机封改磁力密封应用及改造案例(1):轻柴油泵泄漏故障分析
一款单级悬臂离心泵,其运行转速设定为2950转每分钟,负责将轻质柴油从成品储罐中抽出,并传输至油槽车内,操作环境温度为室温条件。此泵的设计特点包括:入口压力维持在低于0.05MPa的水平,而出口压力则不超过0.3MPa。该泵采用的密封组件型号为GX45,由国内厂家专为其配套生产。其中,动环选用1Cr13材质并在其表面进行了硬质合金堆焊处理,以增强耐磨性;静环则采用石墨浸渍合成树脂材料,确保良好的密封性和耐腐蚀性。此外,动环与静环均配备了4F-V型的密封圈。值得注意的是,密封腔的工作压力与泵入口压力相同,均低于0.05MPa,且该泵在运行时无需冲洗、紧急冷却或其他辅助设施支持。
该泵服务于油品车间的装车流程,采用间歇操作模式。在一年多的稳定运行中,其密封性能一直保持良好。然而,在A罐油品抽送完毕后停机,转至抽送B罐油品时,泵刚启动便遭遇了严重的泄漏问题。技术人员随即对泵进行了拆解检查,发现密封面磨损极为严重,动环表面甚至出现了变色现象。此外,动环与静环的表面均呈现出环状沟纹,但并未观察到径向裂纹。同时,密封圈已变为黄色,且静环上的两个密封圈相互粘连。
改进方案:机封改磁力密封。
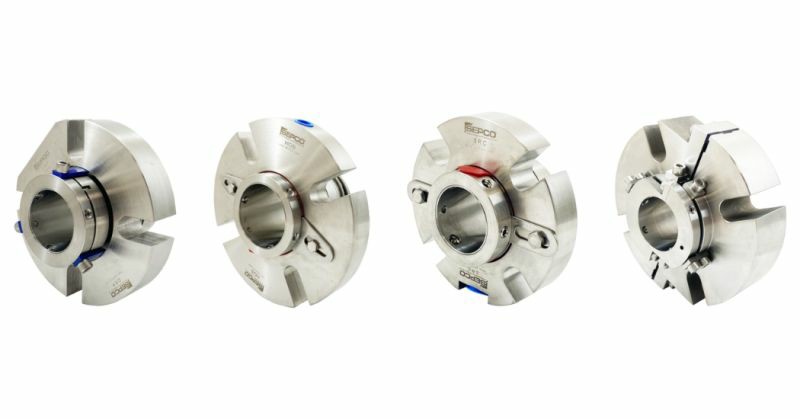
机封改磁力密封应用及改造案例(二):离心泵石墨环断裂故障分析与改进
双支承热油泵,从焦化分馏塔底抽出,打到加热炉中去升温。泵入口温度约 380℃,泵入口压力 0.1~0.2MPa,出口压力 3.0~3.4MPa,流量 180m3/h介质为减压渣油,转速2950r/min,用汽轮机驱动。
这是一台离心泵,其特点在于泵壳采用垂直剖分的双层设计,外层为碳钢材质,而内层壳体及叶轮则选用不锈钢材料制成,泵轴则是由Cr17Ni2合金打造。该泵轴上配置了七只同向入口的叶轮,并通过平衡盘来有效平衡轴向力。
在轴封方面,该泵两端均采用了机械密封技术,具体型号为英国制造的克朗109B。其中,动环材质为石墨,静环则选用合金铸铁,而动环垫则设计为楔形状。为了保持密封效果,该泵还采用了注入式冲洗方式,冲洗液选用的是温度约为90℃的蜡油。此外,泵体夹套内通有冷却水,而压盖部分则设有急冷水装置。
长期实践证明,无论是泵还是密封都能满足工作条件的要求。但在相当长一段时间内,每次开工,该泵都不能顺利投用,影响到全装置不能正常生产。主要的原因是密封泄漏严重,而且大多是入口端的石墨环断裂。
