铝质板翅式换热器以其紧凑的构造、轻量化设计、卓越的强度及高效的热交换能力,在汽车行业、工程机械、化工产业、制药工业、纺织领域及空气分离设备等众多行业中扮演着不可或缺的角色。作为其核心制造技术,钎焊工艺尤其是真空钎焊技术的应用,不仅替代了传统盐浴钎焊带来的环境污染与能耗问题,更以其成熟的技术体系成为行业首选。真空钎焊,在严格的真空环境下进行,无需额外钎剂,依赖毛细现象促使钎料渗透至焊接界面,实现金属间的牢固结合,且能同时处理多个组件,提升了生产效率。
鉴于铝制板翅式换热器作为压力容器的特殊性质,其内腔的密封性能与承压能力至关重要。鉴于其复杂的结构特性,芯体内各部件间的连接完全依赖于高质量的硬钎焊工艺,以确保整体结构的稳固与性能达标。
换热器的结构及工艺流程
2.1 换热器的结构
铝制板翅式换热器芯体的结构由大封条、小封条、双金属复合板、大翅片、小翅片及侧板组成。
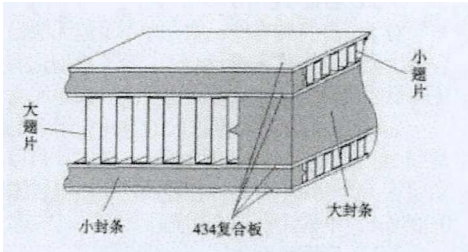
图1 换热器芯体结构
2.2 生产工艺流程
(1)材料切割与预处理:针对双金属复合板、翅片、封条及侧板,执行精确的剪切作业,同时对翅片进行成型处理,封条则进行锯切以满足尺寸要求。
(2)表面清洁处理:利用超声波清洗技术,对部件表面进行深度清洁,去除油污及杂质,确保焊接面洁净无污。
(3)部件组装:通过机械手段,将隔板、翅片、封条及侧板等精确组合,形成换热器的初步结构框架。
(4)真空环境钎焊工艺:在真空炉中实施五阶段温控钎焊过程,首先预抽真空,随后逐步升温至各阶段设定温度(依次为200~260℃、380~400℃、470~520℃、565~585℃、最终钎焊温度597~605℃),每阶段保持一定时间以确保焊接质量,最终在保温1525分钟后停止加热,待工件冷却至200℃以下方可出炉。
(5)芯体矫正与端盖焊接:针对钎焊后可能产生的变形,采用机械方法进行芯体整形。随后,使用氩弧焊技术将端盖牢固焊接于换热器芯体的两端。
(6)压力测试与泄露检测:向换热器内通入1.6Mpa至2Mpa的洁净压缩空气,进行压力测试,以检验其密封性能,并通过手工方式标记出任何泄露点。
(7)修复与再测试:针对检测出的泄露点,对换热器进行锯开补焊处理,随后再次进行压力试验,确保内腔密封性完全达标。
(8)表面处理与美化:对换热器整体进行细致整理,喷涂保护漆并进行烘干处理,以提升其外观质量及耐用性。
(9)最终包装与交付:完成所有工序后,对换热器进行妥善包装,准备交付给客户。
3 泄露原因分析
3.1 换热器原材料
3.1.1 隔板合金成分及包覆层厚度
隔板的钎焊效能显著体现在其熔融液体的流动性、对焊接表面的润湿特性、微小间隙的完全填充能力、对基体材料的溶蚀程度以及最终接头的机械强度。包覆层内Si元素的含量不仅作为合金熔点高低的直接指标,还深刻影响着合金的流动性与润湿效果,以及潜在的溶蚀倾向。具体而言,高Si含量促进了良好的流动性和出色的间隙填充能力,但过度时,Si的扩散至基体界面可引发固相成分的钎焊成分化,导致固相熔化,形成溶蚀现象。
