随着世界经济的迅速发展,低碳烯烃及其下游产品的需求日益增加,以及清洁汽油生产要求进一步降低汽油的烯烃含量,促使炼油工艺中有关汽油回炼以及汽油单独再次反应的研究增多。现在全球大约70%的丙烯是由以轻质烃为原料的蒸汽裂解生产。其余部分主要由丙烷脱氢、易位转化、高碳烯烃裂解为丙烯、高苛刻度催化裂化(FCC)和甲醇制烯烃得到,其中催化裂化/催化裂解在全球丙烯增长方面起着重要作用。
18种危险化工工艺-裂解裂化工艺
随着世界经济的迅速发展,低碳烯烃及其下游产品的需求日益增加,以及清洁汽油生产要求进一步降低汽油的烯烃含量,促使炼油工艺中有关汽油回炼以及汽油单独再次反应的研究增多。近年来,有关这方面的研究大多停留在改质降烯烃方面,而在高温、短停留时间条件下,对催化汽油催化裂解多产低碳烯烃并对汽油改质的研究很少。
现在全球大约70%的丙烯是由以轻质烃为原料的蒸汽裂解生产。其余部分主要由丙烷脱氢、易位转化、高碳烯烃裂解为丙烯、高苛刻度催化裂化(FCC)和甲醇制烯烃得到,其中催化裂化/催化裂解在全球丙烯增长方面起着重要作用。
烃类在热的作用主要发生两类反应:一类是裂解反应,它是吸热反应;一类是缩合反应,它是放热反应。裂解方向产生较小的分子,而缩合方向则生成较大的分子。烃类的热反应是一个复杂的平行顺序反应,这些平行的反应不会停留在某一阶段上,而是持续不断地进行下去。随着反应时间的延长,一方面由于裂解反应,生成分子越来越小、沸点越来越低的烃类(如气体烃),另一方面由于缩合反应生成分子越来越大的稠环芳香烃,高度缩合的结果就产生胶质,最后生成碳氢比很高的焦炭。
催化裂化反应是各种烃分子经过多种类型的反应而生成另一种烃的过程,烃类在催化剂上所发生的各种催化裂化反应是通过正碳离子中间体进行的,所谓正碳离子是指含有一个带正电荷的碳原子的烃离子。正碳离子的生成和特性烃类在酸性催化剂表面主要通过烯烃在B酸中心得到质子(H+),烷烃在L酸中心失去负离子(H)和饱和烃通过非经典方法生成正碳离子。
在FCC反应过程中,催化剂酸性中心上的烃分子倾向于在第二或第三碳原子上形成正碳离子,而FCC的基本反应机理是正碳离子的链在β位键发生断裂(β断裂),生成α-烯烃,生成的长链烃进一步发生β断裂,直到其链短到一定程度为止。由于较短的链β断裂反应活性较低,所以一般来说汽油馏分内的烯烃不再进一步发生β断裂,从而产生大量的C5-C12烯烃,其中部分烯烃又会进一步通过氢转移反应被饱和。
催化剂
FCC以重油为原料,反应操作条件苛刻,要求多产丙烯FCC催化剂具有良好的热稳定、水热稳定性、机械强度和抗重金属污染能力,并且还要求稀土元素含量适中,酸强度较高且酸密度适宜,氢转移活性较低,对丙烯的选择性较高。在REHY,REUSY,USY,Y型沸石,ZSM-5等常用FCC催化剂中,ZSM-5的氢转移活性最低。由于烃分子的C-C键断裂需在催化剂的强酸中心上进行,所以提高强酸性中心的比例对增产丙烯有利。分子筛结构中的稀土元素含量对分子筛催化剂的活性和选择性有影响,稀土元素含量增加时,催化剂活性及氢转移活性均增强。
进料性质
从氢平衡角度看,氢含量越高的进料生产丙烯的潜力越大,原料的类型也是影响丙烯产率的重要因素。研究表明氢含量高的石蜡基原料丙烯产率几乎是环烷基原料的2倍。
反应时间
延长反应时间,可增加烃类的裂化,丙烯产率提高。缩短反应时间,可减少氢转移反应,使已产生的丙烯尽可能多地保留。在保证足够长的催化反应时间的情况下,要尽量缩短非催化反应时间,如提升管后的油气停留时间。可根据生产目的和操作条件选择合适的反应时间。
反应温度和剂油比
随着反应温度的升高,丙烯产率相应上升,但在固定转化率下,其上升幅度很小,并且反应温度对丙烯产率的影响实际上主要是通过改变转化率,即反应深度实现的。
案例介绍:2 ,6-二乙基-4-甲基溴苯的合成
先将一定量的催化剂装入反应器内,将反应器升温。当反应器密相温度达到180℃以上时,启动雾化蒸汽水泵。蒸馏水经蒸汽发生炉、原料油加热炉加热成<400℃的过热水蒸汽,进入反应器将催化剂流化。当反应器内温度达到反应温度时,启动原料油泵。原料油与水蒸汽一起经加热炉进一步加热后进入反应器,在反应器内,原料油与催化剂接触并进行反应。反应物与催化剂分离后,离开反应器进入产物冷却、冷凝、接收系统,停水泵,反应器降温,改用氮气吹扫,直至水蒸汽被扫净。然后,停止所有设备的加热,待反应器完全降温后,卸出结焦剂。
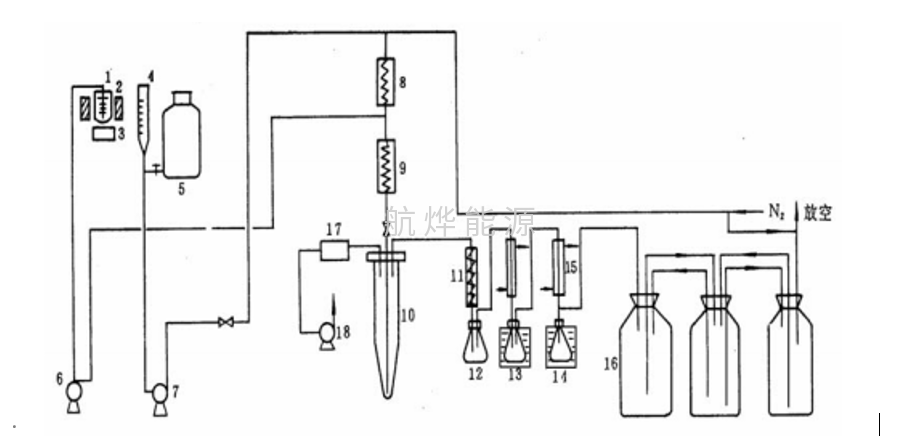
1—原料油罐2—原料预热炉3—电子称4—水计量管5—蒸馏水瓶6—原料泵7—水泵8—蒸汽发生炉9—混合加热炉10—反应器11—馏出管保温12—一级接收瓶13—二级接收瓶14—三级接收瓶15—冷凝器16—集气瓶17—卸剂系统18—真空泵
图1 固定流化床装置图