随着现代化工技术的飞速发展,工业设备的创新成为推动行业进步的关键因素。新型浆态床反应器作为化工生产中不可或缺的设备之一,凭借其高效、环保、灵活的特点,在石油加工、精细化工、生物医药等多个领域展现出巨大潜力。
浆态床反应器是一种将固体催化剂颗粒悬浮于液体反应介质中形成浆态,通过搅拌实现气、液、固三相充分接触的化学反应装置。相比传统反应器,浆态床反应器具有更高的传热传质效率、更宽的操作条件范围和更强的处理能力,尤其在处理高粘度、高固体含量的反应体系时表现出色。然而,传统浆态床反应器在搅拌效率、密封性能及能量消耗方面仍存在诸多挑战。为此,引入磁力技术的新型浆态床反应器应运而生,为这些问题提供了创新解决方案。
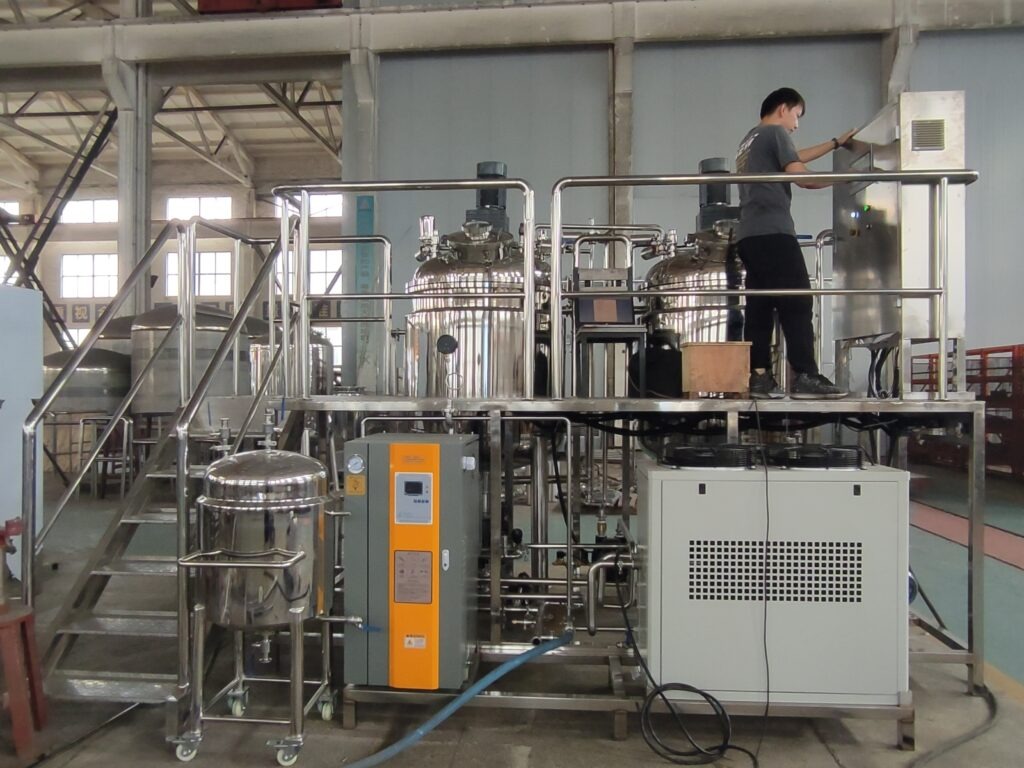
重要组成
新型浆态床反应器的核心在于其创新的磁力驱动系统,主要包括以下几部分:
1. 磁力重油分散乳化机系列:利用磁力驱动原理,实现高效、无泄漏的分散乳化过程,特别适用于重油等难处理物料的处理。
2. 磁力座测量联轴器同轴度:确保磁力驱动装置与反应器轴线的精确对中,提高运行稳定性和使用寿命。
3. 磁耦合传动磁力搅拌反应釜:采用磁耦合传动技术,避免了传统机械密封的泄漏问题,同时实现了高效搅拌,提高了反应效率。
4. 磁耦合传动高压静密封与磁耦合密封技术:这是新型浆态床反应器的关键技术之一,通过磁力作用实现动静部件间的无接触密封,有效解决了高压、高温环境下的泄漏难题。图1展示了磁耦合密封技术的示意图,直观体现了其工作原理。
磁耦合密封的优势在于无需润滑剂、无泄漏、维护简便,且能适应极端工况。其原理基于内外磁体间的磁力作用,通过非接触方式传递扭矩,实现了高效、可靠的密封效果。
应用领域
新型浆态床反应器凭借其独特的优势,广泛应用于以下领域:
石油化工:用于重质油加氢裂化、催化剂再生等过程。
