在染料、药物合成及精细化学品制造等关键领域,重氮化反应扮演着举足轻重的角色,然而,传统釜式重氮化操作常面临产品产率低下、中间产物稳定性差以及反应过程中热量急剧释放等挑战。为了克服这些难题,连续流反应技术应运而生,成为推动这些高风险工艺向更安全、更高效方向转型的有效手段。本文旨在综述连续流重氮化反应技术的最新应用进展,展现其如何通过连续、可控的反应过程,改善产品收率,稳定反应中间体,并有效管理反应热,从而为工业生产带来显著优势。
重氮化反应,作为芳香族一级胺及脂肪族伯胺与亚硝酸或亚硝酸盐在过量酸催化下低温合成的重氮盐的关键步骤,是多种高级化学反应(诸如Sandmeyer、Gattermann、Schiemann、Gomberg-Bachmann、Pschorr及Heck反应)不可或缺的中间环节。然而,传统釜式重氮化操作受限于低温下的亚硝酸钠溶液缓慢滴加,此过程常伴随以下弊端:一是重氮化合物与残留反应物长时间接触,诱发多种副反应;二是反应释热剧烈,而釜式反应器在热质传递上的局限性易导致局部过热;三是自动化程度有限,增加了操作风险乃至爆炸事故的风险,从而限制了其规模化生产潜力。
鉴于此,探索高效且安全的重氮化技术成为化工行业的重要课题。连续流技术,历经近三十年的科研深耕与工业实践,已逐步成熟并广泛应用于多个领域。相较于传统釜式反应,连续流技术展现出显著优势:首先,其卓越的传热传质能力确保了反应的高效进行;其次,对反应条件的精准调控提升了产品的质量与稳定性;再者,连续操作模式下物料在线存量低,显著增强了过程安全性;最后,该技术还便于生产规模的灵活调整与扩展。
因此,将连续流技术引入重氮化工艺,不仅是对传统方法的革新,更是解决当前釜式重氮化局限性的有效途径。本文旨在综述连续流重氮化反应技术的最新研究进展,探讨其在提升反应效率、优化产品性能及增强生产安全性方面的潜力与应用前景。
重氮化反应,作为精细化学工业领域内频繁出现的化学反应,尽管其重要性不言而喻,却因其复杂的副反应网络及在常规条件下重氮化合物迅速生成的特性而面临挑战。遗憾的是,尽管这一反应在工业生产中占据关键地位,但针对其深入的理论研究却相对匮乏,限制了对其反应机理、条件优化及副产物控制的全面理解。因此,加强对重氮化反应的理论探索,对于提升反应效率、减少副产物生成及推动精细化工领域的进步具有重要意义。
案例介绍:柠檬黄的合成工艺
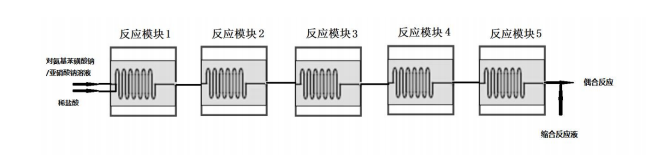
图1 连续流重氮化-偶合实验流程图
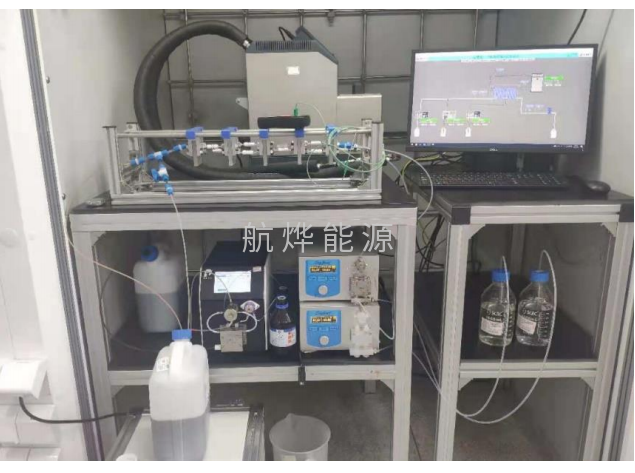
图2 重氮化微通道连续流实验装置
连续流反应流程如图所示:
(1)原料的配制:取一定量的对氨基苯磺酸溶于适量水中,将30%的氢氧化钠(NaOH)溶液逐滴滴入对氨基苯磺酸悬浊液中,待其变为澄清溶液后,加入适量的NaNO2,待NaNO2完全溶解,作为反应液A;将盐酸适量稀释后(稀释比例根据反应液A的浓度变化,保持微通道两路原料流速相当),作为反应液B;
(2)缩合液的制备:开启加热冷却循环器,将换热介质输入微通道换热层,将反应液A和反应液B通过平流泵以稳定流速输入微通道反应器的物料层,进行重氮化反应。在获得的重氮盐溶液中加入DMAS,边搅拌边加入15%的Na2CO3溶液,将pH值调至7.0,反应3h,得到缩合反应液C。
(3)重氮化-偶合反应:开启加热冷却循环器将换热介质输入微通道换热层,将反应液A和反应液B通过平流泵以稳定流速输入微通道反应器的物料层,进行重氮化反应,在反应器尾端将缩合液C定量通入进行偶合反应。
(4)水解反应:收集偶合反应液,用15%的Na2CO3溶液将其pH值调至9.0,加热2h,水解后得到柠檬黄溶液。
缩合反应的工艺条件为DMAS(nDMAS/n对氨基苯磺酸=1.02:1),反应温度为25℃,缩合pH值为7,反应时间为2h;固定偶合反应的工艺条件为反应温度25℃;水解温度为80℃,水解时间为2h。
总结
本文所探讨的案例,虽目前多处于实验室探索阶段,但近十年来,随着输送设备的更新换代与管道设计的不断优化,连续流重氮化反应技术正稳步实现从实验室向中试乃至大规模生产的跨越,预示着其在工业领域的广阔应用前景。
尽管连续流技术在重氮化反应中展现出诸多优势,但仍需攻克几项关键挑战。首要难题是流动性问题,副产物的低水溶性易导致管道堵塞,影响生产连续性。其次,产气问题不容忽视,重氮化过程中释放的氮气在大量产生时,即便实验室条件下可通过背压阀或特殊材质管壁内膜控制,工业应用时却可能因气量过大而危及管式反应器的安全。此外,废酸废水处理亦是一大考验,亚硝酸钠作为常用重氮化试剂,需配合高浓度酸以减少副反应,但这同时也带来了大量废酸排放的环保问题。
航烨能源秉持着“创新驱动发展,追求高效卓越,坚守可靠品质,倡导绿色环保”的核心理念,矢志不渝地致力于提升产品与服务的品质,旨在为全球能源行业的可持续繁荣贡献关键力量。我们敏锐捕捉时代脉搏,深度融合智能化与定制化两大趋势,为能源行业带来前所未有的变革。