生物质热解炭化技术是一种将生物质原料在缺氧环境下通过加热引发其内部化学反应,进而形成生物炭、生物油和热解气的过程。这个过程主要包括三个连续的阶段:首先是干燥预热阶段,生物质在室温至130℃的温度范围内进行初步处理,使内部水分大量蒸发;接着是挥发分析出阶段,在130℃至450℃的温度区间内,生物质中的纤维素、半纤维素和木质素等有机物质受热分解,释放出挥发性气体;最后是炭化阶段,当温度超过450℃时,生物炭逐渐形成,留下富含碳的残留物。
生物炭作为这一技术的产物,具有多重应用价值。作为土壤改良剂,它不仅能够增加土壤中的有机物含量,提升土壤肥力,还能凭借其耐降解特性,延长碳在土壤中的封存时间,有助于缓解温室效应对全球气候的影响。此外,生物炭因其较大的比表面积和丰富的含氧活性基团,能够有效吸附土壤或污水中的重金属及有机污染物,成为一种潜在的活性炭替代品。
为了更高效、连续地实现这一过程,研究者们设计了连续式分段热解炭化设备。该设备采用分段式加热技术,包含5段独立的热解炭化炉,结合连续式输送原理,确保生物质原料的连续处理和高效转化。同时,设备还集成了生物炭循环水冷技术、热解气二次催化裂解技术和油气二级冷凝分离技术等,以进一步提高生产效率和产品质量。
连续碳化的工艺流程是一个高效且复杂的过程,它结合了生物质原料的炭化原理和连续输送原理,通过多个环节实现生物质的连续热解和炭化。以下是该工艺流程的详细说明:
密闭进料:首先,将生物质原料(如粉碎的玉米秸秆)通过进料口送入炭化炉,同时确保进料口和出料口的密封,以保持炉内的密闭环境。
分段热解炭化:在炉内,生物质原料经过多段热解炭化。每一段都设有特定的温度和压力条件,以控制生物质原料的热解速度和炭化质量。通过这种方式,生物质原料中的有机物在缺氧或低氧条件下被逐渐分解,生成生物炭、生物油和热解气。
油气分离:热解过程中产生的气体和液体混合物(即油气混合物)需要通过油气分离器进行分离。这一步骤可以确保生物油和热解气的纯净度,为后续利用提供基础。
生物炭循环水冷:分离出的生物炭需要经过循环水冷系统进行冷却。这一步骤不仅可以有效降低生物炭的温度,还可以减少其在后续处理过程中的安全风险。
热解气二次裂解:分离出的热解气被送入二次裂解装置,进行进一步的催化裂解。这一步骤可以提高热解气的利用价值,生成更多的可燃气体和化工原料。
尾气燃烧:最后,经过处理的尾气(即燃烧后的废气)被送入燃烧装置进行燃烧处理。这不仅可以减少环境污染,还可以回收部分热能,提高整个工艺流程的能量利用率。
整个工艺流程以生物质分段热解产炭为主路线,集成了热解混合气的分离收集、二次催化裂解和热解气燃烧等工艺。通过这种方式,既实现了炭、油、气的联产,又实现了焦油的去除和能量的高效利用。这种连续碳化的工艺流程在生物质能源利用领域具有广泛的应用前景和重要的环保意义。
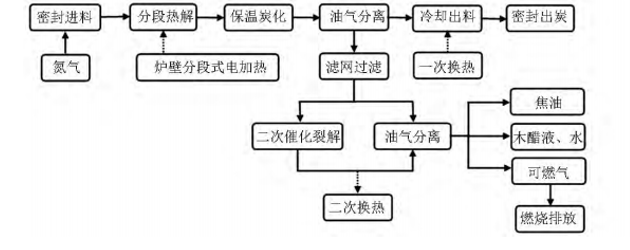
连续生物质碳化工艺流程图
参数 | 数值 |
外形尺寸(mm) | 5000x3000x2600 |
原料处理量/(kg·h-1) | 0~30 |
设备总功率/kW | 45.5 |
炭化温度/℃ | ≤700 |
催化/高温裂解温度/℃ | ≤1200 |
