氦气,这一无色无味的稀有气体,以其独特的物理性质著称于世:它是自然界中沸点最低的气体,低至-268.9℃,且在空气中的含量极为稀少,仅为5.2×10-6。氦气以其低密度、极高的化学惰性、难以液化的特性,加之出色的稳定性、强大的扩散能力和极低的溶解度,展现出了非凡的应用潜力。然而,值得注意的是,氦气资源极为有限且不可再生,目前尚未发现纯氦气藏,其主要来源是天然气,特别是那些氦气含量超过0.1%的天然气田,具备较高的商业开采价值。
在国防安全、航空航天探索、核能工业、低温超导技术、科学研究、医疗诊断以及电子工业等多个关键领域,氦气以其独特的惰性保护作用,成为了不可或缺的战略资源。其重要性无可替代,对于推动科技进步、保障国家安全及促进经济发展具有重大意义。
1 主要提氦技术现状
在天然气中提取氦气的技术领域中,存在着两大类主要方法:低温法(亦称深冷法)与非低温法。非低温法进一步细分为多种技术,包括膜分离法、吸收法、扩散法以及吸附法等,这些方法各具特色。然而,在当前的工业实践中,深冷法与膜分离法因其高效性和实用性,成为了提取氦气的主流技术路线。深冷法依赖于极低的温度来实现氦气与其他组分的有效分离,而膜分离法则利用特殊膜的选择透过性,在不经历显著温度变化的情况下,将氦气从天然气中分离出来。这两种技术各有优势,共同推动着天然气提氦行业的发展。
1.1 深冷法
深冷法,作为一种先进的氦气提取技术,首先通过化学吸收与物理吸附的双重作用,彻底清除天然气中混杂的H2S、CO2、H2O及Hg等杂质。随后,利用烃类物质沸点各异的特性,在逐级液化与精细分离的过程中,将几乎不具备液化特性的氦气巧妙析出。此过程还需进一步通过脱氢精制技术,以确保最终获得的氦气纯度高达99.999%以上,满足严苛的工业与科研需求(如图1所示)。
值得注意的是,深冷法对于原料天然气的氦含量设定了较高门槛,通常要求不低于0.1%,且整个工艺流程相对复杂,需精细操作。然而,其显著优势在于技术体系的成熟稳定,能够确保较高的单次提取效率,并有效利用冷能资源,同时回收C2+等高价值副产品,实现了资源的最大化利用。因此,深冷法特别适用于大规模天然气提氦项目,已成为当前全球范围内从天然气中高效提取氦气的主流方法。
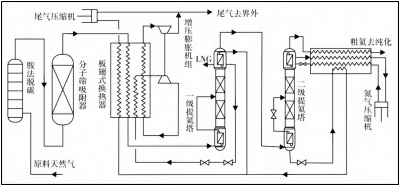
图1 深冷分离提氦工艺流程
1.2 膜渗透分离法
膜渗透分离技术,作为一种前沿的气体分离手段,其核心在于利用不同气体分子在膜表面渗透速率上的差异,在压力的作用下,通过膜的选择性渗透效应,实现目标气体的有效分离(如图2所示)。这一过程不仅实现了对特定气体的浓缩与富集,还展现了膜技术在气体提纯领域的独特优势。
相较于深冷法,膜渗透分离技术对原料气的品质要求更为严苛,且作为新兴技术,其全流程的工业应用尚属空白,国内外均缺乏实际案例支撑。因此,在选择此工艺时,膜的耐用性成为了一个至关重要的考量因素,它直接关联到工艺的经济性与可行性。
值得注意的是,即便采用了膜分离工艺对氦气进行了初步提浓,仍需后续配套催化脱氢与精制工序,以进一步提升氦气的纯度,最终获得满足高纯度要求的He产品。这一过程不仅体现了气体分离技术的复杂性与系统性,也强调了多工序协同作业在提升产品质量中的关键作用。
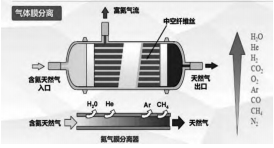
图2 膜渗透分离技术示意图
2 天然气提氦技术发展
随着液化天然气(LNG)产业的蓬勃发展,LNG尾气中的低浓度氦气通过蒸发气(BOG)富集技术,其氦气含量可显著提升至6%至8%,实现了数十倍乃至上百倍的浓度飞跃。鉴于此,近年来国内氦气回收领域出现了一个显著趋势,即在现有生产流程的后端增设BOG回收与提氦装置,以高效捕获并回收这些宝贵的氦资源。
与此同时,膜分离技术的持续进步为氦气提取开辟了新的路径。未来,直接运用膜分离技术从原料气及BOG中高效浓缩并回收氦气,被视为提氦技术的重要发展方向。接下来,我们将聚焦于三种关键技术路径进行深入探讨:一是原料气膜分离技术,旨在直接从天然气原料中高效分离出氦气;二是BOG深冷法,利用深冷技术进一步提纯BOG中的氦气;三是BOG膜分离法,则是将膜分离技术应用于BOG处理,以实现氦气的低成本、高效率回收。这三种工艺各具特色,共同推动着氦气回收技术的创新与发展。
