机封改磁力密封应用及改造案例(八):分子筛进料泵机械密封改造
分子筛进料泵负责输送常温下的航空煤油,其电动机转速达到2950转/分钟,出口压力设定为0.6兆帕。然而,自该泵投入运行以来,密封泄漏问题频发,这对分子筛装置的正常生产构成了严重威胁。一旦分子筛的原料油供应中断,整个分子筛系统的两套装置都将不得不全面停产,原因如下。
4月11日更换密封,密封损坏原因是波纹管断裂;
5月10日更换密封,密封损坏原因是波纹管断裂;
6月1日更换密封,密封损坏原因是波纹管断裂,为了防止波纹管断裂改为弹簧密封;
7月21日更换密封,密封损坏原因是密封圈老化;
8月5日更换密封,密封端面干烧严重,叶轮备帽松动;
8月12日更换密封,叶轮备帽松动。
面对密封频繁泄漏的难题,工作人员首先进行了自我反思,并对从密封安装到泵体安装的各个环节进行了全面而细致的检查,但均未发现异常。在排除了安装问题的可能性后,他们开始将注意力转向工艺流程。
在检查工艺流程的过程中,工作人员首先逐一核查了工艺管线的各个入口阀门,确认它们是否全部处于开启状态,但并未发现任何问题。随后,他们怀疑泵的入口罐液面可能是假液面,但经过实际检查,罐内液面一切正常。最终,他们在泵的出口处发现了一个由仪表控制的调节阀。这个调节阀的作用是在罐内液面降低时自动关闭,以防止液体继续流出。然而,这也意味着当这个调节阀关闭时,泵的出口阀门实际上也处于关闭状态,导致泵内产生涡流,泵体开始迅速升温。随着温度的急剧升高,密封液膜开始汽化,从而引发了密封泄漏。
解决方法:动密封改为静密封。
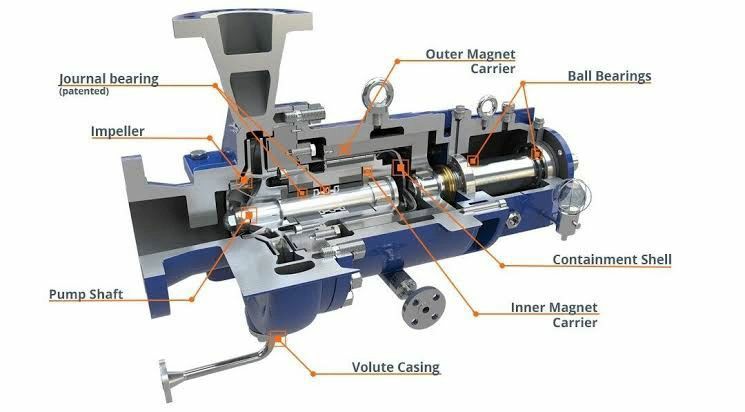
机封改磁力密封应用及改造案例(九):高压泵机械密封改造
在开工期间新安装的2台泵的机械密封在运转时相继泄漏,1个月就更换密封14套,如果这两台泵停将会造成后续的6个生产装置全部停产,后果不堪设想。
该工艺所采用的密封设计是旋转型波纹管密封结构,其中静环组件采用整体碳化硅(SiC)材料,并以浮装式方式安装。介质为特定流体,工作温度高达231℃,并且需要在2.3MPa的工作压力下运行。此外,泵的运行速度达到了每分钟2950转。
关于机械密封的自冲洗方式,系统配置了一个自身带有冷却罐的冲洗系统,该系统能够将冲洗液冷却至大约115℃。然而,机械密封的冷却则是通过背冷式方式实现的。遗憾的是,由于缺乏有效的水封密封措施,这一冷却系统的效能并不理想。更为严重的是,机械密封的冷却水中积累了大量的垢体,这进一步影响了冷却效果。
故障分析:
自冲洗系统缺陷:机械密封的自冲洗系统配备了自身冷却罐,但冲洗压力仅由3mm孔板控制,缺乏调节阀,导致冲洗液温度过高。这一设计上的不足影响了冲洗效果。
水垢积累问题:机械密封的水垢问题极为严重,泵在运行仅40小时后,波纹管的波纹就被水垢填满,导致机械密封失去了补偿能力,进而因失弹而发生泄漏。
静环安装与结垢:静环采用浮装式安装,其密封圈为膨胀石墨梯形环。背冷式的冷却方式使得静环表面也遭受了严重的水垢积累。
泵结构差异:国产泵与进口泵在密封腔设计上存在显著差异。国产泵密封腔配备有冷却水夹套,能有效降低密封腔温度;而进口泵则没有此设计,导致231℃的介质直接作用于机械密封上,使得密封腔温度过高,加剧了密封水的结垢问题。
