本公司专注于研发和制造固定床热解装置及费托合成催化剂评价装置,致力于推动生物质能源的高效利用与清洁转化。
固定床热解装置作为生物质能源转化的关键设备,具有高效、稳定、环保等优点,能够将生物质转化为高附加值的燃气或化学品。费托合成催化剂则是实现生物质能源向液体燃料转化的重要媒介,其高效催化性能可显著提升生物质能源的利用效率和经济效益。以下简单介绍几个应用案例。
1. 煤与生物质共热解反应装置/下落固定床热解装置应用案例:对废催化剂渣蜡热转化制芳烃的工艺优化
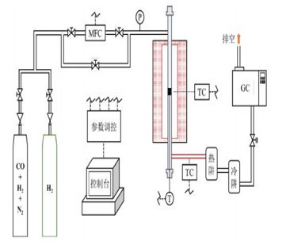
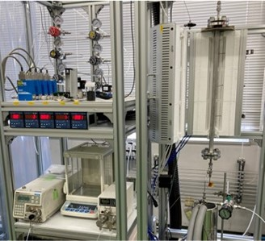
本工艺是通过固定床热解装置优化费托合成废催化剂渣蜡热转化制芳烃。
本装置主要由供气系统、进料系统、加热系统以及冷却系统组成。反应管材质为石英,最高耐热1000℃,反应管内径为30mm,长度为860mm,壁厚为3mm。
评价过程:设定载气流量流速下,以10-15℃/min将炉体加热到750℃,开始进料,进料完成后保温20min,热解产物进入收集装置,通过冷阱后产物可凝相溶入冷阱中的有机溶剂中,不凝气体部分进入气体收集装置。
工艺条件:原料粒度10-20目,反应温度为750℃,载气流速200mL/min,此时液相产物中芳烃的含量高达95%以上,气相组分中H2和CH4的含量高达30%。
2. 钴基费托合成催化剂
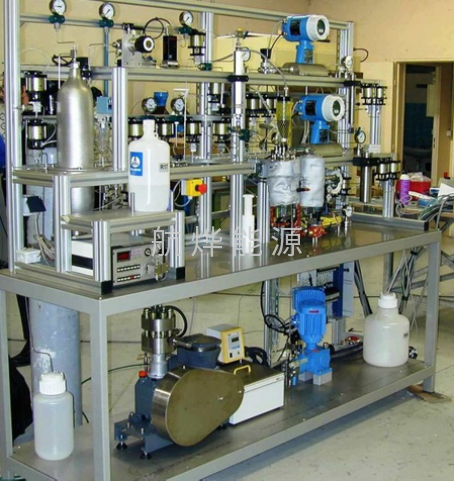
费托合成(FTS)是利用催化剂将合成气(CO和H2)高效转化为液体燃料和高附加值化学品的途径之一。钴基费托催化剂具有催化活性好、高稳定性和低水煤气变换活性的优点,广泛应用于费托合成工业开发中。
本设备由反应系统、进气系统、产物收集系统、分析系统和控制系统组成,反应器为内径为10mm的不锈钢管,产物收集由冷胫和热胫组成。
评价过程:在固定床反应器上,升温至200℃,随后切合成气升温到220℃,调节背压阀使反应管内压强保持在2bar,控制气体流速为30mL/min,1h后收集热肼(120 ℃)和冷肼(-1 ℃)的产物进行分析。
3. 费托合成装置/FTS装置应用案例:评价低碳烯烃制取工艺中四氧化三钴的催化性能
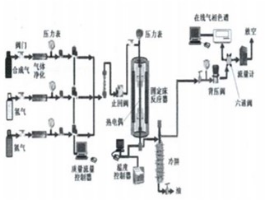
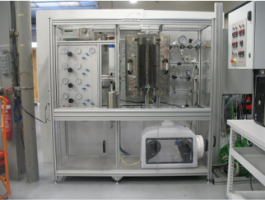
费托合成制烯烃的工艺流程较短、能耗较低,使用的原料气价格低廉,而Co3O4使用周期长、活性稳定且容易调节产物分布,适合作为催化剂使用。
本设备由包括原料气、固定床和色谱分析三部分组成。
评价过程:将催化剂和SiO2装入反应管,用N2排净管内空气,之后切换至还原气(气速76mL/min)。床层温度以2℃/min升至还原温度,常压条件下还原10h。还原结束后降温至80℃,用N2排空还原气后切换至反应气(气速38mL/min)。床层温度30min内升至指定反应温度,升温的同时关闭冷阱末端的截止阀,当压力升至0.4MPa时打开背压阀,最后分离回收液相产物进行分析。
4. 费托合成装置(FTS装置)应用案例:评价Fe系双组份催化剂的催化性能
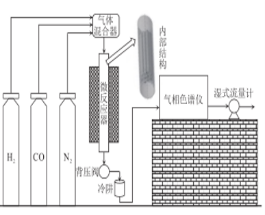
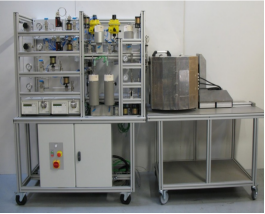