2.1 原料气膜分离提氦技术
主要工艺流程:首先,经过严格预处理的天然气进入多级膜分离系统,通常包含三至四级,每级均精细操作以确保高效分离。其中,第三级膜分离尤为关键,被巧妙划分为两段操作:I段直接产出高浓度粗氦,这些粗氦随即被送往后续的脱氢装置进行深度处理;而同时产生的贫氦气则回流至II段膜,与新的天然气混合后再次进入I段,形成循环提浓机制,进一步提升氦气浓度。如图3所示。
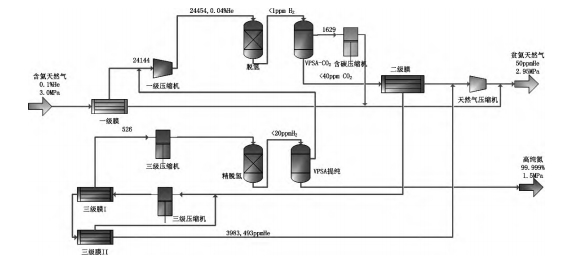
图3 原料气膜分离提氦工艺示意图
2.2 LNG-BOG 提氦技术
充分利用LNG挥发气气质纯净、杂质较少的特点,采用深冷或膜分离技术对BOG中的氦气进行回收提浓后采用催化脱氢和变压吸附工艺进一步提纯,具有较好的可行性和经济性。
2.2.1 BOG深冷工艺
BOG(蒸发气)在常压状态下,首先经历换热过程以提升其温度适应性,随后通过增压手段送入深冷分离装置。在深冷环境中,大部分甲烷与氮气得到有效脱除,从而生成含有氢气的粗氦混合物。这一含氢粗氦随后再次进行增压处理,并伴随换热以调整其状态,为后续纯化步骤做准备。
紧接着,增压并换热后的含氢粗氦进入催化脱氢与脱水阶段,通过特定的催化反应,有效去除其中的氢气成分,并同步进行脱水操作,以确保氦气的纯净度。这一系列处理后,粗氦的浓度显著提升,成为高浓度粗氦。
最后,高浓度粗氦流经精密的吸附装置,该装置利用其强大的吸附能力,将残留的微量杂质彻底清除,从而生产出纯度高达99.999%的高纯氦气。(如图4所示)
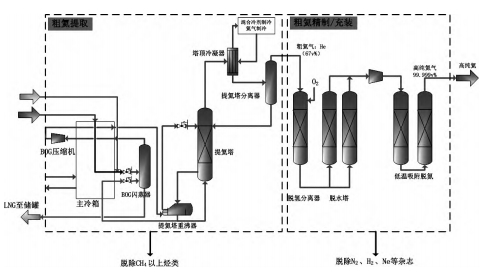
图4 LNG-BOG深冷分离提氦工艺示意图
2.2.2 BOG膜分离工艺
主要工艺流程与BOG深冷基本一致,将换热回收冷量后的BOG增压输入膜分离装置,提浓后获得含氢粗氦,再经过脱氢吸附精制获得高纯氦气(图5)。
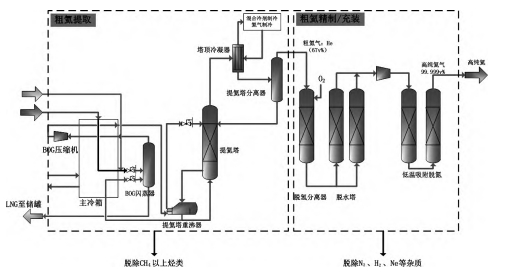
图5 LNG-BOG膜分离提氦工艺示意图
3 工艺技术对比分析
原料气深冷法提氦工艺的一大亮点在于其综合性效益,即在提取氦气的同时,还能高效回收天然气中的乙烷、丙烷等增值组分,甚至可选择性地联产液化天然气(LNG)等产品,从而最大化天然气的经济价值。然而,该工艺的不足之处在于其较高的能耗需求,特别是当考虑副产品回收时,工艺流程的延长会进一步加剧能源消耗。此外,初期投资成本也相对较大。相比之下,原料气膜分离工艺在能耗和投资方面展现出一定的优势,尤其是与同等规模的深冷工艺相比。但值得注意的是,膜分离工艺对原料气的预处理要求较高,否则可能影响分离效果和膜的使用寿命。同时,每级膜分离过程中,含氦天然气的增压操作也是必要的,且低浓度含氦天然气的初级膜分离效果对后续工艺选择具有重要影响。不过,该工艺在提取氦气时,无法同时回收天然气中的其他副产品。
另一方面,LNG-BOG深冷法提氦工艺则巧妙利用了LNG生产过程中BOG的低温特性,通过循环制冷实现氦气的进一步富集。这一工艺的优势在于其技术成熟度高、维护成本相对较低,但设备规模较大。而膜分离提氦工艺针对BOG中氦气含量高、杂质少的特点,通过一至两级膜操作即可有效富集氦气,膜组件用量少,投资成本相较于LNG-BOG深冷工艺更低。两者在BOG提氦方面均表现出良好的可行性和经济性,能耗差异不大,但均依赖于LNG工厂或大型LNG储罐的建设环境。
4 总结
天然气提氦技术现状呈现多元化发展态势,深冷法与膜分离法作为主流技术,各有优劣。深冷法技术成熟,适用于大规模提氦,能同时回收天然气中的高价值副产品,但能耗与投资成本较高。膜分离法则以能耗低、投资相对较少为优势,尤其适用于处理高浓度氦气,但对原料气预处理要求高,且膜组件寿命及性能影响显著。
航烨能源深知每个客户都有其独特的需求与挑战。因此,我们建立了专业的服务团队,通过一对一的深入沟通,全面了解客户的业务需求、应用场景及未来规划。在此基础上,我们运用专业的知识和丰富的经验,为客户量身打造符合其特定需求的能源管理方案。这些方案不仅能够有效解决客户当前的痛点问题,更能够预见并应对未来的挑战,助力客户在激烈的市场竞争中保持领先地位。