冷却水质量问题:密封的冷却水采用循环水,其中含有钾、镁、钙、钠、硅等有害元素。这些元素在高温下容易附着在密封的金属表面,造成波纹管堵塞。
动环与轴套间隙及冷却问题:进口密封的动环与轴套径向间隙仅为0.7mm,且冷却方式仍为背冷式,仅冷却静环背部。冷却水部分进入波纹管,部分向外侧泄漏,导致波纹管迅速结垢,波峰波谷堵塞失弹,造成密封泄漏。此外,该密封设计复杂,增加了钳工安装的难度。
综上所述,机械密封泄漏的主要原因是:
①进口机械密封结构不适应该工况条件
② 冷却水存在严重问题。
③ 冷却系统的冲洗量存在问题。
解决方法:机械密封改磁力密封
机封改磁力密封应用及改造案例(十):多级液态烃泵机械密封改造
该泵的结构设计采用了10级分段式构造,两端则装配了滑动式轴承以支撑其运转。为了平衡轴向推力,该泵特别配置了平衡盘以及分块式止推轴承。
泵的转速设定为2490转/分钟,其入口压力为0.7兆帕,而出口压力则提升至1.4兆帕。在密封方面,该泵采用了双端面机械密封,每组密封都由平衡型和非平衡型两种类型组合而成。
该泵所输送的介质为液态烃,这是一种具有易燃易爆特性、渗透性强、润滑性差以及液化压力高的特殊物质。液态烃的这些特性导致其在泵端面上难以形成液膜,并且容易结冰霜,这些冰霜会破坏机械密封的动静环端面,进而影响到密封性能。因此,液态烃泵的泄漏问题一直备受关注,需要采取特别措施来确保其密封效果。
其中的两台泵机械密封发生多次泄漏,经组织人员对设备进行抢修,共更换机械密封12套。密封损坏原因为波纹管断裂。为了防止波纹管断裂经研究将两台泵的波纹管密封改为弹簧密封。同时,通过与生产部门商议调整了泵的排气条件,在出口压力表处排气,从而使泵体内无气体存留,采用此方法排气后,该泵正常运转4年多均没发生密封泄漏现象,泵运转良好。
泄漏原因:
该泵所输送的烃类介质,因其低温易挥发的特性,常导致密封系统出现结冰、干磨、汽化等故障,进而引发泄漏。此类问题在全国范围内屡见不鲜,主要诱因如下:
工艺条件因素:工艺条件对机械密封的稳定运行至关重要。启动泵之前,若泵内及进出口管线内积聚大量气体,会导致密封端面瞬间开启。因此,必须执行引液排气操作,确保泵内介质充盈。然而,在实际操作中,由于泵出口缺乏排气阀,气体无法充分排出,泵在启动时容易振动并产生汽蚀。对于液态烃泵而言,排气不畅是造成机械密封泄漏的关键因素之一。由于气体主要从出口排出,因此泵出口侧的密封更容易发生泄漏。
介质供应不足与汽化:机械密封在运行过程中,若装置的工艺条件发生变化,可能导致密封冲洗液断流或介质供应不足,进而引发密封面液体汽化,造成密封干摩擦,最终导致泄漏。从更换下来的密封件来看,摩擦面严重受损,这是典型的介质供应不足导致机械密封干摩擦的案例。此外,机械密封结冰也是由汽液混合引起的。
机械密封质量问题:在两次泵的运行中,机械密封发生了泄漏,这是由于波纹管泄漏造成的。多年的实践经验表明,波纹管密封在液态介质中的适应性较差。特别是在泵抽空时,波纹管的摩擦副干摩擦扭矩增大,容易导致波纹管扭断,进而引发泄漏。
解决方法:机械密封改磁力密封
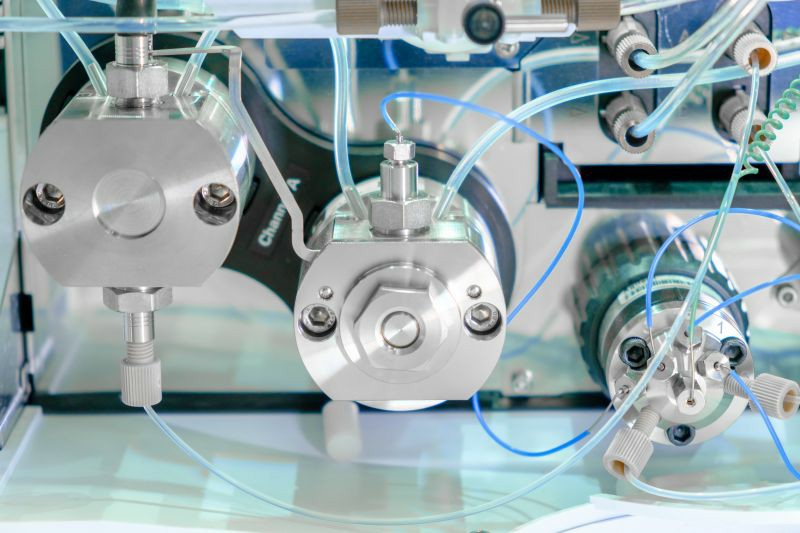