该设备通过正交试验设计,在微结构钢管(Fe)基体上,浸渍共活性成分(Mn、Co或Ce)制备了Fe系双组分催化剂(Fe-Mn:D1~D3,Fe-Co:D4~D6,Fe-Ce:D7~D9),从而与基体形成一体化微反应器。对催化剂在费托合成中的催化性能进行了评价,高温有利于提高CO和H2转化率,而低温有利于降低CH4选择性并提高C2~C4烃类选择性,C2~C4烃类收率几乎均在300°C达峰值,其中D3最高,达38.84%。
催化性能研究工艺条件:反应温度300℃、进料比V(H2):V(CO)=2:3、空速4000h-1、反应压力0.1MPa。
工艺流程:CO和H2分别由质量流量计控制其比例和流速,经气体混合器混合后进入费托合成装置(FTS装置),由控温仪控制程序升温并反应,产物经背压阀和冷凝器进入气相色谱仪,在线检测反应前后的气体组成。
5. 费托合成装置(FTS装置)应用案例:评价高负载率钴基催化剂的催化性能
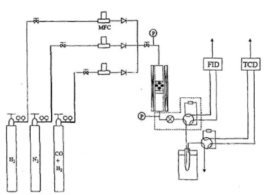
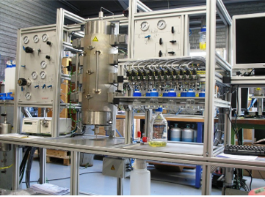
本设备以硝酸钴为钴源,正硅酸乙酯为硅源,采用甘氨酸作为交联剂、助燃剂和C、N前驱体,采用溶胶-凝胶碳化一氧化法,制备了一系列co/so2-scM 催化剂。
在碳化升温速率为 5℃/min,碳化温度为 400℃条件下,催化剂其金属钴负载量为 40wt%时,分散度达到 10.7%,且颗粒尺寸控制在 5.6±1.4nm。
FTS装置结构如下:
进气部分包括3路进气:分别为氢气。氮气以及一氧化碳与氢气混合器。H2(40mL/min)以10℃/min的碳化升温速率升温至170℃并保持0.5h,接着以5℃/min的碳化升温速率升温至400℃并保持5h。降温至120℃并将气路切换为合成气保持该温度调节背压阀使体系压力逐渐升至1Mpa压力,待体系的压力和流量达到稳定后,开始以5℃/min的碳化升温速率升温至目标反应温度进行反应。
6. 生物质连续热解反应器应用案例:用于松木和杨木的热解
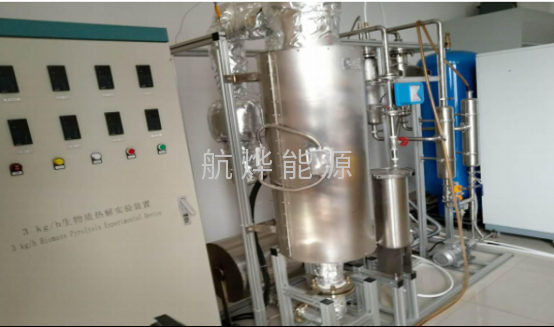
该设备由三部分组成:进料部分,热解部分,产物分离部分。
进料部分:固体由螺旋给料机进入热解炉,气体通过减压阀进入预热炉达到指定温度后进入热解炉中;
热解部分:三段加热炉,最大可达900℃;
热解产物分离部分:旋风分离器和冷凝器可实现固气分离。
工艺流程:99.99%氮气为载体,0.6mm的颗粒粒径的松木和杨木进入热解炉,到达530℃后,原料热解,产生的气体被带到冷凝器中,经由旋风分离器,分理出焦炭,再经冷凝器分别得到热解油和可燃气体,热解油的转化率均在57%。
7. 高压微型固定催化评价装置应用案例:松木杨木热解脱氧油催化加氢制备航空煤油的催化性能
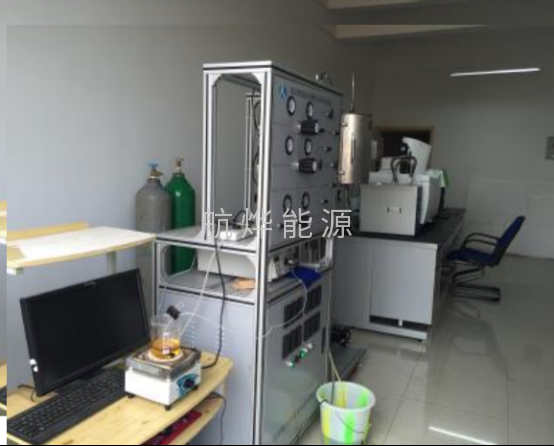
高压微型固定催化评价装置实物图
工艺流程:液体通过平流泵进入反应器内,在预热炉中气化后,随着氢气的流入进入反应器中,发生裂解反应后的气体进入冷凝器,冷凝后得到航空煤油产物。
工艺条件:在高温高压微型固定催化流化床上高温加氢脱氧,条件为温度403.92℃、氢压10.14MPa、空速1.39h-1、氢油比1200。烃的选择率为48.73%。
本公司的固定床热解装置和费托合成催化剂评价装置均经过严格的质量控制和性能测试,确保产品性能稳定、安全可靠。我们不断优化生产工艺和技术创新,提升产品的性能和使用寿命,以满足客户日益增长的需求。未来,本公司将继续加大研发力度,拓展生物质能源的应用领域,为推动能源转型和可持续发展贡献力量。我们期待与更多合作伙伴携手共进,共创美好未来。