在包覆层合金中,Mg元素扮演着至关重要的角色,它既是提升真空钎焊质量的必要金属活化剂,也是有效的吸气剂。当钎焊温度超过550℃时,Mg开始大量蒸发,在钎焊室内形成一层保护性镁气氛。这层气氛通过与残余氧或水蒸气中的氧结合,有效防止了加热部件表面的二次氧化,并有能力渗透并消耗掉零件表面可能残留的氧化膜。
隔板包覆层的厚度均匀性对于避免虚焊、防止烧损、确保钎焊连续性和密封性至关重要。因此,精确控制钎料中的Mg含量在1.0%至2.0%之间,是保障焊接质量的关键措施之一。同时,确保钎料层具有足够的有效厚度,以形成饱满的钎焊缝,从而提升产品的承压性能。实践证明,隔板每侧包覆层厚度维持在0.1至0.15毫米之间,能够充分满足真空钎焊的工艺要求,确保焊接质量达到预期标准。
3.1.2 焊前零件表面处理
在换热器芯体的组装筹备阶段,翅片、隔板、封条及侧板等核心部件均需严格遵循换热器芯体零件清洗作业指导书中的规范,进行超声波清洗处理。此步骤旨在彻底清除附着于表面的污垢、油污及氧化膜,确保焊接面的清洁度。油污若在真空钎焊过程中受热分解,不仅会削弱炉内真空度,还可能促使翅片、隔板及封条等部件加速氧化。特别值得注意的是,铝合金表面的氧化膜极为致密,且其熔化温度(高达2050℃)远超基体材料,因此在钎焊过程中难以熔化,从而对焊接质量构成不利影响。
为确保工件钎焊的高质量完成,必须严格执行焊前表面处理标准,严格控制工件与钎料的清洁度,并尽量缩短从清洗到装配的时间间隔,以减少污染风险。清洗效果的评估则采用36号达因笔进行画线测试:若画线收缩成线状或形成珠点,则表明清洗质量未达标准;相反,画线均匀无珠点,则证明清洗效果良好。
3.1.3 封条的外观形状和表面粗糙度
此外,结构件表面的粗糙度也是影响钎焊质量的关键因素之一,尤其是通过毛细力作用的钎焊过程。表面过于光滑可能导致钎料难以均匀铺展于整个接触面,进而形成空穴,削弱钎焊强度。特别是对于封条等关键部件,其钎焊面的粗糙度需特别关注,以确保钎料能够均匀且有效地覆盖整个焊缝,提升焊接强度。因此,对封条等部件的钎焊面进行适当的粗化处理,是保障钎焊质量不可或缺的一环。
3.2 换热器的装配
零件组装质量的优劣与产品钎焊质量的好坏密切相关,应引起足够的重视。首先,要控制零件的高度公差。根据国家标准,片的高度公差为-0.02mm~+0.05mm,封条的高度公差为-0.03mm+0.03mm,在实际应有中,应避免翅片负公差与封条正公差的配合一般以翅片公差高于封条公差 0.03mm左右为宜。换热器装配后用夹具夹紧,由于铝和不锈钢夹具的热膨胀系数不同,夹紧力太大易造成钎焊后翅片弯曲倒伏,夹紧力大小易造成翅片虚焊、松脱。
3.3 真空钎焊工艺
3.3.1 真空钎焊温度
隔板表面涂覆的钎料,其熔化过程对温度有着特定的要求。钎焊温度的选择至关重要,它不仅关乎钎料能否充分浸润并扩展至焊接界面,还直接决定了钎焊接头的最终连接强度。若温度设定过低,未能达到钎料的熔化点,或各焊接区域温度分布不均,将导致钎料流动性受限,进而引发虚焊现象,钎缝不连续,焊缝强度显著下降,增加泄露风险,极端情况下甚至可能造成部件鼓胀撕裂。此类问题在实际生产中屡见不鲜,部分原因可归咎于小翅片与封条之间间隙配合的不精确。实验观察表明,仅5毫米长度的小翅片若发生脱焊,在低于3.5MPa的压力下即有可能出现鼓胀变形。