热解升温时间/min | 5~60 |
加热方式 | 电阻丝外源加热 |
分段式炭化炉是设备的关键组件,其设计理念涵盖了多段式设计和螺旋输料器的精确尺寸计算。这种多段式设计的主要目的是通过精细控制每一段的温度,形成预设的温度场,确保生物质原料在热解过程中以理想的升温速率进行炭化。这种设计旨在模拟符合热解机理的温度场,从而优化生物炭的得率和品质。
理论上,热解筒壁的分段越多,热解温度场的变化趋势将越趋于平缓,这有助于更精确地控制热解过程。然而,在实际应用中,必须考虑筒壁导热、热解气对流传热等潜在误差的影响,以及各段之间连接处的密闭性问题。综合考虑这些因素,设计者最终选择将筒壁分为5段,并采用法兰连接,同时在法兰之间加入绝热板以减少筒壁的导热损失。
热解炉是生物质原料热解炭化过程的核心热源。在热解过程中,能量消耗主要包括生物质原料的炭化升温、液相产物的潜热和显热、挥发分析出时带走的热量以及炉体自身的散热等。这些能量消耗需要精确计算和有效管理,以确保热解过程的顺利进行和能源的高效利用。
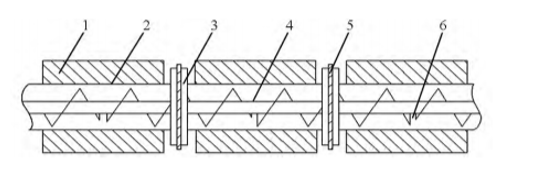
图:分段式炭化炉示意图
1.加热炉2.热解筒壁3.连接法兰4.螺旋输送器5.绝热环6.螺旋缺口
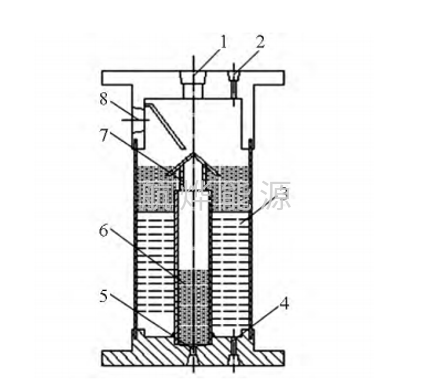
三相分离器
1.出气口2.液位计回流口3.水腔4.出水口5.出油口6.油腔7.浮斗8.进气口
热解炉产生的热解混合气包含多种成分,如水、焦油和不可冷凝气体等,因此需要进行有效的分离和收集。这一过程中,我们采用了分级冷凝原理,根据各成分的冷凝点不同,逐步将它们分离开来。在约200℃的分离罐中,水和轻质油保持气相状态,而焦油则由于其复杂的成分在此温度下冷凝成液相,从而被收集到储油罐中。
热解气经过油气分离后,仍含有水、不可冷凝气体和少量轻质油。为了进一步分离这些成分,我们使用了循环水冷却将热解气降至室温,并导入三相分离器。三相分离器基于不同组分的密度差异进行分离,使轻质油漂浮在水的上层,经特定结构进入油腔排出,而水则从另一出口排出。
此外,为了提高热解设备的系统性和效率,我们引入了催化裂解炉。通过三通阀的切换,热解气可以选择进入冷凝分离装置或催化裂解炉。催化裂解炉采用5段炉设计,每段都能单独控制温度范围在20~1100℃,内部设有可拆卸支撑板用于装填催化剂。热解气从上端进入炉内,经过催化剂的催化裂解后从下端排出。裂解炉前后设有取样口,便于分析催化裂解效果。
炭化炉后端连接了生物炭水冷装置,通过斜螺旋套筒内的循环水对热解后的生物炭进行冷却。以初始温度500℃的生物炭为例,利用0.0481m³/h的循环水可将其降至60℃以下,确保安全收储。同时,循环水在换热过程中从20℃升至40℃。
为了准确监测生物质热解过程中的温度,我们采用了插入式安装的热电偶。通过在螺旋绞龙特定位置进行环切,将热电偶插入到物料层25px深处进行测温,从而避免了由于炉壁热阻引起的误差。
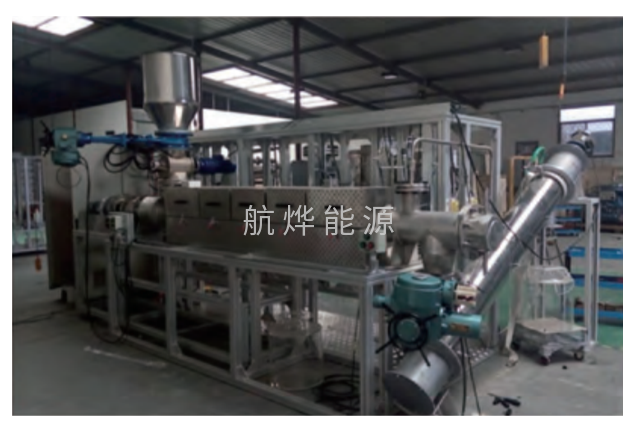
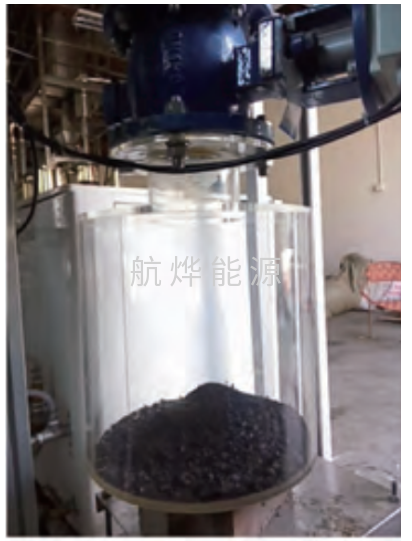
连续式分段热解炭化设备试验图