在强放热反应中,一旦失控,反应速率会飞速提升,温度飙升,且因反应速率快、放热量大,体系中会积聚大量易燃易爆的不稳定物质。相较于常规连续反应,强放热反应的连续化生产在安全性上面临更大挑战。因此,确保反应安全性的核心在于强放热反应釜的安全设计。尽管已有如张本贺等的研究为强放热反应的间歇工艺提供了宝贵指导,但在针对强放热反应连续化过程的安全设计方面,现有研究仍显不足,这一现状限制了此类反应在工业生产中的大规模应用与发展。
1 反应过程的连续化技术
在含能化合物、精细化工及特种化工等高风险强放热且易于失控反应的生产领域,采用微反应技术和连续流工艺替代传统的间歇法已成为未来发展的主流趋势。近年来,科研界正积极投身于探索如何利用连续流技术革新传统生产方式,旨在通过这一转变来优化生产过程,提高安全性与效率,众多研究项目正致力于此方向的深入开发与应用。
鉴于含能材料生产过程中反应剧烈且伴随大量不稳定混合物,半间歇装置的应用潜藏着显著的安全隐患。为了有效缓解这一风险,一种高效策略是采用一系列精心设计的、搅拌效果优异的连续多级反应釜进行生产。这种连续搅拌釜式反应器的优势显著:在维持相同生产效率的同时,它能更精准地调控放热过程,为生产规模的扩大提供更为宽裕的安全空间;此外,连续化生产模式确保了产品生产率与质量的稳定可重复,减少了繁琐的辅助操作,从而显著提升了整体生产效率。因此,从安全性与经济效益的双重考量出发,连续操作模式无疑是对半间歇及间歇操作模式的优越替代。
显然,相较于间歇法,连续化技术,特别是连续釜的应用,在技术和实践层面均展现出非凡的优势,不仅促进了产能的飞跃,还提升了产品产出率。然而,在精细化工与特种化工领域,连续化生产的推进并非毫无障碍,其面临的主要技术挑战包括反应机理的错综复杂以及反应过程中释放的大量热量等难题,这些都需要我们不断探索与创新,以克服瓶颈,推动行业进步。
2 强放热釜式反应器结构
2.1 搅拌釜结构
在强放热反应器的设计核心中,首要关注的是如何迅速且高效地移除反应过程中释放的大量热量。搅拌反应釜在含能化合物制备中备受青睐,主要归因于以下几点:一、搅拌装置能够显著削弱放大效应,通过增强反应器内流体的湍流程度,有效降低传质与传热的阻力,确保热量传递的高效性。二、搅拌装置的转速调节灵活且范围广泛,便于快速调整操作参数与反应条件,为工艺优化提供了极大的便利。三、搅拌反应釜的维护清洁工作简便,仅需打开釜盖与人孔即可轻松进行内部清洗,减少了维护成本与时间。
在实际操作中,为了直观监控强放热反应釜内的反应动态,常在釜盖内侧安装摄像头。同时,为提升安全性,釜底常配备紧急卸料口,以应对突发情况。
搅拌反应釜的构造主要由搅拌容器与搅拌机构成。搅拌容器集成了釜体、夹套、内部构件、接管及开孔等关键部件;而搅拌机构则包括搅拌器、搅拌轴、轴封、机架及传动装置等。依据搅拌桨设计的不同,搅拌反应釜可分为平叶型、弯叶型及螺旋面叶式等多种类型,每种类型均适用于特定的工艺需求。图1-1展示了一个典型的搅拌反应釜结构示例。
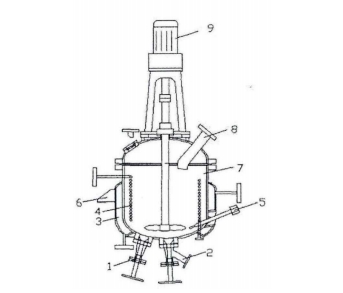
图1-1立式搅拌反应釜
1 紧急卸料阀 ; 2 常规卸料阀 ; 3 夹套 ; 4 盘管
5 温度计 ;6支座 ;7釜体 ;8进料口;9传动装置
2.2 搅拌器
搅拌器作为搅拌反应釜的关键组件,其核心功能在于将电能高效地转化为机械能,进而驱动周围流体产生强烈的湍流运动,这一转变显著降低了传质与传热过程中的阻力,优化了反应效率。搅拌器的性能及其诱导的流体流动形态,对搅拌釜的整体搅拌效果起着决定性作用,因此在搅拌釜的设计过程中,对流动形态(流型)的考虑至关重要。
搅拌桨的设计类型、其在容器中的插入方式、容器的几何形状以及搅拌器的旋转速度等因素,均会对流型产生深远影响。在工业生产的广阔舞台上,立式圆筒搅拌釜因其广泛的适用性而占据了重要地位,成为最常见的釜式反应器之一。这类搅拌釜展现出三种基础且典型的流型模式,如图1-2所示,每种流型都直接关联到搅拌效率、传热传质效果及反应过程的稳定性。
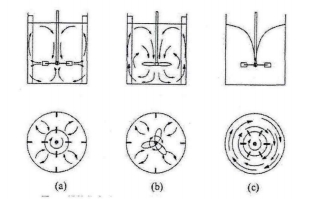
图 1-2 立式搅拌反应釜
1 紧急卸料阀 ; 2 常规卸料阀 ; 3 夹套 ; 4 盘管 ;
5 温度计 ; 6 支座 ; 7 釜体 ; 8 进料口 ; 9 传动装置
2.3 搅拌釜内传热部件
在强放热反应釜的操作中,维持反应温度的稳定性至关重要,而传热部件则扮演着减少物料温度波动的关键角色。搅拌反应器本体、夹套及其内部构件,如各种形式的盘管,均可作为有效的传热元件。
