在全球工业迈向智能化、绿色化的进程中,反应釜、乳化机、发酵罐等核心装备的技术突破正成为产业升级的关键引擎。以磁力传动为代表的无泄漏密封技术,与高剪切乳化、智能发酵等前沿工艺深度融合,不仅破解了传统设备的泄漏、高维护成本等痛点,更推动化工、医药、食品、环保等领域向零泄漏、高能效、智能化方向迈进。本文聚焦 A 类 17 项、B 类 9 项、C 类 22 项关键装备技术,深度解析行业变革背后的技术逻辑与应用实践。
一、A 类核心装备:磁力驱动重构反应设备技术体系
(一)反应釜家族的技术突围:从高压场景到精密合成
在化工合成的心脏地带,聚合釜与搅拌釜正经历着磁力驱动技术的全面革新。某跨国化工企业在尼龙 66 聚合工艺中,采用新型磁力耦合聚合釜,通过优化磁路设计,使反应温度控制精度提升至 ±0.5℃,分子量分布均匀性提高 30%,单批次产能突破 20 吨。而在医药中间体生产中,搅拌釜搭载的反应釜搅拌器采用磁力传动技术后,物料混合效率提升 40%,彻底解决了传统机械密封在强腐蚀环境下的泄漏隐患。
加氢反应釜系列在能源与材料领域展现强劲实力。某新能源企业的连续加氢反应釜生产线,通过串联三级磁力密封装置,将氢气泄漏率控制在 0.001ppm 以下,成功实现锂电池正极材料前驱体的连续化生产,产能较间歇式设备提升 60%。而在高压聚乙烯生产中,高压反应釜配备的大扭矩磁力耦合器,可承受 200MPa 压力与 300℃高温,传动效率达 95%,设备寿命延长至 10 年以上。
(二)磁力传动技术:从密封革命到全场景适配
作为无泄漏传动的核心,磁力传动与磁力驱动技术正重塑设备设计逻辑。某德资企业研发的磁力反应釜,通过钕铁硼永磁体与碳化硅轴承的组合,实现了 10^-7Pa・m³/s 的超低泄漏率,成为制备高纯电子级溶剂的首选设备。而在实验室场景,磁力搅拌反应釜凭借微型化设计与精准控温功能,帮助科研团队在纳米晶合成中实现粒径分布 CV 值<5%,相关成果发表于《自然・材料》。
磁力密封反应釜的应用边界持续拓展。某海洋工程公司的深海磁力密封反应釜,在 500 米水深的极端压力下稳定运行超 10000 小时,支持可燃冰开采模拟实验的关键数据采集。工业级电加热搅拌罐与磁力搅拌机的协同方案,更在锂离子电池电解液混合中展现优势,将批次混合时间缩短至 15 分钟,能耗降低 40%。
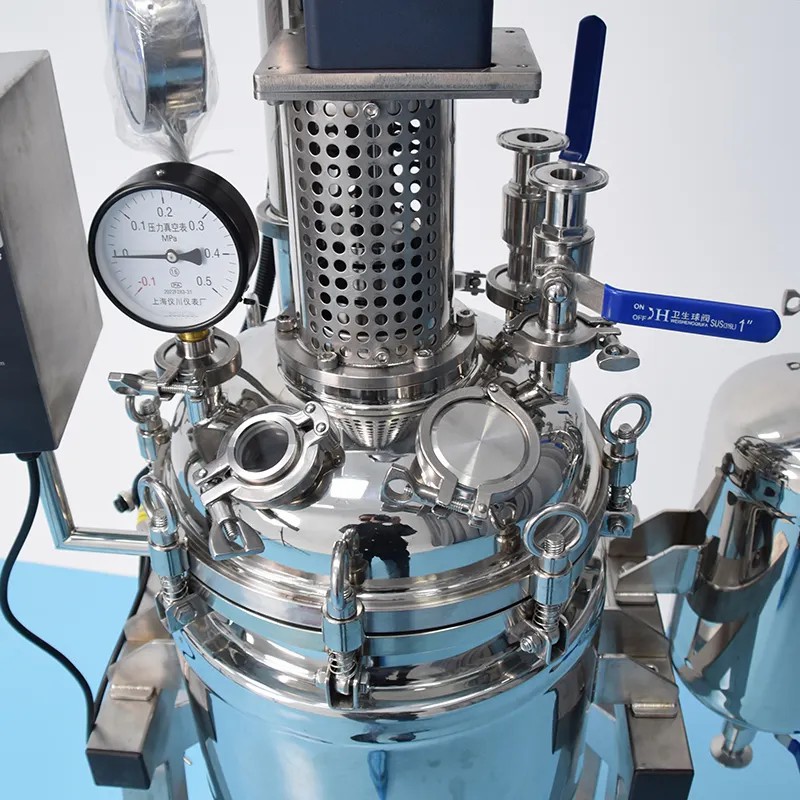
二、B 类乳化设备:从实验室研发到工业化生产的精度革命
(一)实验室级乳化:配方研发的核心引擎
在化妆品与生物医药领域,实验室乳化机正成为纳米级配方研发的标配。某国际美妆集团的研发中心,通过高剪切均质乳化机将抗衰老精华液的粒径控制在 50 纳米以下,经真空均质乳化机脱气处理后,乳液稳定性提升至 36 个月。而在 mRNA 疫苗制备中,实验室乳化机配合微流控技术,实现脂质纳米颗粒(LNP)的包封率达 98%,为新型疫苗的快速量产奠定基础。
(二)工业级乳化:规模化生产的效率标杆
乳化机家族的工业化应用展现强大动能。某乳制品企业的高剪切分散乳化机生产线,通过三级剪切结构将牛奶脂肪球粒径降至 0.1 微米以下,产品口感细腻度提升 70%,年产能突破 50 万吨。而在涂料行业,高剪切乳化机处理石墨烯浆料时,分散效率较传统设备提升 3 倍,导电性能达 10^5 S/m,推动高端防腐涂料的技术升级。
真空乳化机在洁净生产中优势显著。某制药企业的真空均质乳化机系统,在无菌环境下完成眼用乳膏的制备,通过 PLC 智能控制实现乳化转速、真空度、温度的精准匹配,微生物污染风险降低至十亿分之一以下。
三、C 类多元设备:全行业场景的协同创新
(一)储罐与配料系统:洁净生产的基石
