硝化反应是在有机化合物分子中引入硝基的过程,广泛应用于各类工业生产。其中,芳烃硝化是生产基础化学品和特种化学品的重要反应,硝化产物常应用于染料、医药、农药、炸药等领域,同时,作为中间体,常用于合成酚及氟化物等。
18种危险化工工艺-硝化工艺
硝化反应是在有机化合物分子中引入硝基的过程,广泛应用于各类工业生产。其中,芳烃硝化是生产基础化学品和特种化学品的重要反应,硝化产物常应用于染料、医药、农药、炸药等领域,同时,作为中间体,常用于合成酚及氟化物等。
硝化反应是一种快速、强放热反应,引入一个硝基约放热150kJ/mol,反应过程若不能快速移除所放热量,极易因温度失控造成爆炸事故。此外,被硝化物本身不稳定,大部分被硝化物的燃点低、爆炸极限范围大,储存不当易引起火灾甚至爆炸;最常用的硝化剂-硝酸高温易分解,易造成冲料等危险;若硝化产物不稳定,受热或摩擦也易发生爆炸。
在传统工业中,芳烃硝化多采用釜式反应器进行等温硝化,利用搅拌器和冷却器维持恒定的温度,保证反应安全、平稳的进行。图1为多釜串联的芳烃等温硝化工艺示意图。反应时根据比例配制混酸溶液,然后芳烃和混酸进入串联釜反应,反应釜中设有强力搅拌装置,内部装有冷却管,以导出反应热;反应产物进入分离塔,塔顶分离出粗硝化产物,经纯化后得到产品;塔底分离出的废酸,经处理后可再利用。传统硝化工艺安全性低,控制不当易发生危险,并且自动化程度低、批次间重复性差、耗时长,人力和时间成本高。
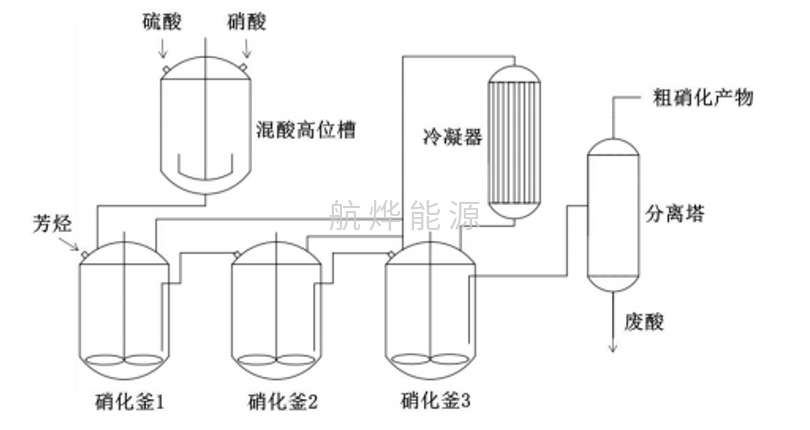
图1多釜串联硝化工艺流程示意图
传统硝化工艺存在的问题
(1)安全性差传统硝化反应器的热质传递效率低,为强化传质,多采用强力搅拌装置,若搅拌装置故障,会造成反应物料混合不均匀,产生局部热点,若再启动搅拌装置,反应将迅速发生,引发爆炸;同时,为控制反应温度,传统反应器中装有冷却盘管,若冷却装置故障,将导致温度急速上升,造成反应失控。
(2)反应时间长、生产效率低对于快速强放热的硝化反应,为增强生产过程的可控性,传统工艺一般采用向有机相中逐滴滴加硝硫混酸的方法来控制反应速率,因此生产过程时间成本高,生产效率低。
(3)产品质量不稳定,批次间不易重复传统硝化工艺副产物多、批次间重复性差,原因主要有三个:首先釜式反应器停留时间分布宽,导致先反应的原料在釜内停留时间过长,易生成串联副产物;其次,硝化反应物料配比要求严格,采用搅拌装置使反应物料进行混合时,很难使物料混合均匀,易发生磺化、过硝化等;最后,虽然釜式反应器内安装冷却盘管、釜外安装夹套进行降温,但由于反应釜体积大,釜内温度梯度大,温度难以精准控制,导致副产物增多,产品质量不稳定。
微反应器的反应通道特征尺寸为微米或亚微米,基于微反应器内部尺寸的微型化,使得微反应器与传统反应器相比,在传热和传质等方面有很大优势,且微反应器设备尺寸小,使得反应过程更加安全、经济,这些优势促使微反应器在化学化工领域有了更加广阔的发展前景。通过将传统化工与微反应器相结合,可节约反应时间、增加产品收率、提高生产过程的安全性,涉及的反应主要有:氧化、硝化、磺化、氟化、催化加氢等;除对现有化工系统进行微型化改造外,还可利用微反应器对反应机理进行研究,深入探索有机合成过程的机理。
对于快速、强放热的芳烃硝化反应,微反应器表现出显著的优势。基于微反应器大的比表面积,其温控效果好,可避免因温度控制不均而产生副反应,有利于提高产品收率和反应过程安全性。由于微反应器内物料可迅速混合均匀,因此反应时间可大大缩短,提高了生产效率。微反应器放大效应小,可实现反应从实验室到实际生产的快速转换,生产规模易于调控。
案例介绍:2 ,6-二乙基-4-甲基溴苯的合成
产物:2 ,6-二乙基-4-甲基溴苯
最佳工艺条件:2 ,6‑二乙基‑4‑甲基苯胺与醇的摩尔比为1:1~3;醇与酸的摩尔比为1:1~3;2 ,6‑二乙基‑4‑甲基苯胺与亚硝酸盐的摩尔比为1:2~5;2 ,6‑二乙基‑4‑甲基苯胺与溴化试剂总用量中溴元素的摩尔比为1:2~6;亚硝酸盐与酸和醇混合区域温度为5℃,停留时间为3.2s,2 ,6‑二乙基‑4‑甲基苯胺的预热区域温度为5℃,与溴化试剂的混合区域温度为45℃,停留时间为1.2s
合成路线:
图2氢-氯碱联产示意图
航烨能源与中科院携手并肩,历经多年磨砺,凭借坚实的技术基础和不懈的创新追求,专注于微通道和管式反应器的深度研发、创意设计、高效制造以及全方位安装服务。我们始终坚持以客户为中心,为客户量身定制系统解决方案,力求全方位满足您的需求。
我们深信,通过双方的紧密合作,我们必将共同推动硝化工艺领域的技术进步和产业发展,共创辉煌的未来。我们期待着与您携手共进,共同开创更加美好的明天!