精细化工:在合成树脂、染料、农药等生产中提高反应效率和产品质量。
生物医药:用于发酵、细胞培养等生物反应过程,确保无菌操作。
环境治理:处理废水、废气中的有害物质,实现环保减排。
应用案例介绍
以某大型石化企业为例,该企业采用新型浆态床反应器进行重质油加氢裂化。通过引入磁力重油分散乳化机系列,显著提高了原料的分散均匀性和乳化效果,为后续加氢反应创造了有利条件。同时,采用磁耦合传动磁力搅拌反应釜,不仅避免了传统密封方式的泄漏问题,还通过精确调节搅拌速度,优化了反应条件,使加氢裂化效率提高了20%,能耗降低了15%。此外,磁耦合密封技术的应用,确保了整个系统在高压、高温环境下的稳定运行,为企业带来了显著的经济效益和环境效益。
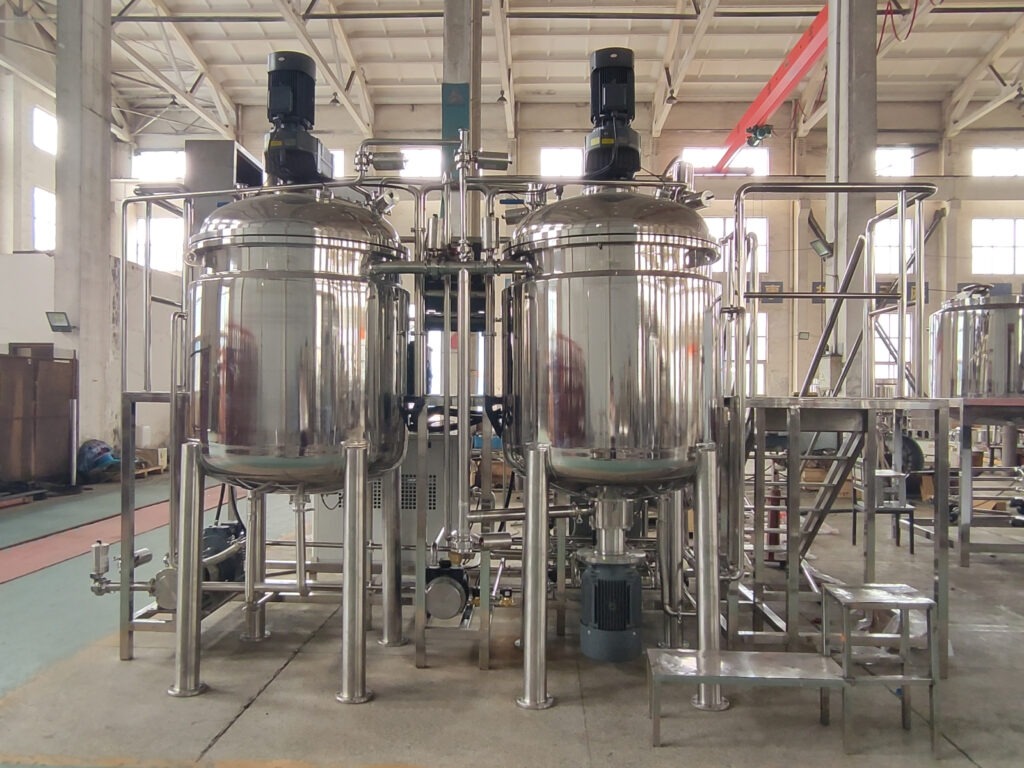
展望未来,新型浆态床反应器将朝着更高效、更智能、更环保的方向发展。具体体现在:
技术融合:结合物联网、大数据等现代信息技术,实现反应过程的远程监控和智能调节。
材料创新:开发耐高温、耐腐蚀的新型磁性材料,进一步提升磁耦合密封的性能和使用寿命。
系统集成:优化反应器设计,实现与上下游工序的无缝对接,提高整体生产效率。
特别地,在磁力驱动系统方面,大扭矩磁力和大扭矩磁耦合传动器的研发将是关键。大扭矩圆盘形磁力耦合器能够传递更大的扭矩,适用于更大规模、更高负荷的反应器,进一步拓宽了新型浆态床反应器的应用范围。同时,底部磁力搅拌机和顶部长轴磁力搅拌机的设计创新,将满足不同工艺需求,提升搅拌效率和反应均匀性。
综上所述,新型浆态床反应器凭借其磁力技术的创新应用,在解决传统反应器面临的搅拌效率、密封性能及能耗问题方面取得了显著成效。随着技术的不断进步和应用的深入,新型浆态床反应器将在更多领域展现出其独特的价值,为推动化工行业的绿色、可持续发展贡献力量。