针对不同反应与工艺的具体需求,需精心挑选适宜的传热部件。若夹套的换热性能足以满足要求,则优先选用夹套方案,此举可避免在容器内部增设部件,保持流体流动的顺畅性,同时节省内部空间,简化清洁流程。然而,当夹套的换热效率不足时,内盘管便成为理想选择,此外,增设挡板或在空心搅拌器内通入载热介质也是增强换热的有效手段。
夹套依据其结构设计可分为整体式、蜂窝式、半管式及螺旋板蜂窝式等多种类型。其中,整体式夹套应用最为普遍,通常由普通碳钢制成,通过法兰连接或焊接方式固定于反应器上,形成中空结构。此类型夹套结构简单,成本经济,但受限于其几何形态,往往尺寸有限,换热能力相对固定,难以通过调整换热面积来优化性能。
鉴于单独使用夹套冷却可能无法满足强放热反应的严苛换热需求,通常会辅以盘管设计以增强换热效能。盘管内的流体流动方向持续变化,产生的离心力促使流体形成二次环流,显著增强了扰流效果,从而提高了对流传热能力。此外,盘管还具备一定的导流功能,部分替代了挡板的作用,进一步优化了反应釜内的流体动力学特性。
3 连续搅拌釜停留时间分布的研究
含有盘管的连续搅拌釜,凭借其卓越的传热效率和灵活的温控特性,在强放热反应尤其是含能化合物生产中占据了重要地位。针对诸如硝化反应器等处理强放热过程的反应釜,除了高效的传热能力外,良好的混合性能同样不可或缺。这意味着在设计此类反应器时,必须全面考虑其综合性能。
为了实现这一目标,对流动反应器的停留时间分布进行精确测定显得尤为重要。这一过程不仅能够帮助我们深入了解反应器内部的流体动力学行为,还是确立反应器内流动模型及计算模型参数的关键步骤。通过科学的数据分析,我们能够更准确地掌握反应器内的流动状况,为后续的优化设计提供坚实的数据支撑,从而确保反应器既能有效应对强放热挑战,又能实现反应物的充分混合,提升整体生产效率与安全性。
4 化工设备的本质安全设计
在工艺设计流程中,一旦操作条件与原料确定且波动范围有限,化工设备的设计便成为保障工艺总体安全性的关键环节。为确保整个工艺过程的本质安全,必须从设备设计的源头融入安全理念。
化工设备的本质安全设计,其核心考量在于安全泄压装置的配置、设备类型的选择以及材料的适用性等方面。特别是在含能材料的生产中,鉴于反应过程常伴有高强度放热,若温度控制失当,极易形成热点乃至引发爆炸,因此其生产设备的本质安全设计显得尤为迫切和重要。
另一方面,螺旋盘管反应器凭借其独特的螺旋结构,在垂直于主流方向的截面上形成了二次涡流,从而强化了传热与传质过程。周静等人在混酸硝化苯工艺中引入新型螺旋盘管反应器,实验证明其显著提高了硝化苯的选择性,且能及时移除强放热反应中的热量,增强了工艺的本质安全性。
搅拌釜作为含能化合物合成与精细化工中的常用设备,其本质安全设计对于提升生产安全性至关重要。
为防止反应器或设备因超压而引发危险,设计并安装安全泄压装置至关重要,其中安全阀是最为常用的设备之一。安全阀依据其工作机制可分为阀控型和爆破型两种类型,它们在工业应用中扮演着不可或缺的角色,确保压力反应器在安全范围内运行。一旦缺失这些关键部件,可能会引发严重的安全事故。
在探讨失控条件下安全控制的影响因素时,安全阀装置的选材问题凸显其重要性。因为安全泄放装置的有效性和耐久性直接受到介质腐蚀性、容器内部温度、压力以及结构类型等因素的影响。因此,在选择材料时,必须全面考虑这些因素,并兼顾材料的加工性能,以确保其在实际应用中的可靠性和稳定性。
在具体材料选择上,碳钢壳体因其良好的机械性能和加工性常被采用。然而,针对特定介质的腐蚀性,还需考虑使用耐腐蚀的金属材料或非金属衬里进行保护,以进一步提升安全阀装置的整体性能和寿命。
5 总结
在化工领域,强放热反应因其高能量释放特性,对反应器的设计与操作提出了严格要求。釜式连续化过程作为处理此类反应的有效手段,通过多釜串联、优化搅拌设计、强化传热等策略,实现了反应温度的稳定控制,有效避免了飞温及反应失控的风险。研究团队在釜型选择、搅拌桨型优化、盘管设计及夹套冷却系统等方面进行了深入探索,不仅提升了反应效率,还显著增强了工艺的安全性。此外,结合数学模型与仿真技术,对反应过程进行精确模拟,为工艺放大及安全设计提供了有力支持。这些研究成果不仅推动了含能化合物等高性能材料的制备技术进步,也为相关化工过程的连续化改造提供了重要参考。
航烨能源深知每个客户都有其独特的需求与挑战。因此,我们建立了专业的服务团队,通过一对一的深入沟通,全面了解客户的业务需求、应用场景及未来规划。在此基础上,我们运用专业的知识和丰富的经验,为客户量身打造符合其特定需求的能源管理方案。这些方案不仅能够有效解决客户当前的痛点问题,更能够预见并应对未来的挑战,助力客户在激烈的市场竞争中保持领先地位。