另一方面,若钎焊温度过高,虽然能确保钎料完全熔化,但也可能带来新的问题。过高的温度会促进钎料内部气孔的形成,同时加剧钎料的过度扩散,导致钎料流失和溶蚀现象的发生,最终削弱产品的承压性能。因此,在钎焊过程中,精确控制温度,避免过低或过高,是确保焊接质量、提高产品可靠性的关键环节。
3.3.2 真空炉的真空度
在真空钎焊中,钎料和某些蒸汽组分之间的相互作用会显著地影响钎焊特性。钎焊炉真空度低时,炉内的氧气、水蒸汽等氧化性气体与铝起化学反应生成难容的氧化膜,氧化膜熔化温度2200℃以上,在散热器钎焊温度下不分解,阻隔了钎料向母材的浸润扩散。抽真空与升温有一个过程,依据工件的大小、重量不同,抽真空与升温的时间也不同。一般温度小于450℃,真空度控制在 0.02pa以下,在钎焊阶段应在 0.003pa 以下,良好的真空度对钎焊缝的质量影响较大。
3.3.3 真空钎焊时的环境状况在真空钎焊时,环境大气温度及湿度都会对铝制板式换热器钎焊质量造成很大的影响。在湿度大的条件下进行组装时会有更多的水分留在芯体零件上,人炉后会释放水蒸气,降低钎焊炉的真空度。同时由于水蒸气的蒸发需要大量的热量,会影响到工件的温度。环境湿度的高低直接影响真空钎焊质量。
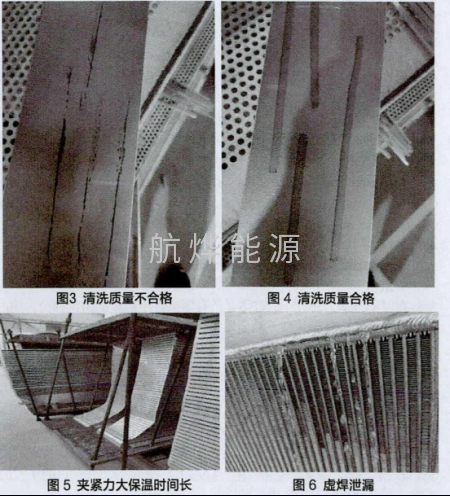
为了全面提升航烨能源产品中的真空钎焊质量,我们需从源头至终端实施一系列精细化管理与控制措施。首先,原材料采购必须严格筛选,确保所有材料均源自正规、专业的供应商,以此为基础,保障材料本身的质量与性能达到最优。具体到翅片与封条的公差控制上,翅片公差应精确限定在0.03mm至0.05mm之间,而封条公差则应更为严格,控制在0至0.03mm范围内,理想状态下,翅片应略高于封条约0.03mm,以促进更好的配合与焊接效果。
备料阶段,我们需严格遵循既定工艺程序,确保每一步操作都准确无误。清洗剂的选择同样关键,其PH值应不低于7.5,以避免对零件造成不必要的损害。零件清洗后,需立即进入组装流程,两者之间的时间间隔应严格控制在24小时以内,以防止零件重新受到污染。组装过程中,零件间的配合间隙需严格控制在0.03mm以内,确保装配精度。
针对真空钎焊工艺本身,我们需不断优化并严格控制各项关键参数,如温度、保温时间及真空度等。特别是在焊接阶段,真空度必须维持在0.003pa以下的极高水平,以确保焊接过程的稳定性和焊接质量的可靠性。同时,根据实际生产中的内外部条件变化,灵活调整钎焊工艺参数,以适应不同情况的需求。
在封条的技术要求上,除了基本的表面光洁平整、无裂纹、皱折、腐蚀斑点等规定外,我们还需根据实践经验与相关技术文件,将封条钎接面的粗糙度值进一步细化至Ra0.8~1.6μm之间,以提升钎焊接头的连接强度与密封性能。
最后,在环境控制方面,我们需确保真空钎焊车间内的相对湿度维持在30%~70%的适宜范围内,以减少湿度对焊接过程及焊接质量的不利影响。通过这一系列综合措施的实施,航烨能源将能够显著提升真空钎焊质量,为客户提供更加可靠、高性能的产品。