在启动汽轮机和热油泵之前,预热步骤是必不可少的。预热过程中,首先需要确保泵的出口阀门处于关闭状态,随后打开预热阀门,并轻微开启泵的入口阀门。这样,热油便能通过预热阀门流入泵体,并最终通过入口阀门进入系统中循环。为了防止密封部件因高温受损,在预热的同时,还需向泵的两端密封注入封油,流量控制在4至5t/h之间,这些封油会流经泵体并最终汇入入口管道中。
当检测到入口管道法兰的温度超过280℃时,便可以启动泵了。此时,外壳表面的温度大约在240℃左右。启动泵时,需要关闭预热阀门,并适当增大入口阀门的开度。接着,启动已经预热充分的汽轮机,并逐步增加转速至正常水平,随后再打开出口阀门。整个启动过程大约需要30-50分钟。
在泵启动的过程中遇到了一个问题:在启动之前,预热阀门被错误地关闭了,这导致热油供应被切断。而在启动过程中,为了保持密封,持续注入了温度为90℃的封油。这一做法实际上对已经预热至280℃以上的泵体产生了冷却效果。实际测量数据也反映了这一点,入口法兰的外表面温度从280℃显著下降到160℃至170℃,泵体的表面温度也从240℃降低到了190℃至200℃。
再者,当出口阀门被打开后,泵的流量迅速达到120-140m3/h。在这个过程中,原先为保持密封而注入的封油仅在1-2min内就被完全排出,紧接着,380℃的高温热油开始流入。由于转子被热油包围且泵采用双层壳体设计,转子温度的提升速度远高于泵外壳,导致在短短几分钟内,转子和泵外壳之间产生了120℃至140℃的温差。这种温差引起的热伸长现象在转子上表现得更为显著,超过了泵壳的热伸长。值得注意的是,无论是转子还是泵外壳,它们都以出口端的平衡盘作为“参考点”向入口端膨胀。经过计算,两者之间的热伸长差值达到了2.58mm。
由于机械密封的构造特性,其中静环被固定安装在壳体上,而动环则装配在轴上。当轴与外壳因热膨胀产生2.58毫米的差异时,这相当于在原有密封压缩量的基础上额外增加了2.58毫米。考虑到密封安装时的初始压缩量已经是3.6毫米,两者相加使得总压缩量达到了6.18毫米。然而,克朗109B密封的设计极限压缩量仅为5.0毫米,一旦超过这个极限,动环(由石墨制成)就会在传动座与静环(由合金铸铁制成)之间受到过度的挤压。这种过度的压力最终会导致动环在楔形垫的作用下发生断裂。