在食品医药领域,不锈钢搅拌罐、不锈钢配料罐、不锈钢配液罐构建起精密的物料处理体系。某疫苗企业的不锈钢配液车间,30 台不锈钢配液罐通过 DCS 系统联动,实现培养基配制的精度误差<0.1%,配合 CIP/SIP 系统,确保每批次产品的微生物负载<10CFU。而在调味品行业,不锈钢配料罐的智能称重系统,使酱油酿造的氨基酸态氮含量稳定在 1.2g/100mL,品质波动率小于 0.5%。
(二)发酵与提取:生物工程与环保的双轮驱动
发酵罐家族在可持续发展中扮演关键角色。某环保企业的餐厨垃圾发酵罐,通过高温好氧发酵技术,将有机质降解效率提升至 98%,单日处理量达 50 吨,副产有机肥符合 NY/T 525 标准。而在生物制药领域,生物发酵罐的全自动控制系统,实时监控溶氧、pH、浊度等参数,使重组蛋白表达量提升 20%,发酵周期缩短 15%。
提取浓缩设备推动中药现代化进程。某中药企业的多功能提取罐,采用动态逆流提取技术,使三七皂苷提取率提升至 95%,溶剂消耗量减少 40%。配套的浓缩罐通过双效蒸发工艺,将蒸发强度提升至 50kg/(m²・h),有效保护热敏性成分。四、技术融合:跨领域应用的无限可能
(一)磁力驱动与乳化设备的协同创新
当磁力搅拌机遇见高剪切乳化机,物料处理进入 “无泄漏 + 高精度” 时代。某锂电池企业的电极浆料制备线,磁力搅拌反应釜与高剪切分散乳化机串联运行,将导电剂分散时间缩短 50%,且无任何润滑剂污染风险,电池能量密度提升至 300Wh/kg。而在纳米纤维素生产中,磁力耦合器驱动的乳化罐,通过变频控制实现剪切速率 10^5s^-1,制备出直径<20 纳米的纤维素晶须,成为高端涂料的关键原料。
(二)环保与能源:设备技术的新战场
在 “双碳” 目标下,混凝土搅拌罐与高温搅拌罐的节能改造如火如荼。某建材集团的混凝土搅拌罐搭载余热回收系统,使每立方米混凝土能耗降低 30%,年节约电量相当于 2000 户家庭的年用电量。而在生物质能源领域,电加热搅拌罐配合磁力驱动技术,实现藻类油脂提取效率提升 40%,为生物柴油规模化生产提供装备支撑。五、未来趋势:智能化、模块化、绿色化三大方向
(一)智能化:从设备到产线的数字孪生
随着工业 4.0 深入,发酵罐设计与反应釜搅拌器融入 AI 算法,实现预测性维护与工艺优化。某生物制药厂的生物发酵罐通过数字孪生技术,将染菌率降低至 0.1%,设备综合效率(OEE)提升 25%。而不锈钢储罐的物联网系统,实时监控液位、温度、压力等 12 项参数,异常报警响应时间<10 秒。
(二)模块化:快速适配多元场景
多功能提取罐与高剪切乳化罐的模块化设计,让产线切换时间从 24 小时缩短至 4 小时。某日化企业的柔性生产线,通过更换乳化机的定子转子组件,可在上午生产洗发水、下午生产面霜,产能利用率提升 30%。实验室级高速分散均质机与工业级设备的参数无缝对接,更加速了研发成果的转化效率。
(三)绿色化:低碳技术的深度渗透
磁力密封反应釜与真空乳化机的节能设计成为行业标配。某化工园区统计显示,采用磁力驱动设备后,园区整体泄漏率下降 80%,VOCs 排放量减少 60%。而餐厨垃圾发酵罐的沼气回收系统,单个处理站年发电量突破 1000 万度,相当于减少碳排放 6000 吨。
从聚合釜的分子级合成到乳化机的纳米级分散,从发酵罐的生物转化到不锈钢储罐的洁净储存,工业装备的每一次技术突破,都在重塑全球制造的底层逻辑。随着磁力驱动、高剪切乳化、智能发酵等技术的深度融合,设备正从单一功能单元进化为智慧生产的核心节点。未来,在 “双碳” 目标与数字化转型的双重驱动下,这些承载着创新基因的装备,将继续书写高效、绿色、智能化的产业新篇章。