秒,且误差小于 5%。强化学习算法可自主探索设计空间,找到人类工程师难以发现的最优结构。某企业利用强化学习优化微通道换热器的流道布局,在相同体积下使换热效率比传统设计提高 22%。
AI 还能提升仿真的智能化水平,如自动识别几何模型中的关键区域并加密网格,或根据仿真结果自动调整物理模型参数。未来,“AI 驱动的自适应仿真” 将成为主流,工程师只需输入设计目标与约束条件,系统即可自动完成建模、仿真、优化的全流程。
数字孪生与全生命周期仿真
数字孪生技术通过构建物理设备与虚拟模型的实时映射,实现换热器全生命周期的动态仿真与监控。在运行阶段,数字孪生模型可接收传感器实时数据(如进出口温度、压力、流量),通过仿真预测内部状态(如结垢程度、腐蚀速率),提前预警故障。某炼油厂的加氢换热器采用数字孪生系统后,通过仿真发现某根换热管因结垢导致热阻增加 15%,及时安排清洗,避免了非计划停机(单次停机损失约 500 万元)。
在维护阶段,数字孪生可仿真不同维护方案的效果,优化维护周期。例如,通过仿真预测不同结垢速率下的换热器性能衰减曲线,制定个性化清洗周期,比固定周期维护减少 30% 的维护成本。未来,随着物联网与传感器技术的发展,数字孪生将在换热器的设计、制造、运行、维护全流程中发挥核心作用。
挑战与应对策略
尽管仿真技术取得了显著进展,但其应用仍面临若干挑战。一是模型简化与实际的差异,过于简化会导致精度不足,而过度复杂则增加计算负担,需要建立 “精度 - 效率” 平衡的评估标准;二是材料属性与边界条件的不确定性,如流体物性参数随温度、压力的变化,需要引入不确定性分析方法(如蒙特卡洛模拟)量化其对结果的影响;三是仿真数据与实验数据的验证不足,部分企业因缺乏实验条件,难以验证仿真模型的可靠性,建议加强产学研合作,建立共享的实验数据库与验证平台。
为应对这些挑战,行业需加强基础研究(如复杂流动与传热机理)、提升软件自主研发能力(减少对国外商用软件的依赖)、培养跨学科人才(既懂传热学又掌握仿真技术与 AI 算法)。同时,推动仿真标准的制定,规范建模流程与结果评估方法,提高仿真数据的可信度与可复用性。
结语
换热器模拟仿真技术已从辅助工具升级为驱动创新的核心引擎,其应用深度与广度的不断拓展,正在重塑工业温控领域的发展格局。从传统行业的能效提升到高端制造的技术突破,仿真技术带来的不仅是性能优化的数字,更是工业思维的变革 —— 从 “经验驱动” 向 “数据驱动”、从 “试错迭代” 向 “精准设计” 的转变。
未来,随着多物理场耦合、AI 融合、数字孪生等技术的成熟,换热器的设计将更加智能、高效、个性化,为工业绿色低碳发展、能源高效利用、高端装备自主可控提供坚实支撑。在这场技术革命中,掌握仿真工具、具备创新思维的企业与人才,将在激烈的市场竞争中占据先机,推动换热器技术迈向新的高度。
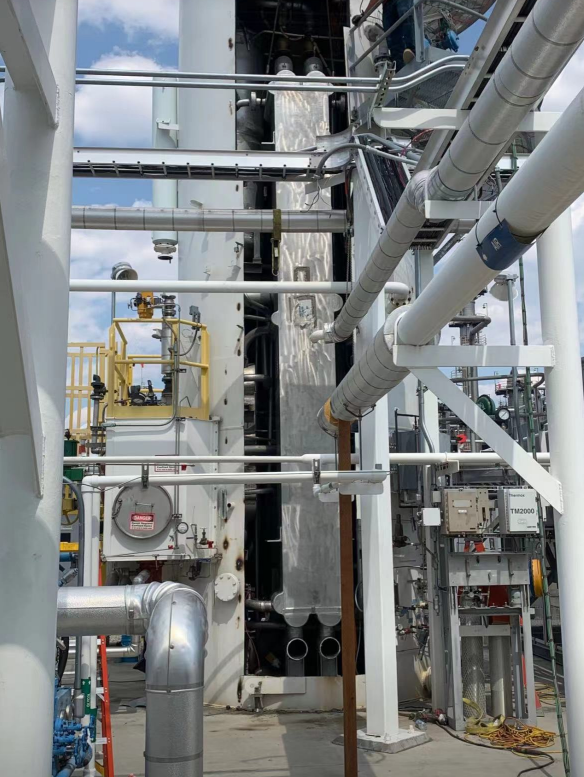