经过深入分析,我们发现入口端密封在安装时的压缩量已经相对较大。在启动过程中,由于轴的膨胀量大于壳体的膨胀量,使得密封的压缩量进一步增大,直至超过其极限值,这是导致密封失效的主要原因。此外,整个启动过程需要30到50分钟,期间为了保持密封而注入的封油不仅未能起到预期的作用,反而冷却了已经预热的泵体,从而使得预热步骤失去了其应有的效果。
改进方法:机封转磁力耦合密封,再没有发生石墨环断裂的故障,使装置顺利投产。
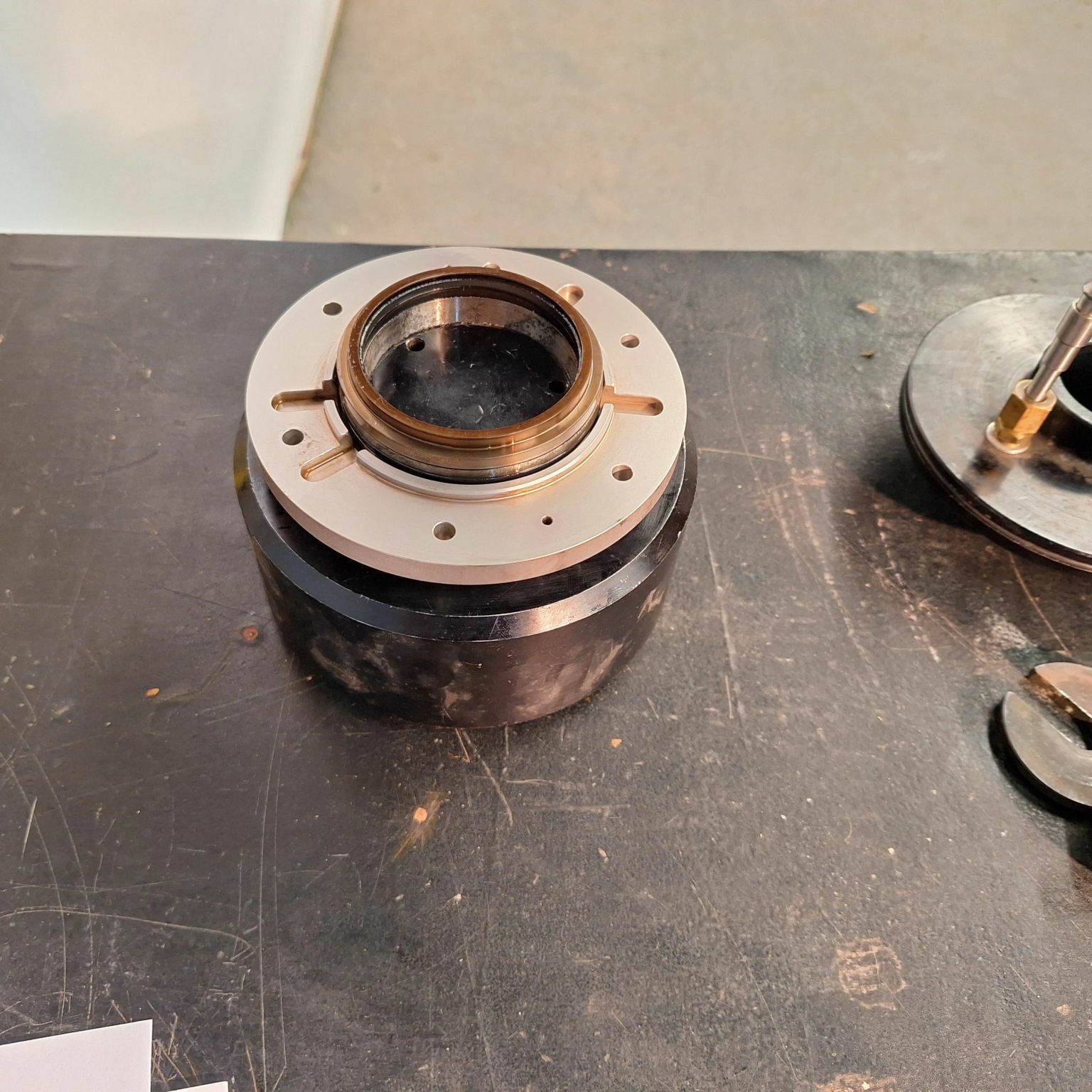
机封改磁力密封应用及改造案例(三):苯酐泵泄漏故障分析与改进
有一台单级悬臂式离心泵,其转速高达2940转/分钟,专门用于输送温度范围在250至260℃的苯酐介质,且泵入口处的压力维持在0.1至0.2MPa之间。该泵配置了103型机械密封系统,其中动环由18-8不锈钢镶嵌碳化钨硬质合金构成,而静环则采用石墨浸渍合成树脂材料。密封系统的动静环密封圈均设计为4F-V型,且未设置冲洗、急冷或其他辅助设施。
尽管已多次尝试更换密封件,并怀疑是由于压缩量不足导致的问题,但即便将压缩量从3至4毫米增加至7至8毫米,问题依旧未能得到解决。在泵刚启动时,密封及泵的运行状态均表现良好,无任何泄漏迹象。然而,当泵持续运转约10分钟后,开始出现滴漏现象,并且泄漏量逐渐增大,从最初的每分钟10至20滴,发展到后来的每分钟60至70滴。拆开泵体检查后,发现动静环的表面依然光洁无损,其他相关零件也未见异常。
深入分析后发现,泵启动初期,密封处的温度相对较低,因此密封效果良好。但随着时间的推移,密封处的温度逐渐升高,直至接近泵内介质的温度(250℃)。由于动环的环座采用的是18-8不锈钢材料,其线膨胀系数高达17.2x10-6℃-1,在工作温度下,环座的膨胀量可达0.3至0.4毫米。相比之下,碳化钨的线膨胀系数则较小,仅为(4.5~5)X10-6℃-1,对应的膨胀量为0.1至0.15毫米。而热装时的过盈量更是不足0.1毫米。因此,当温度升高时,两者的过盈连接出现了间隙,导致碳化钨环松脱,介质得以从这一间隙中泄漏出来。
为了验证这一结论,我们将动环放入烘箱中进行加热。当烘箱内的温度达到240℃时(约30分钟后),取出动环进行检查。此时,可以明显看到环座与碳化钨已经分离。进一步观察发现,环座与碳化钨环接合的部位存在磨损的痕迹和油迹,这充分证明了热装式动环的失效是由于环座选材不当以及过盈量过小所导致的。
改进方法:机封改磁力密封。
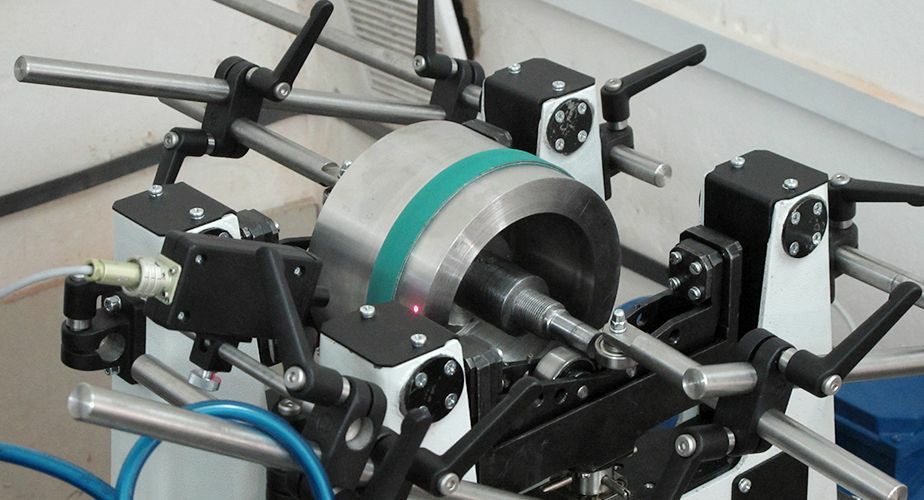